Condition-Based Maintenance (CBM) is a proactive maintenance strategy that focuses on monitoring the condition of assets in real-time to optimise maintenance activities. By leveraging data and analytics, CBM allows organisations to make informed decisions about when to perform maintenance, leading to improved reliability, reduced costs, and enhanced asset performance.
The Condition-Based Maintenance trifecta
A CBM process involves 3 key steps:
- Identification of critical assets and parameters to monitor: Identify the assets that have a significant impact on operations and determine the key parameters that need to be monitored to assess their condition effectively.
- Data collection, analysis, and interpretation: Utilise condition monitoring techniques such as sensor-based monitoring, vibration analysis, oil analysis, and thermography to collect data about asset condition. Analyse and interpret this data to identify patterns, anomalies, or potential issues.
- Decision-making and action based on condition assessment: Based on the analysis of the collected data, make informed decisions about maintenance actions. This may include scheduling maintenance tasks, performing repairs, or ordering spare parts.
Difference between Condition-Based and Predictive Maintenance
While CBM and predictive maintenance share similar goals, there are distinct differences between the two approaches:
Data analysis and maintenance actions
CBM focuses on monitoring specific parameters and triggers maintenance actions based on condition assessments. Predictive maintenance, on the other hand, relies on predictive algorithms and historical data patterns to forecast failures and schedule maintenance.
CBM offers the advantage of early detection of potential failures, allowing for timely maintenance and reduced downtime. Predictive maintenance, on the other hand, can provide more advanced warning and may be better suited for complex systems. Both approaches have their strengths and limitations, and the choice depends on the specific needs and characteristics of the assets being monitored.
Examples of Condition-Based Maintenance
HVAC system monitoring
In commercial buildings, HVAC systems are crucial for maintaining a comfortable indoor environment. A condition-based maintenance program can be implemented to ensure optimal performance and energy efficiency. Sensors and data analysis techniques are employed to monitor the condition of HVAC equipment.
For example, temperature and humidity sensors can be installed at various points in the system to collect real-time data. This data is then analysed to identify any deviations from the desired setpoints or abnormal trends. Additionally, airflow sensors can be used to monitor air volume and ensure proper ventilation.
Based on the analysis results, maintenance actions can be scheduled. For instance, if the analysis reveals decreased cooling capacity or reduced airflow, it may indicate issues such as clogged filters, refrigerant leaks, or fan motor problems. With the help of an Intelligent Maintenance Management Platform, maintenance alerts are generated when the analysed data exceeds predetermined thresholds, prompting technicians to perform targeted maintenance tasks like filter replacement, coil cleaning, or refrigerant recharging.
Lift maintenance
Lifts are critical components of multi-story buildings, and their reliable operation is essential for the smooth functioning of the facility. Condition-based maintenance can be applied to lifts using various monitoring techniques.
For example, lift systems can be equipped with sensors to monitor parameters such as motor current, door operation, travel time, and vibration. If the analysis reveals deviations from normal operating conditions, maintenance alerts are generated. For instance, increased motor current or abnormal vibration levels may indicate mechanical wear or misalignment. Similarly, issues with door operation or prolonged travel times can suggest problems with sensors, controls, or mechanical components.
Maintenance technicians receive these alerts and can take appropriate actions based on their severity. They can schedule maintenance activities such as lubrication, adjustment of mechanical components, or replacement of worn-out parts. By implementing CBM for lift maintenance, the facility can enhance lift reliability, reduce downtime due to unexpected breakdowns, and improve passenger safety.
Condition-Based Maintenance monitoring techniques
Condition-based maintenance relies on various monitoring techniques to assess the condition of assets and determine when maintenance actions are required. Here are some commonly used CBM monitoring techniques:
- Vibration Analysis: Vibration sensors are used to monitor the vibrations produced by rotating machinery such as motors, pumps, and turbines. Changes in vibration patterns can indicate misalignment, bearing wear, or other mechanical issues.
