Seguro que ya has leído en algún lugar que el mantenimiento predictivo permite un ahorro del 30-40 % (en comparación con el mantenimiento correctivo) o un ahorro del 8-12 % (en comparación con el mantenimiento preventivo). Lo que probablemente no sabes es que estas estadísticas de mantenimiento son de la Guía de Buenas Prácticas del Departamento de Energía de los Estados Unidos de… 2010.
Las cosas han cambiado mucho en la última década y ha llegado el momento de actualizar nuestras referencias. Las siguientes estadísticas de mantenimiento te darán una perspectiva de lo que está pasando en este momento. Este es un buen punto de partida si estás buscando benchmarks de mantenimiento para evaluar tu propio rendimiento.
Mantenimiento predictivo impulsado por IA
El mantenimiento predictivo está evolucionando gracias a la inteligencia artificial (IA) y al aprendizaje automático. Con análisis avanzados de datos y la integración del IoT, las organizaciones ahora pueden anticipar fallos en los equipos con mayor precisión. En 2025, se espera una adopción generalizada de los gemelos digitales, réplicas virtuales de activos físicos que predicen el rendimiento y las necesidades de mantenimiento en tiempo real.
Mantenimiento impulsado por la sostenibilidad
Los objetivos de sostenibilidad están transformando las prácticas de mantenimiento. Las empresas están adoptando cada vez más tecnologías verdes, como sistemas de alta eficiencia energética y repuestos sostenibles. Las evaluaciones del ciclo de vida y el seguimiento de la huella de carbono en las operaciones de mantenimiento se convertirán en prácticas estándar, reflejando un compromiso más amplio con la responsabilidad ambiental.
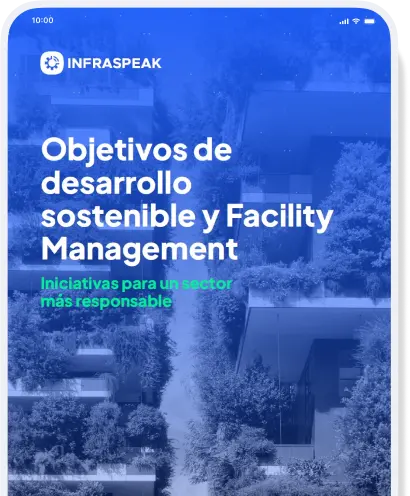
Mantenimiento colaborativo mediante plataformas inteligentes
El mantenimiento se está convirtiendo en un esfuerzo colaborativo, facilitado por plataformas como Infraspeak. Estas plataformas permiten la colaboración entre departamentos y partes interesadas, proporcionando visibilidad en tiempo real sobre el estado de los activos, las órdenes de trabajo y los datos de cumplimiento. El enfoque en la comunicación fluida impulsará una resolución más rápida de problemas y una toma de decisiones más inteligente.
Realidad aumentada y virtual (AR/VR) para formación y ejecución en mantenimiento
La AR y la VR están revolucionando la forma en que los profesionales de mantenimiento se capacitan y ejecutan tareas. Los técnicos pueden usar gafas de realidad aumentada para acceder a manuales, instrucciones visuales o soporte experto en el sitio. Las simulaciones en realidad virtual ofrecen experiencias de formación inmersivas, mejorando las habilidades sin interrumpir las operaciones. En 2025, las herramientas de AR/VR serán esenciales para tareas complejas de mantenimiento y soporte remoto.
Estrategias de mantenimiento resiliente con computación en el borde
La computación en el borde está redefiniendo la forma en que se procesan y utilizan los datos en el mantenimiento. Al analizar los datos en el origen, las empresas pueden tomar decisiones más rápidas, incluso en entornos con baja conectividad. Esta capacidad será crítica en 2025 para industrias que dependen de información en tiempo real, como la manufactura, los servicios públicos y el transporte.
