You’ve probably read that predictive maintenance yields savings of 30-40% (compared to reactive maintenance), or savings of 8-12% (compared to preventive maintenance). What you probably don’t know is that those maintenance statistics are from the U.S. Department of Energy’s Best Practices guide from… 2010.
So much has changed in the past decade and it’s time we collectively update our references. The following maintenance statistics give you a real perspective of what’s happening right now. This is a good place to start if you’re looking for maintenance benchmarks to evaluate your own performance.
Maintenance is key to keeping businesses competitive and increasing return on investment. At the same time, companies need to control costs to remain competitive. So, how can maintenance managers provide cost-effective maintenance? Our team looked at the biggest and latest challenges in maintenance – including the one just mentioned – and the trends that take them head-on. Let’s dive in!
Top 7 maintenance trends not to miss
Predictive maintenance powered by AI
Predictive maintenance is evolving, thanks to AI and machine learning. With advanced data analytics and IoT integration, organisations can now anticipate equipment failures with greater accuracy. In 2025, expect widespread adoption of digital twins, where virtual replicas of physical assets predict performance and maintenance needs in real time.
Sustainability-driven maintenance
Sustainability goals are reshaping maintenance practices. Companies are increasingly adopting green technologies, such as energy-efficient systems and sustainable spare parts. Lifecycle assessments and carbon footprint tracking for maintenance operations will become standard practices, reflecting a broader commitment to environmental responsibility.
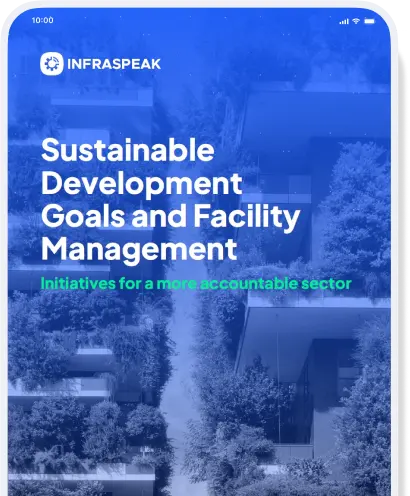
Collaborative maintenance through smart platforms
Maintenance is becoming a team effort, enabled by platforms such as Infraspeak. These facilitate collaboration across departments and stakeholders, providing real-time visibility into asset health, work orders, and compliance data. The focus on seamless communication will drive faster problem resolution and smarter decision-making.
Augmented and virtual reality (AR/VR) for maintenance training and execution
AR and VR are revolutionising the way maintenance professionals are trained and execute tasks. Technicians can use AR glasses to access manuals, visual instructions, or expert support on-site. Virtual reality simulations offer immersive training experiences, improving skills without interrupting operations. In 2025, AR/VR tools will become essential for complex maintenance tasks and remote support.
Resilient maintenance strategies with edge computing
Edge computing is redefining the way data is processed and utilised in maintenance. By analysing data at the source, companies can ensure faster decision-making, even in low-connectivity environments. This capability will be critical in 2025 for industries relying on real-time insights, such as manufacturing, utilities, and transport.
📝 Read also: The role of Predictive Maintenance in enhancing manufacturing plant safety
Decentralised Repair Teams
Companies with several facilities often spread throughout different territories and countries, traditionally keep maintenance teams onsite at a great cost. Realistically, this is the only option that allows companies to react quickly to a sudden breakdown. But, if we take sensors and AR for granted in the near future, do onsite teams still make sense?
Decentralised repair teams are already feasible. Open networks of repair logs and real-time machine data (and extremely reliable, if it’s collected by sensors) allow managers to know what’s happening at any time. Meanwhile, AR can be applied to realistic training materials and virtual repair oversight. That means companies can either have smaller in-house teams or allocate them to a facility only when it’s strictly needed.
Ultimately, decentralised repair teams allow companies to optimise their workforce. They also reduce costs – on travel, training, etc – and cost variations. On the other hand, given the level of outsourcing in Maintenance and FM, it will impact many third-party companies. These companies will likely need to adjust their business model and differentiate themselves by the level of support and analysis they provide.
More Agility and Less Downtime
If you call us out for saying less downtime is a trend for the following years, we don’t blame you. In truth, less downtime is never out of fashion. But, since there’s increased competition, businesses need to become more agile. Arguably, adaptability is the greatest competitive advantage that companies can have. That means maintenance teams need flexible platforms where they can add or remove features with no hassle.