- Thermal Imaging: Infrared cameras are employed to capture thermal images of equipment and detect abnormal temperature patterns. Hotspots or temperature variations can signify overheating, electrical faults, or insulation degradation.
- Oil Analysis: Regular analysis of lubricating oil samples can provide insights into the condition of components such as bearings, gears, and engines. Oil analysis can detect contaminants, degradation, or abnormal wear particles, indicating potential equipment failures.
- Ultrasonic Testing: Ultrasonic sensors detect high-frequency sound waves emitted by equipment. This technique can identify leaks, electrical discharge, or mechanical problems like bearing defects or valve malfunctions.
- Acoustic Emission Testing: Acoustic emission sensors detect stress-induced microcracks and release of energy within structures or equipment. This technique is useful for assessing the integrity of pressure vessels, pipelines, and other critical assets.
- Electrical Signature Analysis: By analysing electrical signals and waveforms, electrical signature analysis can identify abnormalities in motors, generators, and other electrical equipment. It can detect issues like unbalance, insulation problems, or rotor bar defects.
Advantages and requirements of Condition-Based Maintenance
✅ Cost savings: By performing maintenance tasks based on asset condition rather than predetermined schedules, organisations can avoid unnecessary maintenance, reduce costs, and extend asset lifecycles.
✅ Improved asset reliability: Early detection of potential failures and timely maintenance actions ensure high asset reliability, minimise downtime, and enhance operational efficiency.
✖ Data collection and analysis: Effective CBM relies on accurate and timely data collection, which may require investing in monitoring equipment and ensuring proper data analysis capabilities.
✖ Implementation complexity: Introducing CBM into an organisation requires a comprehensive strategy, appropriate technology selection, and proper training of maintenance personnel.
Establishing a Condition-Based Maintenance programme
Setting a CBM programme involves several steps to ensure its successful implementation:
- Define Objectives: Clearly outline the objectives you want to achieve with your CBM program. These objectives could include minimising downtime, reducing maintenance costs, optimising asset performance, or increasing equipment lifespan.
- Identify Critical Assets: Identify the assets that are critical to your operations and would benefit the most from a CBM approach. These could be equipment, machinery, or systems that have a significant impact on productivity or safety.
- Select Appropriate Sensors: Determine the type of sensors required to collect data from your critical assets. Choose sensors that provide relevant information for detecting potential failures or performance deviations.
- Define Data Collection Plan: Establish a plan for collecting data from the selected sensors. This plan should outline the frequency and duration of data collection, as well as the methods for transferring and storing the data. Consider using technologies such as IoT (Internet of Things) devices or data loggers for automated and remote data collection.
- Establish Baselines: Gather historical data and establish baselines for normal operating conditions and performance parameters of your critical assets. These baselines will serve as references for comparison when analysing real-time data to identify abnormalities or potential failures.
- Set Thresholds and Alarms: Determine the thresholds or limits for various parameters beyond which equipment performance is considered abnormal or failure is imminent. When data collected from sensors cross these thresholds, alarms or notifications should be triggered to initiate maintenance actions.
- Implement Data Analysis Techniques: Apply appropriate data analysis techniques to the collected data to identify patterns, trends, and anomalies. This may involve statistical analysis, machine learning algorithms, or other diagnostic methods to detect early signs of equipment degradation or failure.
- Develop Maintenance Strategies: Based on the analysis results, develop maintenance strategies for each asset. This may include scheduling preventive maintenance tasks, condition-based inspections, or replacing components based on predictive indicators.
- Integrate with Maintenance Management System: Integrate the CBM program with your existing maintenance management system or create a new one if necessary. This integration ensures that data from sensors and analysis results are used effectively to plan, schedule, and execute maintenance activities.
- Continuous Improvement: Regularly review and evaluate the performance of your CBM program. Identify areas for improvement, such as refining data collection methods, adjusting thresholds, or enhancing data analysis techniques. Implement these improvements to optimise the effectiveness of the CBM program.