Más agilidad y menos downtime
Si nos llamas la atención por decir que menos downtime es una tendencia, no te culpamos. En realidad, buscar un menor downtime nunca pasa de moda. Pero, dado que la competencia es cada vez mayor, las empresas deben ser más ágiles. Podría decirse que la adaptabilidad s la mayor ventaja competitiva que pueden tener las empresas. Eso significa que los equipos de mantenimiento necesitan plataformas flexibles en las que puedan añadir o eliminar funciones sin problemas.
Sin embargo, eso no es suficiente para reducir el downtime y mejorar la productividad. Las empresas buscan ser más ágiles en todos los ámbitos, eliminar el despilfarro e implantar prácticas lean. El mantenimiento lean incluye la gestión de inventarios y adquisiciones “justo a tiempo”, el kaizen, el mantenimiento centrado en la fiabilidad y la monitorización de la condición (que, en cierto modo, también es un mantenimiento “justo a tiempo”).
Por cierto, aquí tenemos 9 técnicas de monitorización de la condición que debes conocer.
La reducción del downtime no solo mejora el tiempo de actividad, sino que también aumenta la vida útil del equipo. Ambas cosas tienen un impacto positivo en el retorno de la inversión de los equipos, con lo que aumentan los márgenes de beneficio. También influye en la sostenibilidad, ya que debemos utilizar los recursos durante el mayor tiempo posible y abandonar la “cultura europea del descarte”.
En media, el mantenimiento supone entre el 20 y el 50% del presupuesto operativo total. Un mantenimiento eficaz es fundamental para garantizar la competitividad y la productividad. Es una tarea ardua para los responsables de mantenimiento, sin duda, pero no es imposible prestar servicios de primera calidad con más agilidad y economía. Siempre que se cuente con la tecnología adecuada, ¡por supuesto!
Y ya que estás aquí…
- ¡No te olvides de consultar las tendencias del mantenimiento industrial hasta 2030!
- También puede interesarte las tendencias y retos del facility management para este año.
El mantenimiento está cambiando pero ¿estamos cambiando al mismo ritmo?
Para las empresas europeas, los principales puntos críticos son el downtime no planeado y el mantenimiento de emergencia (90 %), el envejecimiento de la infraestructura y tecnología de IT (88 %), la conexión de activos modernos y el análisis de datos (76 %), la obtención de datos de activos (40 %), la conexión de activos antiguos y la obtención de datos (29 %), los ciclos de mantenimiento (24 %), la conexión de activos a lugares remotos (24 %), el monitoreo de activos en tiempo real (22 %) y la colaboración con proveedores (20 %).
Fuente: CXP Group Report, 2018
Presupuesto y eficacia del mantenimiento
- En 2021, el 42,5 % de las empresas en los Estados Unidos gastaron el 21-40 % de su presupuesto operacional en equipos/materiales de limpieza y mantenimiento. Cerca del 35,79 % gastaron solo el 1-20 %, el 16,78 % gastaron el 41-60 %, el 3,36 % gastaron el 61-80 % y el 1,57 % gastaron más del 80 % [Statista].
- El 29 % de las fábricas gastaron del 5 al 10 % de su presupuesto anual en mantenimiento; el 24 % gastaron del 11 al 15 %; el 17 % gastaron más del 15 %; el 17 % gastaron menos del 5 %, y el 13 % no saben lo que gastaron [Plant Engineering, 2021].
- Cerca del 88 % de las instalaciones subcontratan algunas de las operaciones de mantenimiento. De media, el 23 % de las tareas de mantenimiento son subcontratadas [Plant Engineering, 2021].
- El 44 % de las fábricas gastan más de 40 horas por semana haciendo mantenimiento [Plant Engineering, 2021].
- El 68 % de la industria considera su programa de seguridad «bueno, pero necesita ser mejorado», mientras que solo el 19 % lo clasifica como «excelente, de máximo nivel». [Advanced Technology, 2020]
- El 93 % de las empresas consideran que sus procesos de mantenimiento son muy eficaces [CXP Group, 2018].
