Idle time refers to periods when machines or equipment are available but not actively engaged in productive work. The term is also used to characterise full-time employees who are officially working but not engaged in productive tasks, nor actively contributing to productive work.
Efficiently managing idle time is, therefore, crucial for optimising efficiency and productivity.
Main factors contributing to idle time
- Lack of work or tasks: This can happen due to factors such as low demand, seasonal fluctuations, or delays in the workflow.
- Equipment maintenance: If machinery, equipment, or tools necessary for performing tasks require maintenance, it can result in idle time. Repairs, adjustments, or waiting for replacement parts can all contribute to downtime.
- Inefficient workflow or process bottlenecks: If there are delays in receiving necessary inputs or if there are unnecessary waiting periods between tasks, idle time may occur.
- Staffing issues: Insufficient staffing or imbalances in workload distribution can result in idle time. The same applies to when there are more employees than required for a specific task or if there is a lack of coordination among team members.
- Waiting for approvals or feedback: When teams are waiting for approvals, feedback, or decisions from superiors or clients, idle time can occur. Delays in the decision-making process can stall progress and result in unproductive periods.
- Inadequate planning or scheduling: Poor planning, unrealistic deadlines, or inadequate scheduling of tasks also play a significant role.
- External dependencies: When an organisation or individual relies on external factors or entities to complete their tasks, delays or issues with those dependencies can result in idle time. For example, waiting for suppliers or approvals from external agencies.
Difference between idle time and uplanned downtime
The key difference between idle time and unplanned downtime is the underlying cause.
Idle time and unplanned downtime are related concepts but have slightly different meanings in different contexts. As we’ve noted, idle time refers to periods when resources or individuals are not engaged in productive activities despite the availability of the asset. Unplanned downtime, on the other hand, refers to the period when equipment, machinery, or systems are not operational or unavailable due to unexpected failures, breakdowns, or malfunctions. It is an involuntary interruption in the normal functioning of equipment or systems.
How to calculate idle time
The calculation of idle time can vary depending on the context and the specific situation you’re analysing. However, here is a general formula that can be used:
Idle Time = Scheduled Production Time – Actual Production Time
Scheduled Production Time is the planned duration for a running equipment/resource.
Actual Production Time is the actual time during which the equipment/resource operates as intended.
Examples of idle time in production
Equipment changeover
When transitioning from producing one product to another, the machinery or production line may need to be reconfigured or adjusted. During this changeover period, the equipment is idle and not actively producing any goods.
For instance, let’s consider a manufacturing facility that produces different types of bottles. Switching from producing plastic bottles to glass bottles requires reconfiguring the machinery, cleaning the production line, and making necessary adjustments. This changeover process may take several hours, during which the equipment remains idle.
Material shortages
Idle time can occur when there are shortages of materials or components required for production. If there is a delay in receiving necessary inputs or if the supply chain is disrupted, production may come to a halt until the required materials are available. During this waiting period, the production line or workers may be idle, leading to idle time.
For example, consider a car manufacturing plant that relies on a specific component from a supplier. If there is a delay in the delivery of that component, the assembly line may need to stop until the component arrives. The time between the depletion of the existing component inventory and the arrival of the new shipment contributes to idle time.
Managing idle time
To effectively manage idle time, accurate tracking and monitoring are necessary. This involves recording start and end times of idle periods, analysing the frequency and duration of idle time events, and identifying underlying causes. By closely examining idle time data, patterns and trends can be identified, facilitating informed decision-making for process improvements.
Scheduling maintenance during periods of low demand or non-production hours helps minimise the impact on overall productivity. Optimising changeover procedures through efficient planning and employee training reduces transition time between different production runs. Also, cross-training employees for versatile roles allows increased flexibility during periods of low demand.
Last, embracing automation and technology for an enhanced control further allows efficiency by streamlining operations and reducing occurrences of idle time.
- Improved efficiency in facility management.
- Better visibility into asset and team performance.
- More informed and data-driven decision making.
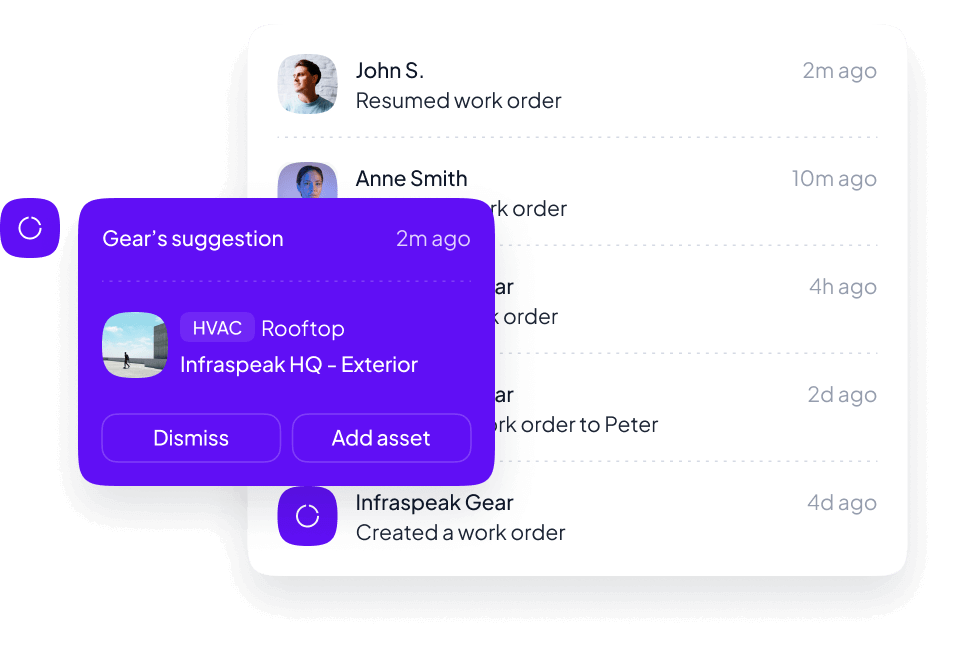