What is a CMMS?
Starting point: CMMS means Computerised Maintenance Management System/Software.
The key to understanding what a CMMS is lies in these words. A CMMS is a type of software to systematise and centralise all the information about maintenance management. And since the goal is precisely to concentrate efforts and optimise time, we start by shortening the name to the acronym “CMMS”.
These systems are often referred to by other names, such as:
- Maintenance management software;
- Preventive maintenance software;
- Facilities management software;
- Work order management software;
- …among others.
Does your business need a CMMS?
Before we explore the advantages of a CMMS and how it works, the question is whether your company really needs a CMMS. Although each case is different, you most likely need maintenance management software if you meet at least one of these criteria:
✓ you operate with a variety of industrial equipment
✓ your equipment often has expensive breakdowns
✓ you need to manage infrastructures and large facilities (e.g. hotels, shopping centres, sports arenas, electric power stations)
✓ you have an obligation to comply with several hygiene, safety and quality criteria, including HACCP analyses and ISO standards
✓ you’re a maintenance service provider, and you need to manage several assets and clients
✓ you’re still dependent on manual processes (or systems such as Excel) to create checklists and taks plans
✓ your decision-making is based on intuition rather than real data
✓ you have a disorganised and inefficient maintenance team
✓ you have trouble communicating with the maintenance staff
Do any (or several!) of the items above apply to you? Let’s see how this kind of software works and even how you can save money with a CMMS, even if you run a relatively small business.
How does a CMMS work?
The basic concept to understand how a CMMS software works is the work order, or maintenance request. Everything revolves around work orders, which can be, by a certain technician, followed in real-time, processed, marked as resolved, archived, and used in the production of detailed reports on its operation.
For example, if your preventive maintenance plan includes several tasks in HVAC equipment, you only need to create a maintenance request to, say, “change a filter”, schedule it for a certain date and time, and assign it to a technician. When the technician has finished the task, he marks it as “closed” and has one less worry crossed out of his (and your) list.
This is the main purpose of any maintenance management software and this type of process applies to both reactive maintenance (or corrective maintenance) tasks and preventive maintenance plans. The remaining functions, which vary between different CMMS, aim to speed up the management of maintenance requests, besides simplifying communication, and increasing control over the whole maintenance operation.
Here are a few examples:
- asset management, so you can access all the information about each piece of equipment at any time;
- scheduling tasks and preventive maintenance features, so you can schedule routine inspections;
- failure reporting and reactive maintenance features to solve any unexpected equipment failures;
- stock management, to control inventory and avoid stock disruption;
- creation of maintenance requests from any employee or customer, which makes failure detection faster;
- conducting audits on your equipment and infrastructures;
- monitoring energy consumption, such as water, gas, and light from your buildings;
- mobile CMMS app for maintenance technicians and other staff;
- performance reports, because there is always room for improvement!
What are the advantages of a CMMS?
Almost all businesses agree on the advantages of a CMMS, namely the increase in team productivity, better cost control, and inventory optimisation.
Centralisation of information
If looking for information about the last repair you made to your air conditioning is pretty much like looking for a needle in a haystack, then you definitely need a CMMS.
The CMMS puts an end to lost paper and endless Excel sheets. From the moment you insert configure the software with all your information, it is very simple to find work plans, maintenance request logs, instruction manuals, and other types of files.
Non Stone-Age communication
With a CMMS, each team member receives a notification each time they are assigned a task. On the other hand, it eases the reporting of failures to the technical team, which also decreases the reaction time (and, in turn, important metrics like MTTR).
Increased productivity
According to a study published in July 2019, 86.7% of companies that use a CMMS notice an increase in employee productivity. On the one hand, maintenance managers take less time to assign tasks to their technicians, and on the other, technicians can find all the information they need quickly.
Reduced downtime
Whenever you leave a task in your backlog and drift from your maintenance plan, the probability of having an equipment breakdown increases. Another of the main advantages of a CMMS, reported by 82.8% of companies in the same study, is to reduce downtime, as the software makes it easier to schedule, control, and review all the preventive maintenance plans.
More preventive maintenance means less downtime and also less reactive maintenance, which equals cost reduction (unless there is excessive preventive maintenance):
Cost control
Remember when we asked you if you make your decisions based on intuition? With the data collected by CMMS and the automatic reports, you’ll start to make more informed decisions and predict how much you will spend on maintenance, with a greater degree of confidence. Thanks to this, about 89% of companies report an improvement in cost control when using a CMMS.
Furthermore, among the 64 companies in the study that reported “lack of information in decision-making”, only 5 continued to have the same complaint.