¿Tu empresa se encuentra entre estes 93 %? Aquí puedes encontrar 50 acciones para mejorar la eficacia.
Métricas de mantenimiento
|
Estrategias de Mantenimiento
- El 88 % de las empresas industriales utilizan el mantenimiento preventivo, el 52 % utilizan el «usar hasta averiar», el 40 % realizan mantenimiento preventivo utilizando herramientas analíticas y el 22 % mantenimiento centrado en la confiabilidad (RCM) utilizando el análisis de datos operacionales [Plant Engineering, 2021].
- En el mantenimiento industrial, el 80 % de las empresas asocian el CMMS a una mayor productividad. La mayoría piensa que el mantenimiento predictivo es la mejor estrategia para reducir el downtime y reducir la probabilidad de falla, pero el RCM es lo que proporciona una mejor eficacia global a los equipos [Advanced Technology, 2020].
- Las principales causas de downtime no planeado de equipos son: envejecimiento de los equipos (34 %), fallo mecánico (20 %), error operacional (11 %), falta de tiempo para mantenimiento (9 %) y mal diseño del equipo (8 %) [Plant Engineering, 2020].
- Según Machine Metrics, las interrupciones duran de media 4 horas.
- El Grupo Aberdeen estima que el downtime no planeado de equipos cuesta, de media, 220 400 € por hora (260 000 USD)
- Para disminuir el downtime, el 46 % de las empresas pretenden introducir o alterar la estrategia de mantenimiento, el 46 % actualizar equipos, el 33 % mejorar y aumentar la frecuencia de capacitaciones, al 32 % les gustaría expandir sus capacidades de monitoreo y el 16 % pretende automatizar el análisis/downtime de máquinas. Además, el 13 % pretende aumentar el downtime programado, el 9 % contratar más técnicos de mantenimiento y el 9 % subcontratar servicios de mantenimiento [Advanced Technology, 2020].
Fuente: Industrial Maintenance 2020 | Status, Trends + Forecasts Report, Advanced Technology, 2020
Si «usar hasta averiar» es tu talón de Aquiles, aquí puedes encontrar 8 medidas para reducir el mantenimiento correctivo en tus instalaciones.
Mantenimiento Preventivo: bueno en teoría pero difícil en la práctica
- El 94 % de las empresas consideran el Mantenimiento, Reparación y Operaciones (MRO) extremamente, o de cierta forma, importante para evitar el downtime, por lo que es importante leer y seguir prácticas para gestionar el mantenimiento preventivo [Peerless Research Group (PRG), 2018].
- El 37 % de las empresas tratan todos los MRO manualmente, pero el 27 % ya automatizaron el 25-50 % de las tareas, el 21 % automatizaron el 50-75 %, el 9 % están mayoritariamente automatizadas, y el 6 % están totalmente automatizadas [Peerless Research Group (PRG), 2018].
- En el mantenimiento industrial, el 60 % de las empresas asocian el mantenimiento preventivo a una mejor productividad, y más del 60 % a una disminución del downtime y mayor seguridad [Advanced Technology, 2020].
De acuerdo con un Estudio de Mercado de Gestión de Activos Empresariales y Gestión de Servicios en el Terreno de ARC Advisory Group:
- Hasta el 50 % de los costes de mantenimiento son un «desperdicio».
- Cerca del 30 % del mantenimiento preventivo se realiza con demasiada frecuencia.
- Solo el 18 % de las averías relacionadas con la edad de los equipos siguen un modelo.
Estadísticas de Software de Mantenimiento
- El 52 % de las instalaciones industriales utilizan un Sistema de Gestión de Mantenimiento Computarizado (CMMS) [Plant Engineering, 2021].
