What is FRACAS?
Whenever people tell you to “learn from your mistakes”, that’s probably the last thing you want to hear. But here’s the thing: it doesn’t make it any less true. It’s always possible to turn a negative into a positive, even when you’ve been through the worst of failures.
So, even if failures cause downtime, outstanding expenses and lots of unwarranted drama, learn from your failures. And we didn’t come up with that. This process is actually known as FRACAS, which stands for Failures Reporting Analysis and Corrective Action System.
As the name indicates, it consists of three steps:
📝 Reporting – identify asset failures
⚙️ Analysis – learn from failure history
✅ Correction – take steps to fix failures and prevent them from happening again
The FRACAS loop step by step
1. Failure Modes and Effect Analysis (FMEA)
The first step of FRACAS is our old friend FMEA. To put it simply, take the equipment’s history and performance data to spot common failures. Then, list what causes each failure (failure modes), the impact it might have (effects), and how to handle each of them.
Here’s more about FMEA and how to perform one step by step.
2. Failure Code Creation
The second step is to create failure codes. Failure codes are short descriptions of what happened (an alarm went off, there was a bearing problem, a calibration problem or, in some sense, the failure modes). Using failure codes helps to prioritise failures, but it’s also extremely useful to monitor failures by category. Just beware of having a limited amount of codes – otherwise, technicians may not go to the trouble.
3. Work Order Analysis
Once again, you need accurate data to make a valid analysis. Check which failures happen more frequently (using the failure codes), completion notes, the work orders that take longer to resolve, what’s improving over time and what’s not. Work orders should be the first and most reliable source of information about failures, even though you can also check with technicians and ask for their feedback.
4. Root Cause Analysis
Wait… Isn’t FMEA a root cause analysis tool? Yes, you’re right, but it’s time to look at failures and ask why they’re happening. You can literally make a 5 Whys Analysis, use a fishbone diagram, FTA, or another type of root cause analysis. The goal is to understand the real source of the problem so that you can adjust preventive and predictive maintenance to stop it.
Download our complete guide to Root Cause Analysis here.
5. Strategy Adjustment
FRACAS is a Kaizen loop, which means steps repeat again and again, in an attempt to achieve continuous improvement. Monitor the outcomes, the failures at start-up, maintenance costs and maintenance hours by failure code, ask for the technicians’ feedback and implement changes that might improve your performance. Once you decide to try a new procedure, don’t forget to start small, with a single machine or a few pieces of equipment, in a PDCA cycle.
Even after you’ve assessed your results, there are a couple of other things you can do. One is creating reports to track the impact of the changes you’ve implemented (e.g. how much money you saved, how unplanned downtime is decreasing, etc). The other is auditing data. Don’t verify them one by one, but check if there are any odd work orders, red flags, and test if technicians are registering everything correctly.
Examples of FRACAS in maintenance
FRACAS is widely used in various industries to maintain critical equipment and systems. Let’s consider a manufacturing plant that relies on a large conveyor system to transport products between different stages of production. If a conveyor belt suddenly breaks down, the FRACAS process would be initiated:
- Reporting: The plant operator or maintenance personnel would report the conveyor belt failure to the maintenance department, providing details about the location, time of failure, and any relevant observations.
- Analysis: The maintenance team would investigate the failure by examining the broken conveyor belt, inspecting associated components, and reviewing maintenance records. The goal is to determine the cause of the failure, such as excessive wear, misalignment, or a structural defect.
- Corrective Action: Based on the analysis findings, appropriate corrective actions can be taken. This may involve replacing the damaged conveyor belt, realigning components, conducting preventive maintenance tasks, or implementing design modifications to enhance reliability.
- Tracking: Throughout the FRACAS process, all information related to the failure, analysis, and corrective actions would be recorded in the FRACAS system. This allows the maintenance team to track the status of the repair, monitor the effectiveness of the corrective actions, and identify any recurring issues that require further attention.
FRACAS and data reliability
FRACAS relies on accurate and complete data. If your data is not reliable, conclusions will not be valid. That is why we need to talk seriously about collecting as much accurate data as possible. However, data collection is a process in itself.
One of the things our clients share with us the most is that technicians would often forget to file reports, or forget details about their repairs.
Of course, relying on memory leaves very little accurate data to work with. On the other hand, if technicians are equipped with the right technology, they will record details on the spot, which significantly increases the amount of data you can extract from asset history and work orders. Using Infraspeak’s NFC tags, technicians can simply swipe their phones to clock into work and close a work order. We’ve also developed a mobile app so that they can be connected to the platform at all times.
Now, this does not mean your data will be 100% accurate. Technicians may forget to swipe and close the work order. They might log the wrong stock. But it significantly decreases the amount of human error, and gives you a margin of error that’s small enough to work with. Plus, a maintenance platform will generate automatic reports, which saves you time analysing reports and data. Here are a few things you can do to make sure the whole process is intuitive for the whole team and that data is easy to log:
- Make sure work orders are easy to fill and complete;
- Follow-up on failures that are not closed yet to guarantee that it’s not a mistake;
- Touchdown with technicians regularly to know which information they deem unnecessary, which parts of the process they struggle with the most, etc;
- As time goes on, review your processes to eliminate information that isn’t relevant anymore (because you’ve automated it, for example), and to see if there is something else you need to start requesting. Eliminate “noise” from work orders;
- Automate data collection with condition-monitoring sensors. These devices can be connected to your maintenance platform and you can check data in real-time.
It’s been a ride, but we feel like we definitely have a lot to learn from our mistakes. Pardon, from our failures. Remember: you can always count on Infraspeak’s intelligent maintenance management platform to collect better data and turn it into valuable insights!
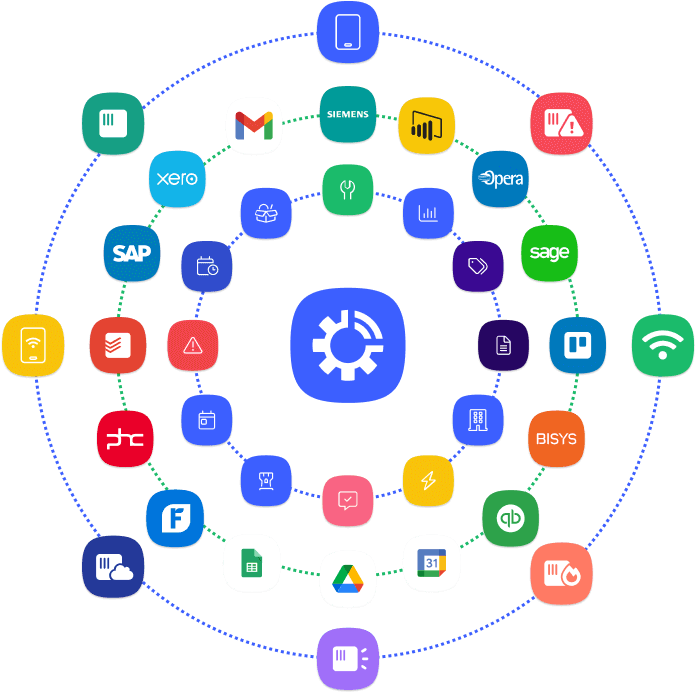