Definition of Run-to-Failure Maintenance
Run-to-failure maintenance, also known as “breakdown maintenance”, is a maintenance strategy where an asset or piece of equipment is allowed to operate until it fails or breaks down before any maintenance or repairs are performed. In this approach, maintenance actions are only taken when the equipment has stopped working or is no longer operational.
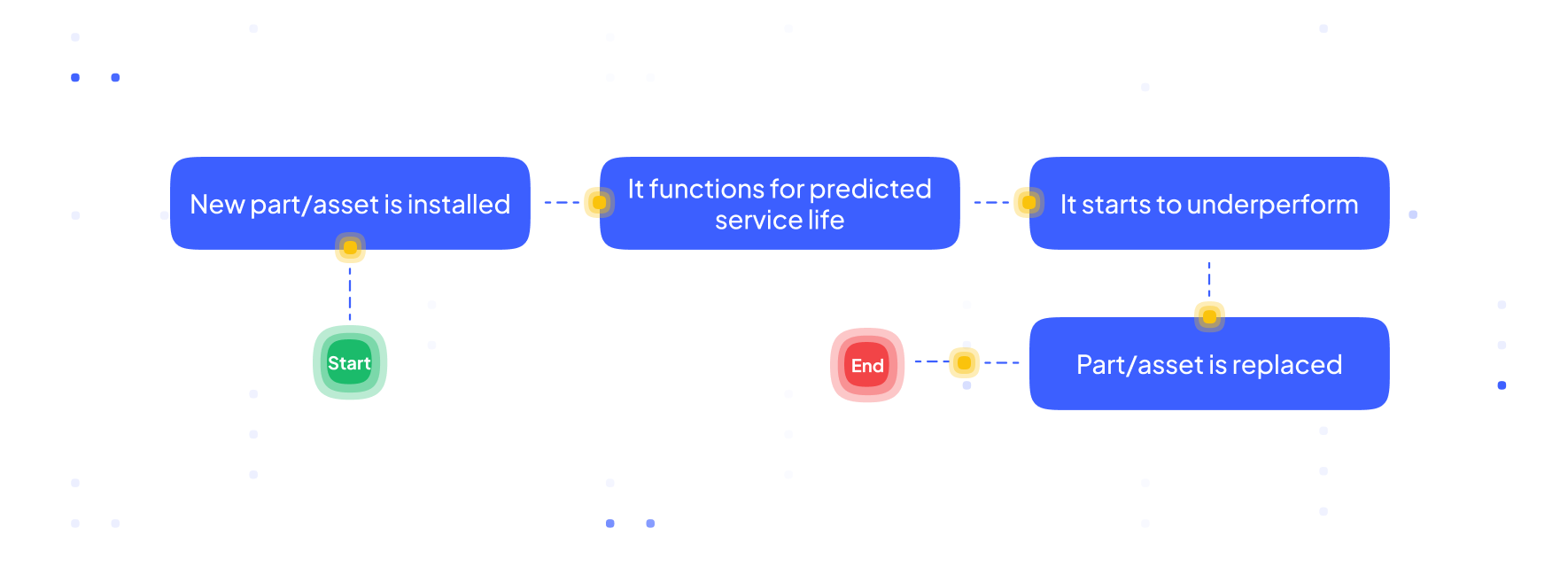
Benefits of Run-to-Failure Maintenance
Despite its unconventional nature, run-to-failure maintenance (RTF) offers several advantages that make it a compelling strategy in certain circumstances. One key benefit is its cost-effectiveness. By avoiding preemptive maintenance, organisations can save on unnecessary repairs and reduce downtime, leading to time savings. Additionally, this approach is particularly applicable to non-critical assets, where minor failures may not significantly impact operations or safety, making it a practical choice of easy implementation.
When to apply Run-to-Failure Maintenance
To grasp the rationale behind implementing run-to-failure maintenance, it is essential to explore specific use cases where this approach excels. We will examine why non-critical assets are ideal candidates for this strategy and how certain equipment’s inherent reliability supports the decision to run it until failure.
Evaluating risk factors and understanding the consequences of potential failures are essential considerations. Striking a balance between run-to-failure maintenance and other maintenance approaches can optimise equipment performance whilst controlling costs.
Here are some examples of when RTF might be applied:
- Light Bulbs: In residential or small-scale applications, run-to-failure maintenance is often applied to light bulbs. Since the cost of replacement is relatively low and the failure of a single light bulb is not critical, it may not be cost-effective to perform preventive maintenance on each individual bulb.
- Assets with a Short Life Span: Assets that have a short life span can be easily replaced once they reach the end of their life cycle. These assets include items like batteries, water heaters, and digital controls.
- Non-Critical Appliances: Equipment that just isn’t crucial to production can be replaced without impacting a facility’s output.
- Recreational Equipment: Recreational facilities, like amusement park rides or coin-operated machines, may use run-to-failure maintenance for certain low-cost equipment. The cost of downtime or replacement is relatively low compared to the cost of performing regular maintenance.
- Low-Value Components: In complex systems, there may be some low-value components that do not significantly impact the overall operation. In such cases, it might be more practical to allow these components to run until they fail before replacing them.
- Temporary or Short-Term Installations: For temporary installations or projects with a short lifespan, such as events, it may not be necessary to perform preventive maintenance, and run-to-failure maintenance can be a reasonable approach.
✖ Please note: RTF is not suitable for critical systems or equipment where failure could lead to significant safety hazards, financial losses, or harm to the environment. For such cases, preventive maintenance strategies are more appropriate to ensure reliability and avoid failures.
How to Apply a Run-to-Failure Maintenance Programme
Implementing a RTF maintenance programme requires establishing monitoring and alert systems, setting appropriate thresholds for triggering maintenance actions, and training maintenance personnel for efficient execution. Building a cohesive team that understands the objectives of run-to-failure maintenance is paramount to achieving positive outcomes.
By aligning run-to-failure actions with preventive and predictive maintenance tasks, organisations can strike a harmonious balance between different maintenance strategies.
Also, in today’s digital age, Intelligent Maintenance Management Platforms (IMMP) have emerged as invaluable tools for planning and executing maintenance approaches, RTF included. Leveraging advanced data analytics, these platforms enable informed decision-making, ensuring optimal equipment performance and reliability.
Using an IMMP, maintenance teams can proactively create work order templates and allocate tasks whenever maintenance requirements arise.