The desire to improve productivity and efficiency through machines or devices has been present since the great Ancient civilisations. Thousands of years ago in China, we found our first cases of documented automation. Machines powered by pulleys, hydropower, and trip hammers simplified tasks such as iron casting and grain preparation. These early inventors utilised physics, intelligence, and innovation to address one crucial question:
Can this machine make our lives easier and boost productivity? 🚀
At Infraspeak, we don’t use big wooden wheels, but we still get big results. We’re of course referencing Infraspeak Gear™ — the powerful processing core that sits in the centre of our facilities management platform.
It offers intelligent insights and suggestions based on platform data points, issues alerts when anomalies or errors are detected, and most importantly, automates thousands of administrative, recurring tasks that would otherwise be done manually, most likely by someone like you.
Stay with us for a deep dive into Infraspeak Gear™ automations. In this article, you will:
- learn why they’re important
- have an intro into building them
- study some key examples
- and finally, hear why we’re so excited
Let’s do this!
Automation 101: What, why and how?
Automation is defined by the Cambridge Dictionary as “the use of machines and computers that operate without needing human control”.
When it comes to our platform, automation refers to our solution’s capabilities to complete recurring, admin tasks without the need for human input.
They turn these tedious tasks into ‘done deals’ so you don’t need to lift a finger, saving you hours upon hours of time to do what really matters — we mean it — our clients save up to 7 hours a month on repetitive admin work using Gear automations, the equivalent of a standard working day. How does it work?
With 3 simple logical queues!
- Triggers: The starting point of the automation you’re creating
- Conditions: A rule or set of rules that influence what will eventually happen
- Outcomes: What do you want to happen as a result of your automation
Automation involves using different combinations of these elements that contain different data from the platform (cost centres, work order areas, asset category, clients, buildings, and more) in various orders. Here’s an example:
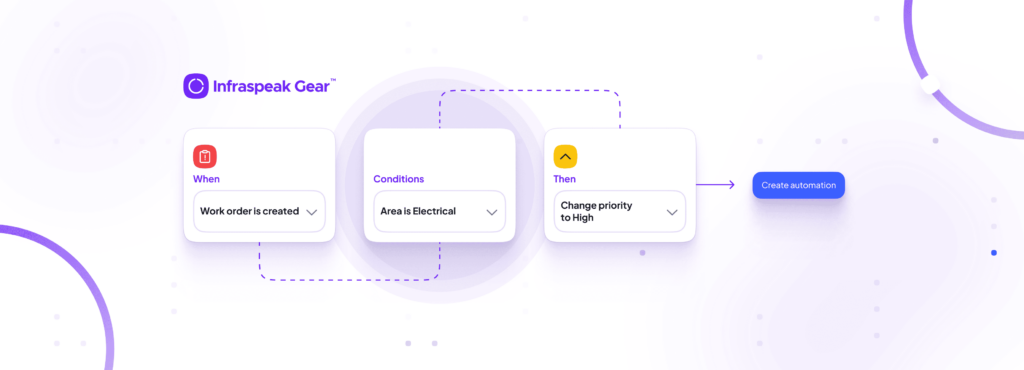
Play around with them enough, and you can create millions of automations. Do you see how powerful this is?
The best news is, it’s only just begun! We’re constantly bringing new triggers, conditions and outcomes into our Gear automations stack so that you can complete more manual admin tasks in record time, or even better, not at all!
Who’s ready for some examples?
Millions of automation combinations is obviously quite big, so the next thing we’ll do is choose three of the most popular examples and help you visualise what each one means in practice.
Example Number 1: Whenever a work order from the work order area ‘lighting’ is created, allocate it to the cost centre ‘Utilities’.
For instance, let’s say a light bulb goes out in one of your hotel suites, and your technician creates a work order to replace it. As you can imagine, this is a common occurrence and may happen once a week. Instead of manually assigning each work order to the cost centre, you can set up automation with Infraspeak Gear™ to take care of it for you.
Example Number 2: “When a work order is created related to the building ‘South Hospital Wing’ and the asset category is ‘Lift’, set the priority as ‘urgent’.
Imagine your hospital’s lift door broke in the South Wing. This would have a huge impact on any disabled or elderly patients! Cutting response time to this type of failure is critical to protect your patients, and therefore need to go to the top of your technician’s to–do list — set up this automation and that can be achieved.
Example Number 3: “When a work order is created for the client “His Majesty the King”, assign it to the person “007, James Bond”.
Only the best will do for his royal highness! If something goes wrong in one of his estates, it must always be passed to special agent Bond. James Bond. Ok, you got us, this one was just a fun example, but imagine you had a technician who had a lot of experience with a client and a strong rapport… you’d need the same automation, right?
