It’s not the million-dollar question, but it’s close: How can your company reduce maintenance costs?
Often, the maintenance costs of a company are so high that they can severely curb the profit margins and prevent the company from blossoming. Don’t let this happen to you! Read our 14 tips for reducing maintenance costs and start saving today.
So, is it impossible to reduce maintenance costs?
It’s not all or nothing. It is true that reducing maintenance spending in a short period of time is difficult. However, it is possible to improve control over your maintenance budget with a systematic approach. The key is to eliminate waste. This way, you eliminate tasks you are overdoing, increase productivity, and save materials.
According to one study, 50% of maintenance costs are “waste”. However, reducing maintenance spending by half requires almost superhuman efficiency. Instead, let’s try to cut maintenance costs by 20%. The prime suspects for cutting costs are:
- the equipment with the highest preventive maintenance costs;
- the equipment with the highest number of work hours per year.
14 strategies for reducing maintenance spending
The equipment you spend the most time on is probably the biggest source of waste. However, you can use these strategies to reduce maintenance costs on any asset:
Eliminate repetitive tasks
Did you know that 30% of preventive maintenance tasks are performed too often? Not all breakdowns follow a clear pattern over time. So, unless you have established a pattern (number of cycles, quarterly or semi-annual maintenance requirement, etc), you may be over-performing maintenance.
Eliminate tasks that do not correspond to any failure mode
Another way to avoid over-maintenance is to ensure that each task corresponds to a specific failure mode. In other words, ensure that you are not scheduling maintenance tasks that do not prevent anything specific. Not sure what the failure modes are? Here’s how to do a root cause analysis to better explore failure modes.
Instead of “fixing”, find a cure
Do you have equipment that breaks down frequently? Instead of constantly “fixing” the problem, conduct a root cause analysis to understand the true source of the problem. Often, investing a little more time will pay off in the long run. Here’s what you can learn from breakdowns.
Optimise work orders
Optimising work orders can help technicians to act faster and understand immediately what they need (protective materials, tools, etc). But there are more ways to avoid waste. For example, when you receive notifications of breakdowns, use geolocation to find out who the nearest technician is to optimise travel.
Avoid reactive maintenance
According to Reliable Plant, unplanned work takes 3 to 9 times longer. This means that reactive maintenance is not only haemorrhaging money and resources but also time. Therefore, one of the best ways to reduce maintenance costs is to avoid reactive maintenance.
💡 Learn how to reduce reactive maintenance and downtime with practical ideas
Negotiate contracts with current suppliers
This strategy has the potential to reduce your maintenance spending by up to 5%. Review all the contracts you have with suppliers and learn if there are any that you can renegotiate, any that are not being fulfilled, or any that can provide more than one service for a more competitive price.
Know the life cycle of your assets
If an asset requires numerous repairs, consider whether it’s worth continuing to repair it. Knowing the life cycle of your assets can go a long way in deciding whether it’s worth repairing the piece of equipment, completely refurbishing it, or exchanging it for a new one.
There is no one strategy to reduce maintenance costs. Maintenance is essential to ensure everyone’s safety and comfort! What you can do is eliminate wasteful maintenance and increase the productivity of your staff. For this, each task needs to have a specific goal and the staff needs to have an optimised work routine.
Prevent breakdowns
Unsurprisingly, the best way to reduce maintenance costs is to prevent malfunctions. Not only because fixing damaged equipment is costly, but also because your operations have to slow down or even come to a halt in order to accommodate the reparation works. But how can you prevent breakdowns? Without a doubt, you should invest in a good preventive maintenance strategy and ideally in a facilities management software capable of scheduling, tracking and reviewing all technical operations.
Track and manage inventory
If your average repair time is too high, one reason could be having a lack of spare parts in stock. One possible solution for this problem is to ensure a degree of similarity between assets and/or to have interchangeable spare parts. Having the same parts fit many machines can be a smart money-saving trick and makes it easier to obtain technical assistance from the manufacturer. Finally, you should bear in mind that ordering parts in bulk allows you can negotiate better prices.
Cut down on day-to-day wastage
Just like any other activity, maintenance is full of waste. On average, only 30% of technicians’ time is spent working. The rest? Waiting for tools, for authorisations, going back and forth… Anyway, the list goes on. Use the data collected by your IMMP to understand where the bottlenecks and productivity losses are.
Optimise MRO inventory
Another strategy to lower maintenance expenditure is to optimise inventory for maintenance, repairs, and operations. Again, use data history to forecast your needs. This ensures you don’t spend money on parts and tools you won’t need or that are still in stock. This also allows you to save space and improve logistics.
Train your team
Another key to keeping maintenance costs down is training your entire team and not just the technicians. If all of your employees know how to detect problems, malfunctions will be detected much faster. Sure enough, you will have fewer periods of downtime and you will avoid expensive and time-consuming repairs.
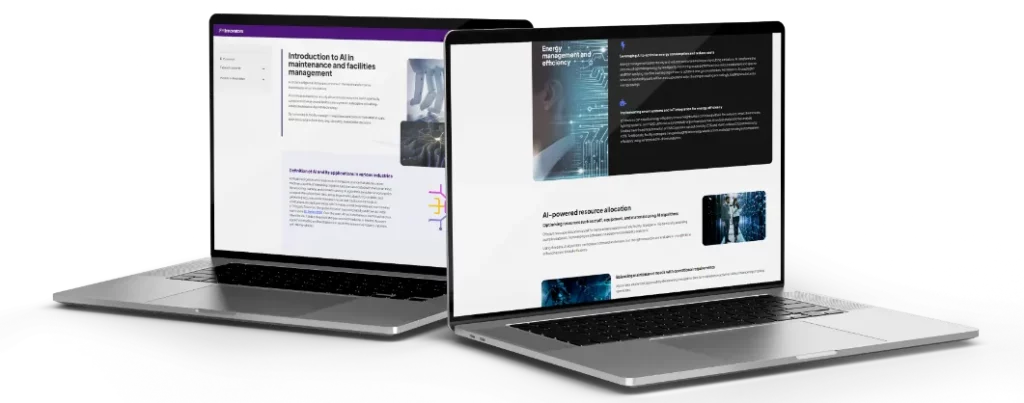
Choose the right technology
Even if your phone freezes from time to time and your computer may require a quick fix via the failsafe “On-Off” method, technology is an asset to your business and should be used. Imagine (or worse, try) analysing all your maintenance operations one by one with a pen and pad of paper? Using a solution that you can customise to suit your needs will streamline your infrastructure management, and save you a lot of time.
Extend the warranty/insurance period
Nothing functions flawlessly. It is always a good idea to insure the most expensive equipment for your business or to extend the warranty of some items. This will not only mean saving on maintenance costs but also on high repair costs. In some cases, you may even want to insure some specific components — talk to your technicians to decide which policy is the most appropriate for your business.
Extra tip: finding the ideal maintenance partner with Infraspeak Network™
Infraspeak Network™ is a shared workspace that introduces collaboration to procurement and work-execution processes between facility and maintenance managers and vendors, suppliers, contractors and facility service providers.
The Infraspeak Network™ simplifies everyday processes like quote requests and proposals, sharing work orders and monitoring maintenance carried out by suppliers. These newly enabled workflows allow you to do the following from your Infraspeak platform:
Expand your Client/Supplier base and book of contacts
Manage quote requests and agree on proposals for work orders and purchase of stock
Execute contracted maintenance work more efficiently