- El 60-80 % de las implementaciones de CMMS fallan. ¿Por qué? Las causas más populares son la débil relación y formación de los usuarios, la falta de apoyo de la administración y el establecimiento de funciones y responsabilidades poco claras [Fiix Implementation Guide, 2019].
Mantenimiento predictivo y datos: ¿cumplen las expectativas?
- El 48 % de las fábricas ya utilizan dispositivos conectados para capturar, analizar y mejorar el mantenimiento. Otro 30 % están estudiando el tema [Plant Engineering, 2021].
- En España, el 60 % de las empresas ya han invertido, o planeado invertir, en mantenimiento predictivo en 2018. En Alemania, el 54 % ya han invertido en mantenimiento predictivo y el 80 % han planeado hacerlo [CXP Group, 2018].
- El 89 % de las empresas están preocupadas con la seguridad y privacidad de los datos. La falta de capacidad para procesarlos y las infraestructuras inadecuadas son otros obstáculos para implementar el mantenimiento predictivo [CXP Group, 2018].
- El mercado global de mantenimiento predictivo crecerá hasta 23,5 mil millones de dólares hasta 2024 [IoT Analytics, 2019].
- El 91 % de las empresas reducen el tiempo de reparación y el downtime no planeado tras la implementación del mantenimiento predictivo [CXP Group, 2018].
- El 93 % mejoran el mantenimiento de las infraestructuras envejecidas [CXP Group, 2018].
De acuerdo con «PWC’s Predictive Maintenance 4.0 – Beyond the Hype: PdM delivers results», un estudio con 268 empresas europeas reales de Bélgica, Alemania y Países Bajos:
- El mantenimiento predictivo disminuye los costes en un 12 %
- La disponibilidad mejora en un 9 %
- Prolonga en un 20 % la vida útil de los activos envejecidos
- Reduce los riesgos de seguridad, salud, ambiente y calidad en un 14 %.
Obtén más información sobre las técnicas de mantenimiento basado en la condición y los beneficios que debes esperar de cada una de ellas.
El futuro del mantenimiento: lo que piensan los gestores sobre lo que va a venir
Pero, ¿es tan fácil invertir en mantenimiento predictivo y en conexión? Además del envejecimiento de los equipos, ¿cuáles son los obstáculos que los gestores enfrentan?
- Los gestores creen que el principal desafío que enfrentarán en el futuro es el envejecimiento de los equipos (67 %). Otros desafíos incluyen: la falta de comprensión de nuevas opciones/tecnologías (37 %), falta de recursos o personal (34 %), falta de presupuesto (29 %), falta de formación (28 %), falta de apoyo de la administración (26 %), falta de adhesión de los empleados (23 %), mala planificación, no se siguen las indicaciones (20 %), otras (2 %) y no aplicable (1 % [Plant Engineering, 2021].
Automatización, IOT y el déficit de competencias
- International Data Corporation (IDC) proyecta invertir 4,1 mil millones de dólares en realidad virtual para mantenimiento industrial hasta 2024.
- Solo el 29 % de los facility managers creen que sus técnicos están «muy preparados», el 45 % dicen que están «un poco preparados» y el 26 % «nada preparados» [Peerless Research Group (PRG), 2018].
- La falta de personal cualificado es una realidad. El 31 % de las empresas subcontratan porque «las personas cualificadas son difíciles de encontrar». El 58 % de los trabajadores de la industria trabajan en el sector hace más de 20 años [Plant Engineering, 2021].
- En el mantenimiento industrial, la situación se agrava: Las tres principales razones para subcontratar el mantenimiento son: la falta de tiempo o de mano de obra (48 %), la falta de capacitación de los trabajadores existentes (41 %) y el exceso de formación especializada (39 %) [Advanced Technology, 2020].
- El 48 % de las empresas industriales encuentran en el proceso de contratación, integración y retención el mayor desafío para su programa actual. Además, el 41 % considera la falta de recursos o personal como el mayor desafío para mejorar el mantenimiento [Advanced Technology, 2020].