We also wanted to share one more thing that may put a smile on your face:
—— You don’t need to make every automation from scratch! You can duplicate existing automations so that you can change just one element, and make it in even less time. For example, you could duplicate the automation in example 1 and create something like:
Whenever a work order with the work order area ‘plumbing’ is created, allocate it to the cost centre ‘Utilities’.
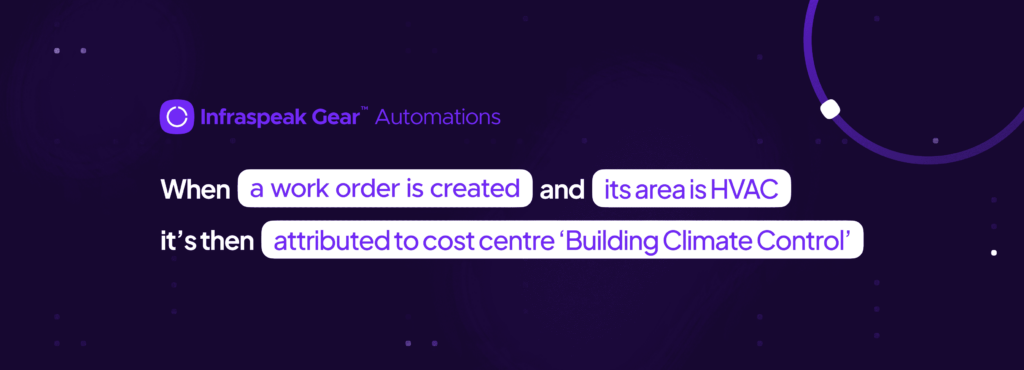
We care about you, facility and maintenance managers!
Ultimately, we’re doing all this because we care.
Over the past few years, you’ve had to rapidly adapt to fresh challenges like the need for flexibility in remote work and the pressing need to prioritise sustainability meant that whilst automation was important, it needed to be done in a way that helped you — it had to have direction. This is how we help.
The truth is, Infraspeak Gear™ automations is only one way we save you time and, ultimately, money. As well as our tried-and-tested core maintenance apps for corrective, preventive, procurement and more, we have a few more tricks up our sleeve that are designed to put you front and centre, and are worth highlighting:
The Infraspeak Network™
A brand new shared workspace that connects facility managers and service providers and which makes collaboration simple and pain-free, at long last.
The Infraspeak Hub™
A marketplace-style interface where you flexibly connect native apps, software integrations and hardware based on your needs, allowing you to scale your platform with your operations.
Infraspeak Gear™
The star of this article! Gear does more than just automations. It also:
- Data-backed suggestions and insights to speed up decision-making
- Warnings, for example, if an unusually high measurement is registered
- and enough automations for you to take millions of tasks off your to-do list!
- Improved efficiency in facility management.
- Better visibility into asset and team performance.
- More informed and data-driven decision making.
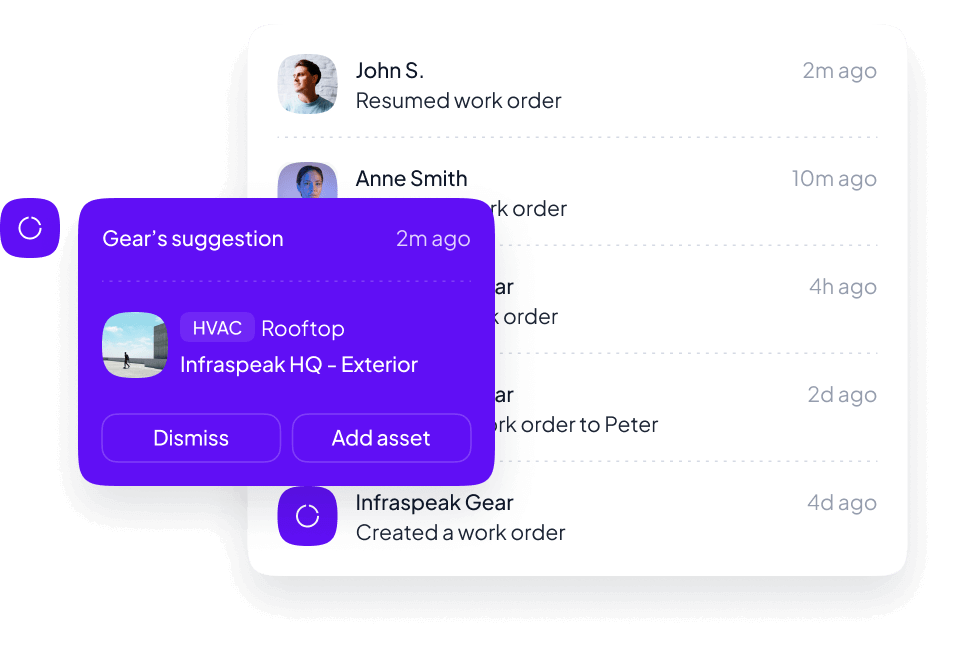