Increased asset lifetime
About 88.2% of companies mention that they can extend the lifespan of their assets with a CMMS. There are several possible justifications: the increase in productivity (which allows them to comply with their preventive maintenance plan more rigorously), the decrease in breakdowns, and, of course, detecting problems earlier with the quick failure reporting features.
Stock management
Another major advantage of using a CMMS is better stock control. This translates into less overstocking and less inventory shrinkage, which causes 88% of companies to reduce stock-related costs.
What are the main limitations of a CMMS?
Integration capabilities
One of the most significant drawbacks of a CMMS is its limited ability to integrate with other systems. Modern facilities often rely on a variety of software solutions for different aspects of management, including Building Management Systems (BMS), Energy Management Systems (EMS), and Enterprise Resource Planning (ERP) systems. A CMMS that is not able to seamlessly integrate with these systems can create data silos, leading to inefficiencies and a lack of comprehensive oversight.
Inflexibility and scalability issues
CMMS solutions are often rigid and lack the flexibility to adapt to the evolving needs of a facility. As organisations grow and their maintenance needs become more complex, a CMMS may struggle to scale accordingly. This inflexibility can result in increased manual workarounds and a higher likelihood of errors.
User experience and usability concerns
Many CMMS platforms suffer from poor user interfaces and a steep learning curve, which can result in low adoption rates among maintenance staff, reducing the effectiveness of the system. A clunky, difficult-to-use interface can also lead to errors and inefficiencies, negating the potential benefits of using a CMMS.
Reactive rather than proactive maintenance
While a CMMS can facilitate preventive maintenance to some extent, it often falls short of enabling truly proactive maintenance strategies in order to foresee potential issues before they become critical. These are very challenging to implement effectively with a traditional CMMS.
A shift towards a more integrated solution
There is a noticeable trend of facilities managers moving towards platforms that allow them to integrate and coordinate teams, assets, maintenance, procurement, compliance, sustainability and daily operations across all internal and external systems and processes.
In fact, a 2023 Verdantix report on the smart building market indicates that, whilst CMMS is still widely used, there is a growing interest in more integrated solutions. The report highlights that approximately 40-50% of surveyed large facilities are either considering or have already implemented those, indicating a significant shift.
On the other hand, according to Gartner’s research, about 60-70% of facility managers in small to mid-sized organisations still rely primarily on CMMS. This is largely due to budget constraints.
Factors influencing the shift
Technological advancements
The rapid advancement of IoT and big data analytics has made these solutions more attractive due to their ability to integrate seamlessly, for more efficient and proactive maintenance management.
Operational needs
Facilities with more complex operations, such as those in manufacturing, healthcare, and large commercial buildings, are more likely to adopt them, since the need for real-time data and comprehensive integration with other systems drives this shift.
Budget and resource allocation
Smaller facilities with limited budgets may be temped to continue to rely on traditional CMMS, due to lower costs and simpler implementation processes. However, as the cost of technology decreases and the ROI of advanced systems becomes more evident, even these facilities may start to consider a more holistic approach.
Increasing FM complexity
Systems are increasingly complex, regulations are stricter, customers have higher expectations and there is an ongoing pressure to be efficient, compliant and sustainable.
Expanding responsibilities
Facilities teams are expected to juggle a growing list of responsibilities — from asset management to maintenance, procurement, compliance, supplier management, sustainability… you name it!
Information overload
Data is coming from everywhere — field teams, assets, suppliers, customers — often scattered and without clear insights for informed decision-making.
Disjointed systems won’t survive
To keep up with today’s demands, they need a system that breaks down silos and connects every process, asset and person — from internal teams to contractors to building users — enabling their entire operation working as one.
How to choose the best CMMS?
A future-proof solution
Why adopt a maintenance management software if you’re going to keep living in the past? With cloud storage, all information becomes available at any time – at home, in the office, or working remotely from the Philippines.
Maintenance technicians are never idle, so it’s important to choose a CMMS that they can use “on the go” and jump from one task to the next. Here at Infraspeak, of course, we are also big fans of NFC tags for all kinds of purposes.
Flexible and adaptable
Your goals of today may not be your goals of tomorrow. Your company grows, the team expands, the market and the demands of your customers change. Look for a flexible and scalable solution to anticipate the needs of the future. At Infraspeak, you can choose the apps and addons that best suit your company and create your own dashboard.
Updates & integrations
This is a golden rule for any software: if it hasn’t been updated in months, it’s probably not a good idea. It is important to know that the team behind the CMMS is committed to improving it and taking your suggestions into consideration. Also, take advantage and check the integrations it has with other software (e.g. CRMs, fleet management solutions, or hotel management systems).