However, that’s not enough to reduce idle time and improve productivity. Companies are looking to become more agile across the board, eliminate waste, and implement lean practices. Lean maintenance includes “just-in-time” inventory management and procurement, kaizen, reliability-centred maintenance, and condition monitoring (which, in a way, is also “just-in-time” maintenance).
Reduced downtime not only improves uptime, it also increases the equipment’s useful life. Both have a positive impact on equipment ROI, thus growing profit margins. It plays into sustainability as well, since we must use resources for as long as possible and quit “Europe’s throwaway culture”.
On average, maintenance accounts for 20-50% of the total operating budget. Effective maintenance is critical to ensure competitiveness and productivity. It’s a tall order for maintenance managers, sure, but it’s not impossible to provide top-notch services with greater agility and economy. As long as you have the right technology, of course!
Since you’re here…
📝 Don’t forget to check the Industrial maintenance trends until 2030!
📝 You may also be interested in the facilities management trends and challenges for this year.
Maintenance is Changing: but are we changing with it?
For European companies, the main pain points are unplanned downtime and emergency maintenance (90%), ageing IT infrastructure and technology (88%), connecting modern assets and analysing data (76%), obtaining asset data (40%), connecting older legacy assets and obtaining data (29%), maintenance cycles (24%), connecting assets from remote locations (24%), monitoring assets in real-time (22%), and collaboration with vendors (20%).
Source: CXP Group Report, 2018
Maintenance Budget and Efficiency
- In 2021, 42.5% of companies in the US spent 21-40% of their operating budget on cleaning and maintenance equipment/supplies. About 35.79% spent only 1-20%, 16.78% spent 41-60%, 3.36% spent 61-80%, and 1.57% spent more than 80% [Statista]
- 29% of plants spend 5 to 10% of their annual budget on maintenance; 24% spend 11 to 15%; 17% spend more than 15%, another 17% spend less than 5%, and 13% don’t know [Plant Engineering, 2021]
- Around 88% of facilities outsource some of their maintenance operations. On average, 23% of their maintenance tasks are outsourced [Plant Engineering, 2021]
- 44% of plants spend more than 40 hours a week performing maintenance [Plant Engineering, 2021]
- 68% of manufacturers considered their safety program “good, but needs improvement”, while only 19% classified it as “excellent, best in class”. [Advanced Technology, 2020]
- 93% of companies consider their maintenance processes are not very efficient [CXP Group, 2018]
⚙️ Does your company fit into those overwhelming 93%? Here are 50 actionable ways to improve your efficiency.
Maintenance Metrics
|
Maintenance Strategies
- 88% of manufacturing companies use preventive maintenance, 52% use run to failure, 40% apply preventive maintenance using analytics tools, and 22% reliability-centred maintenance (RCM) using operational data analysis [Plant Engineering, 2021]
- In industrial maintenance, 80% of companies link a CMMS to greater productivity. Most think predictive maintenance is the best strategy to reduce downtime and reduce the probability of failure, but RCM is what provides the best overall equipment effectiveness. [Advanced Technology, 2020]
Still running to failure: statistics about unplanned downtime
Source: Plant Engineering
- The top causes for unplanned equipment downtime are ageing equipment (34%), mechanical failure (20%), operational error (11%), lack of time for maintenance (9%), poor equipment design (8%) [Plant Engineering, 2020]
- According to Machine Metrics, outages last 4 hours on average
- The Aberdeen Group calculates that unplanned equipment downtime costs, on average, $260.000 an hour (€220.400)
- To decrease downtime, 46% of companies plan to introduce or change their maintenance strategy, 46% intend to upgrade their equipment, 33% want to improve training and increase frequency, 32% would like to expand monitoring capabilities, and 16% to implement automated analytics/ machine downtime. Plus, 13% to increase scheduled downtime, 9% want to hire additional maintenance technicians, and another 9% to outsource maintenance services. [Advanced Technology, 2020]
Source: Industrial Maintenance 2020 | Status, Trends + Forecasts Report, Advanced Technology, 2020
⚙️ If run to failure is your Achilles’ heel, here are 8 actionable ways to reduce reactive maintenance in your facility.
