This might come as a shock, but preventive maintenance isn’t always right. As much as we advocate for timely maintenance, we must concede that preventive maintenance is time and people-intensive. Too much of it will leave you scrambling to answer emergency requests and footing a large bill. So if it’s not preventive maintenance all the way, what’s the right maintenance strategy for you?
Different types of maintenance
There are three classic types of maintenance – reactive, preventive and predictive. According to reliability engineers, an effective maintenance program should be a well-rounded affair between predictive (55-44%), preventive (35-25%) and reactive maintenance (10%). But which one should you use and for what?
Before we get there, let’s examine the different types of maintenance:
Reactive maintenance or “run to failure”
Instead of putting a lot of resources into preventing failures, just wait for them to happen and deal with the consequences later. This usually leads to expensive repairs, not to mention lengthy breakdowns that disrupt services. However, there’s a time and place for everything – including, as we’ll see, reactive maintenance.
Preventive maintenance prevents breakdowns
It can be either time-based (performed periodically, on designated time intervals) or usage-based (maintenance is performed only when the assets reach certain milestones). This type of maintenance is linked to reduced downtime and it’s easy to schedule, even in the long term, but it comes with the risk of over-maintenance. It also comes with upfront costs, even though it usually translates into a high ROI eventually.
Condition-monitoring tries to avoid over-maintenance
What if we could avoid over-maintenance? Condition-monitoring techniques aim to find the optimal time for maintenance. The twist is that condition monitoring can be as simple as using a dipstick to assess oil levels, or as complex as motor circuit analysis. In other words, it may be cheap or come with high upfront costs. Deciding whether it’s worth the investment or not varies greatly from asset to asset.
Predictive maintenance
Not to be confused with condition-monitoring, even though predictive maintenance is inconceivable without it. Predictive maintenance looks at data gathered with condition monitoring methods and uses algorithms to predict when a failure is happening. It’s a very promising strategy, but it invariably comes with high costs – both to develop accurate algorithms, and to install advanced condition-monitoring devices.
Reliability-centred maintenance (RCM)
Rather than a strategy, reliability-centred maintenance is an approach. It still relies on reactive, preventive and predictive maintenance. This approach focuses on recognising the failures that compromise the system the most and adopt the best strategy for each critical asset. The idea is to build a reliable facility or plant with maximum availability while keeping maintenance costs under control. And it all starts with 7 questions.
Total productive maintenance (TPM)
Another approach, in which every operator takes ownership of their equipment. The ultimate goal of TPM, as it is known, is zero downtime, zero defects and zero accidents. It’s supported by 8 pillars and it’s intimately connected to Industry 4.0.
How to Choose the Right Maintenance Strategy
We don’t want to oversimplify. However, in general terms, you can decide the right maintenance strategy based on these 4 questions:
- Does the total cost of failure exceed maintenance costs?
- Does each task address a specific failure mode?
- Does it address the failure at the optimal point?
- Is it the least expensive and most effective option for that failure mode?
Before you answer each of these questions, look at:
- criticality matrix
- historical data, including preventive maintenance vs. repair data
- root-cause analysis (FMEA, FTA, 5 Whys) for the common failures
If the cost of failure doesn’t exceed maintenance costs
Failure cost should take into account losses in production, potential fines and the cost of repair. If the total is less than the maintenance cost, then it’s cheap and easy to solve – consider applying reactive maintenance.
Please note: other incalculable factors, such as safety and compliance, should also be taken into account. However, if the asset ranks high in criticality, it is unlikely that the cost of failure won’t exceed maintenance costs.
If a maintenance action does not address a specific failure mode
You’re probably engaging in over-maintenance. Reevaluate your criticality matrix and decide whether that maintenance action can be performed by the employee who operates that piece of equipment.
If it does not address the failure at the optimal point
Chances are you’re engaging in over-maintenance again. If it’s preventive maintenance, reassess the plan to see if you can change from time-based maintenance to usage-based maintenance.
Another option is, of course, condition-monitoring or predictive maintenance. But don’t forget the first question: does failure cost exceed maintenance costs? Calculate costs, compare different techniques, and make a decision.
If it is not the most cost-effective option
If a maintenance strategy is expensive but effective, especially when it comes to high criticality assets or assets that are hard to repair (low maintainability), keep it. If its effectiveness is limited, consider changing to condition-monitoring (for critical assets) or reactive maintenance (if repairs are swift and inexpensive).
If you have a lot of critical assets at hand, answer the 7 questions of RCM. This will turn your focus to the most critical assets – and then come back here to decide which is the right maintenance strategy for each of them.
Final Recap
- if an asset is hard to monitor and the cost of failure is low, run to failure.
- if an asset is hard to monitor (or your budget does not allow for predictive maintenance) but the cost of failure is high, we recommend time-based preventive maintenance;
- if an asset is easy to monitor and the cost of failure is low, go with condition-based maintenance;
- if an asset’s condition is easy to monitor and the cost of failure is high, predictive maintenance will likely pay off.
Think you already nailed your maintenance strategy down? Efficiency is not just the right strategy but also how you execute it. Talk to one of our specialists and see how an intelligent maintenance management platform can help.
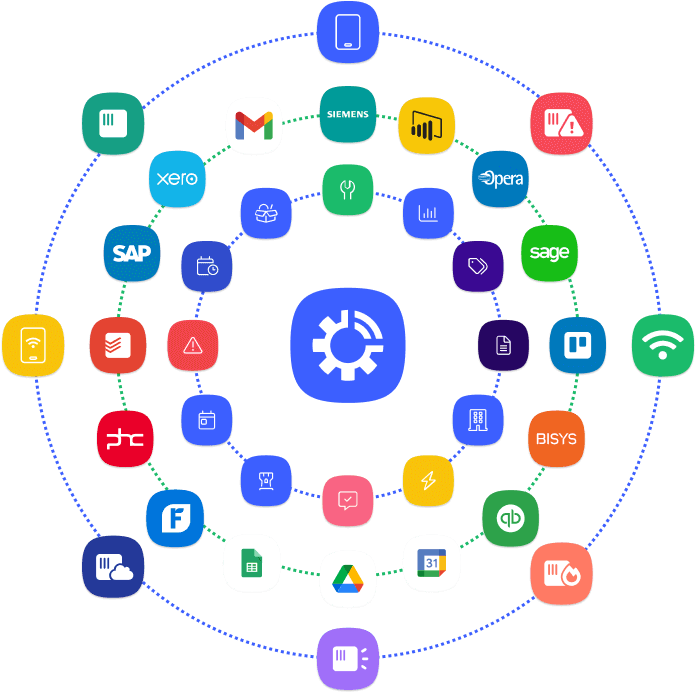