Unplanned downtime is an unforeseen event that halts the operation of a business, equipment, or system, resulting in lost productivity, revenue, and customer satisfaction. It can be caused by various factors such as equipment failure, power outages, natural disasters, or human error.
Consequences of unplanned downtime
Unplanned downtime can have severe consequences on any business, including:
- Lost productivity and revenue: Every minute of downtime can result in lost productivity and revenue, affecting a business’s bottom line.
- Decreased customer satisfaction: Unplanned downtime can lead to delayed deliveries, canceled orders, and frustrated customers.
- Equipment damage: Downtime can result in equipment damage due to the sudden stoppage or loss of control, leading to costly repairs or replacements.
- Safety hazards: Unplanned downtime can create safety hazards for employees and customers, leading to accidents or injuries.
FRACAS methodology and unplanned downtime
FRACAS (Failure Reporting, Analysis, and Corrective Action System) methodology is a proactive approach to managing unplanned downtime. It involves the systematic collection and analysis of data related to equipment failures to identify root causes and implement corrective actions.
The FRACAS methodology aims to improve equipment reliability, reduce downtime, and increase overall efficiency. By analysing failure data, businesses can identify trends and patterns, leading to predictive maintenance strategies and proactive equipment repairs.
Unplanned downtime and condition monitoring techniques
Unplanned downtime is closely related to condition monitoring techniques. Condition monitoring is the process of regularly monitoring the health and performance of equipment to identify any potential issues or failures before they result in unplanned downtime.
By using condition monitoring techniques such as vibration analysis, thermal imaging, and oil analysis, businesses can detect any abnormalities in equipment performance that could lead to unplanned downtime. For example, an increase in vibration levels in a piece of machinery could indicate a problem with a bearing, which, if left unchecked, could lead to a breakdown and unplanned downtime.
👷 You may also like: Asset management systems: which one is right for you?
Condition monitoring also enables businesses to perform maintenance activities on equipment based on its actual condition, rather than at set intervals. This approach, known as condition-based maintenance, can help businesses reduce maintenance costs and increase the lifespan of their equipment.
By implementing condition monitoring techniques, businesses can proactively manage their maintenance operations and reduce the risk of unplanned downtime. They can also improve equipment reliability, increase productivity, and reduce maintenance costs, making it a crucial component of any maintenance strategy.
Predictive maintenance and unplanned downtime
Predictive maintenance is an advanced maintenance strategy that uses data analysis and machine learning to predict equipment failures before they occur. By analysing historical data, businesses can identify potential equipment failures, enabling them to schedule maintenance proactively.
Predictive maintenance can help businesses reduce downtime, extend equipment lifespan, and lower maintenance costs. It involves regular equipment monitoring and data analysis, which can be time-consuming and challenging to manage manually.
How Infraspeak can help manage unplanned downtime
Infraspeak is a leading intelligent maintenance management platform that provides real-time equipment monitoring, predictive maintenance capabilities, and automated workflows, enabling businesses to proactively manage their maintenance operations.
Infraspeak offers features such as maintenance scheduling, work order management, asset tracking, and equipment performance monitoring. It also provides a mobile app that enables technicians to access maintenance information and complete work orders on the go.
In conclusion, unplanned downtime can have severe consequences on any business. However, with the right maintenance strategies and tools, businesses can proactively manage their maintenance operations and reduce downtime. The FRACAS methodology, predictive maintenance, and intelligent maintenance management platforms such as Infraspeak can help businesses achieve this goal.
- Reduce time-to-repair by up to 83%.
- Automate 60%+ of all admin work.
- Reduce unpredictable costs by up to 3.2x.
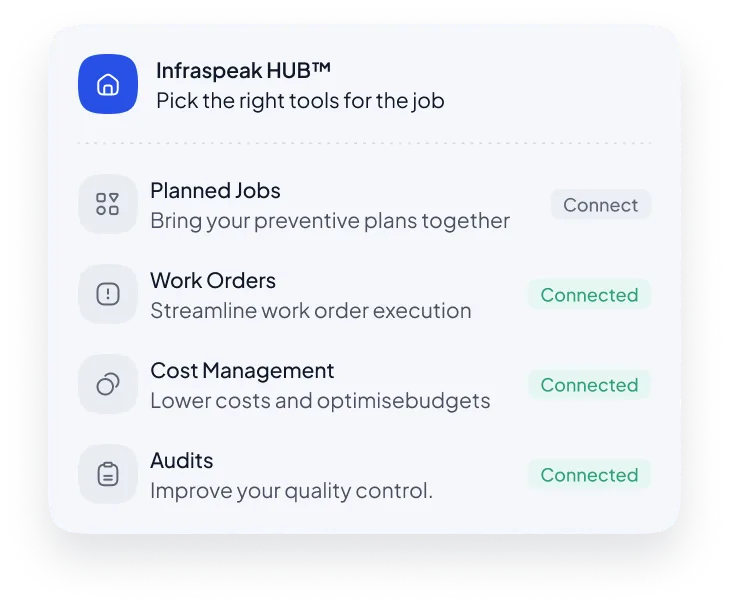