Preventive Maintenance: good on paper, harder in real life
- 94% of companies consider Maintenance, Repairs and Operations (MRO) extremely or somewhat important to avoid downtime, follow lean practices, and manage preventive maintenance. [Peerless Research Group (PRG), 2018]
- 37% of companies handle all their MRO manually, but 27% have already automated 25-50% of their tasks, 21% have automated 50-75%, 9% are mostly automated, and 6% are fully automated. [Peerless Research Group (PRG), 2018]
- In industrial maintenance, 60% of companies associate preventive maintenance with better productivity, and over 60% with decreased downtime and improved safety. [Advanced Technology, 2020]
According to an ARC Advisory Group’s Enterprise Asset Management and Field Service Management Market Study:
- As much as 50% of maintenance costs are a “waste”
- Around 30% of preventive maintenance is too frequent
- As little as 18% of age-related failures follow a pattern
Maintenance Software Statistics
- 52% of industrial plants use a Computerised Maintenance Management System (CMMS) [Plant Engineering, 2021]
- 44% of businesses in Portugal use specific software (CMMS) for maintenance management, 55% use facility management software, and the remainder uses Excel sheets [Portuguese Facility Management Association, 2021].
- 60 – 80% of CMMS implementations fail. Why? Poor user engagement and training, lack of support from management, and unclear goals, roles, and responsibilities [Fiix Implementation Guide, 2019]
Predictive Maintenance and Data: are they delivering?
- 48% of plants already use connected devices to capture, analyse, and improve maintenance. A further 30% is looking into it. [Plant Engineering, 2021]
- In Spain, 60% of businesses had already invested, or planned investments, in predictive maintenance in 2018. In Germany, 54% had already invested in predictive maintenance and 80% planned to invest. [CXP Group, 2018]
- 89% of companies are worried about data security and privacy. The lack of ability to process that and inappropriate infrastructure are the other inhibitors to implement predictive maintenance. [CXP Group, 2018]
- Specifically, in the UK, 85% of businesses see planning maintenance processes based on predictive insights as a major challenge. [CXP Group, 2018]
- The global predictive maintenance market will grow to $23.5 billion by 2024. [IoT Analytics, 2019]
- 91% of businesses reduce in repair time and unplanned downtime, after implementing predictive maintenance [CXP Group, 2018]
- 93% improve the maintenance of their ageing infrastructure [CXP Group, 2018]
According to PWC’s “Predictive Maintenance 4.0 – Beyond the Hype: PdM delivers results”, a study with 268 real European companies from Belgium, Germany, and the Netherlands:
- Predictive maintenance decreases costs by 12%
- Availability improves by 9%
- Extends the lifetime of an ageing asset by 20%
- Reduces safety, health, environmental and quality risks by 14%
The Future of Maintenance: what managers think comes next
But is it so easy to invest in predictive maintenance and connectivity? Apart from ageing equipment, what are the obstacles managers face?
- Managers believe the main challenge they face in the future is ageing equipment (67%). Other challenges include lack of understanding of new options/ technologies (37%), lack of resources or staff (34%), lack of budget (29%), lack of training (28%), lack of support from management (26%), employee buy-in (23%), poor scheduling, rarely followed through (20%), other (2%), and non-applicable (1%). [Plant Engineering, 2021]
Automation, IoT, and the skills gap
- The International Data Corporation (IDC) projects $ 4.1 billion will be invested in augmented and virtual reality for industrial maintenance by 2024.
- But there’s a skill gap. Only 29% of facility managers believe their technicians are “very prepared”, 45% say they’re “somewhat prepared”, and 26% “not at all prepared” [Peerless Research Group (PRG), 2018]
- The lack of skilled personnel is real. 31% of companies outsource operations because “skilled individuals are hard to find.” 58% of manufacturing employees have worked in the industry for more than 20 years. [Plant Engineering, 2021]
- In industrial maintenance, the situation worsens. The three main reasons to outsource maintenance are lack of time or manpower (48%), lack of skills among current staff (41%), and too many specialised skills (39%). [Advanced Technology, 2020]
- 48% of manufacturing companies find the process of hiring, onboarding, and retaining the biggest challenge to their current program. Moreover, 41% viewed the lack of resources or staff as the biggest challenge to improve maintenance [Advanced Technology, 2020]