“The fact that the app’s menu is very simple helped a lot with the team’s acceptance. It works and I feel it’s an easy tool to use, offering a good user experience.” — Head of the Buildings Division at Matosinhos City Council, about Infraspeak
What are the challenges in using a CMMS?
Even with all the advantages we’ve discussed so far, it is normal that you still have some concerns regarding the implementation and use of a CMMS. In this section, we anticipate the three main challenges you may face and the reasons why they are, in fact, very easy to overcome.
Implementation
As with any change, there is always doubt and an adaptation phase. The trick is to choose the maintenance management software / platform that best fits your company — it must address your needs and integrate with the other software you are using.
Our dedicated specialists and unique delivery and implementation frameworks ensure faster time-to-value and much higher implementation success rates than the alternatives.
Adaptation
All the advantages of a CMMS depend on its correct use. Therefore, all employees who will use it need to participate in the onboarding phase. But rest assured: the most sophisticated platforms have mobile versions for smartphones and tablets, which are not unknown to anyone.
Data Security
It’s true that CMMS store sensitive information. Indeed, hacking is not a conspiracy theory.
But it is also true that most SaaS (short for Software as a Service) use information hubs with multiple layers of protection — not a company server, which is a much more vulnerable target. In fact, successful attacks on SaaS are extremely rare.
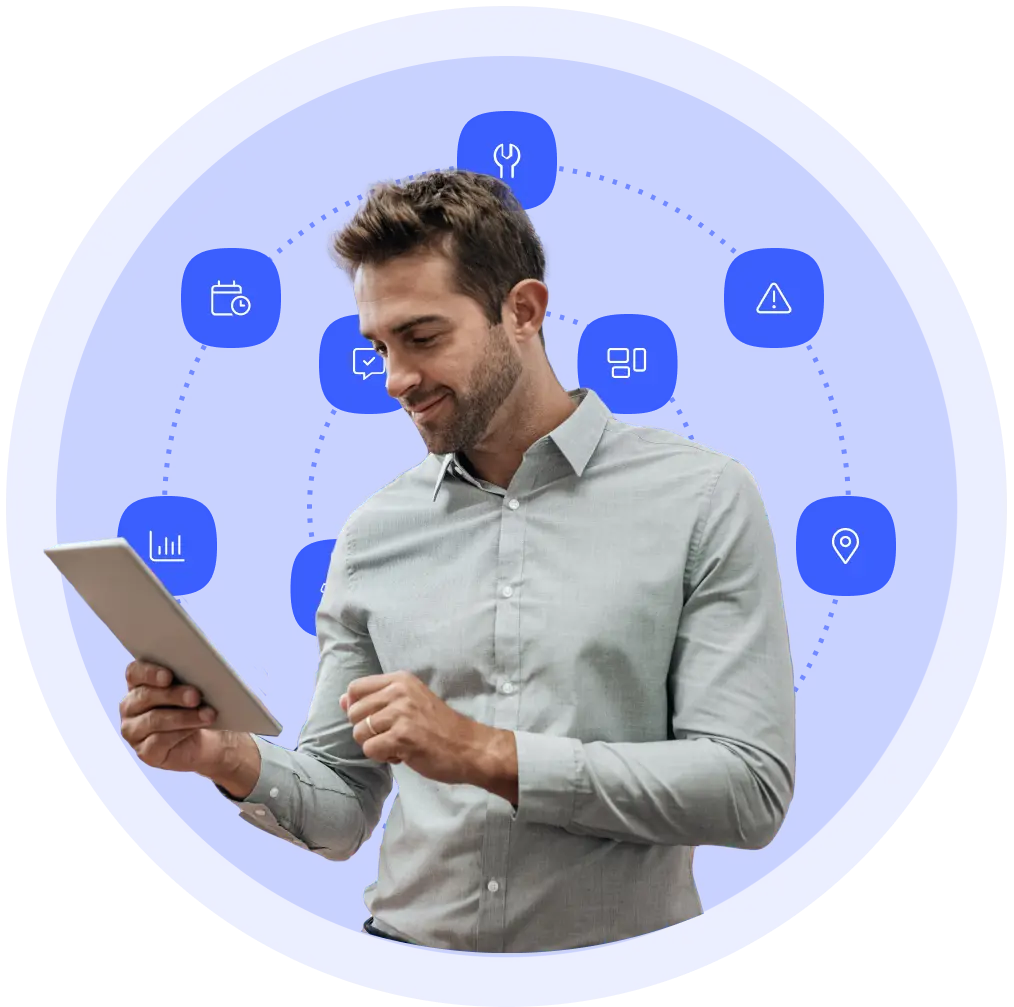