Intelligent Maintenance Platforms and Condition-Based Maintenance
Condition-Based Maintenance offers, as we see, significant benefits for optimising maintenance strategies and improving asset performance.
Intelligent maintenance platforms, such as Infraspeak, can play a crucial role in facilitating and enhancing the implementation of these strategies, through:
Data collection and monitoring
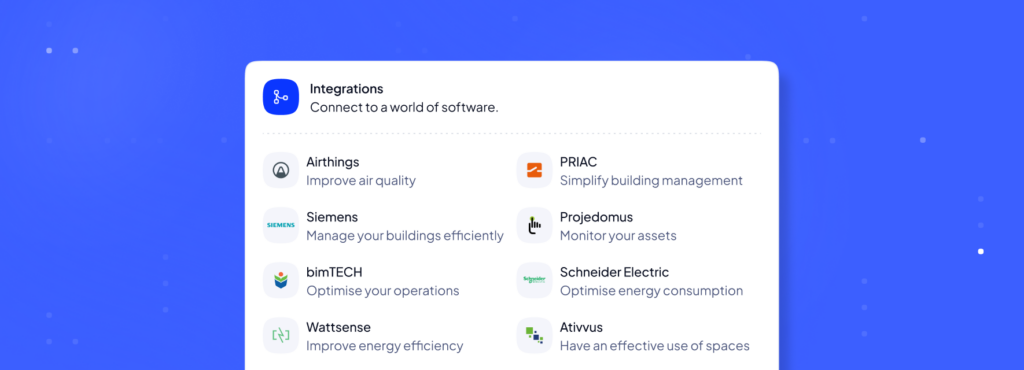
Intelligent maintenance platforms enable seamless data collection from various sensors, devices, and systems. They gather real-time data on equipment conditions, performance metrics, and environmental factors.
Centralised data storage and analysis
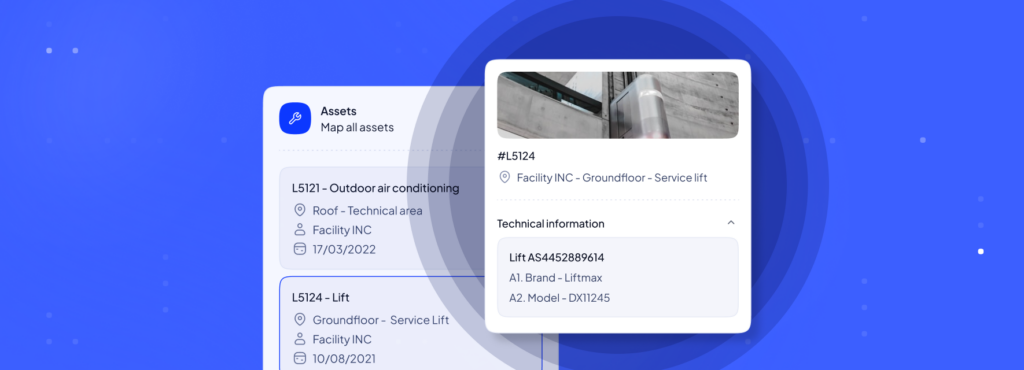
An IMMP stores and manages the collected data in a centralised manner, making it easily accessible for analysis. It employs advanced analytics techniques, including machine learning algorithms, to analyse the data and detect patterns, trends, anomalies, and potential failure indicators.
Maintenance planning and scheduling
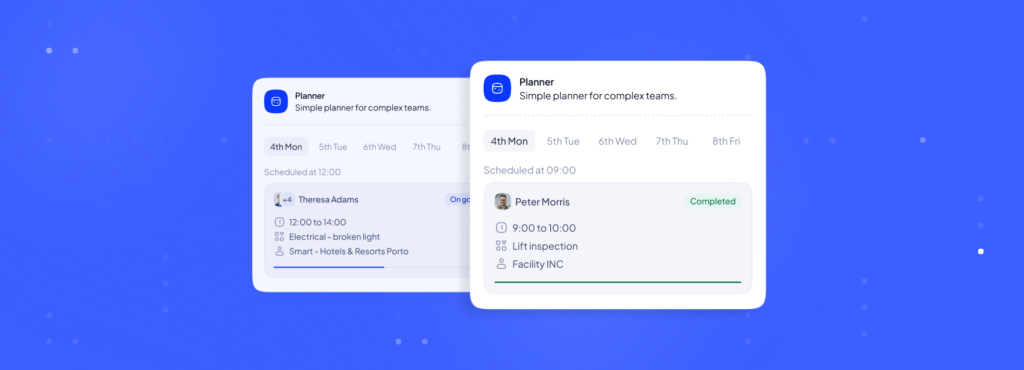
Intelligent maintenance platforms support effective maintenance planning by integrating CBM analysis results with maintenance management functionalities. They provide automated tools for generating maintenance alerts, work orders, and notifications based on the identified maintenance needs. This streamlines the planning and scheduling process, ensuring that maintenance activities are performed at the right time and with the right resources.
Condition monitoring dashboards and visualisation
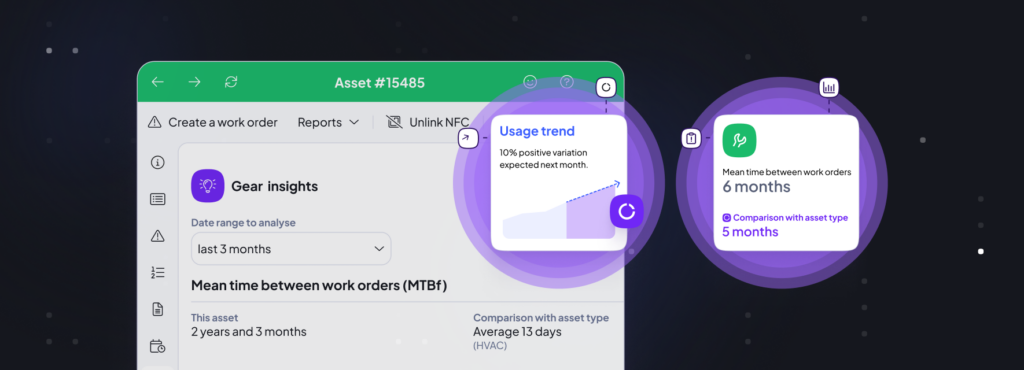
Infraspeak offers intuitive dashboards that present the condition monitoring data and analysis results in a clear and easily understandable manner. Maintenance teams can monitor asset health, track performance trends, and view real-time status updates.
Mobile capabilities and field service management
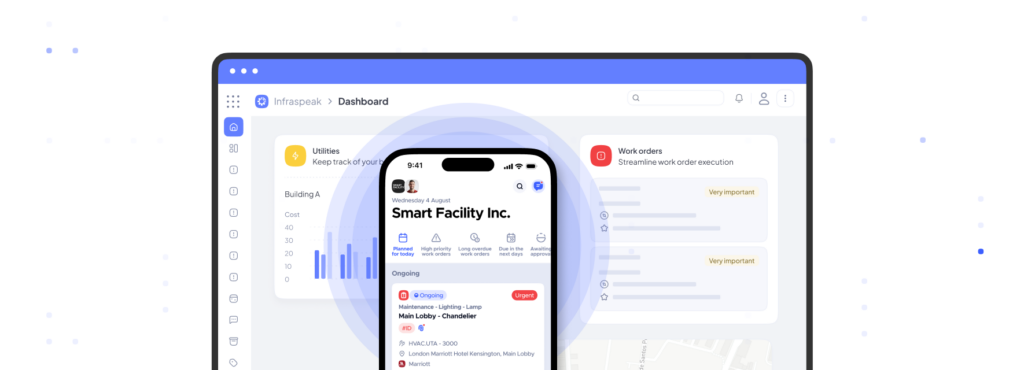
Intelligent maintenance platforms often provide mobile applications or interfaces that enable technicians to access and update information while in the field. This includes receiving real-time notifications, accessing work orders, documenting maintenance activities, and capturing asset data.
Historical data and performance analysis
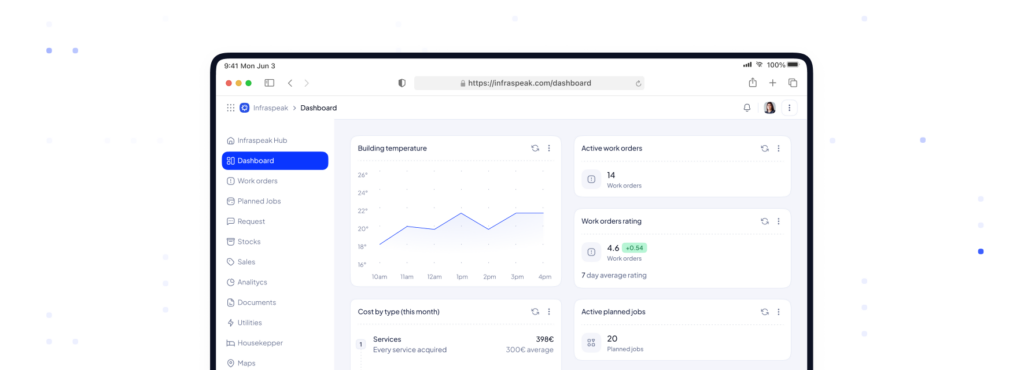
By storing historical maintenance data and asset performance records, intelligent maintenance platforms enable in-depth analysis of asset reliability, downtime patterns, and maintenance effectiveness. This historical analysis helps identify areas for continuous improvement, optimisation of maintenance strategies, and long-term asset management decisions.
- Improved efficiency in facility management.
- Better visibility into asset and team performance.
- More informed and data-driven decision making.
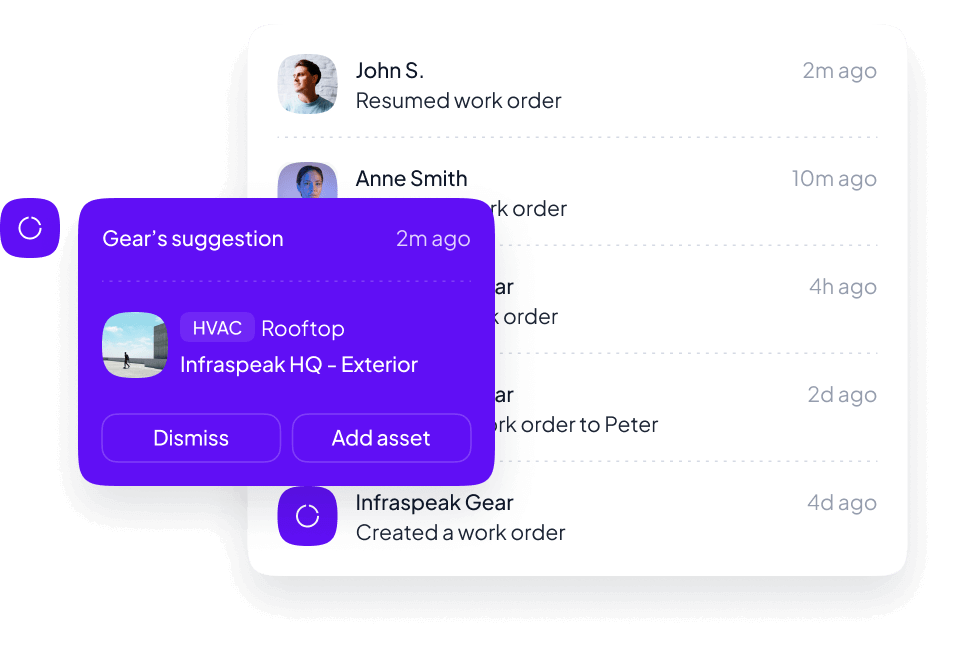