When we think about preventive maintenance, it is inevitable to think about planning. But there is no point in implementing planned preventive maintenance if you don’t have a good schedule because its execution will fail.
It would be like having an excellent recipe for a homemade beer, preparing your own malt, showing off to your friends… and then ruining it because you should have let it brew for another day. No planning works without a timetable, and that’s what brings us to this step-by-step to draw up a preventive maintenance schedule. Shall we?
0. Timeline vs. Preventive Maintenance Plan
The starting point for drawing up a preventive maintenance schedule is to distinguish the schedule from the plan itself. The preventive maintenance plan establishes priorities based on the criticality of the assets and defines all the tasks to be performed throughout the year. But in a sense, it is like stating that kids need to learn “English and Mathematics” — in other words, it is just a statement of intent. To make it happen, the school timetable has to be made and time divided between subjects.
This “schedule” is, as you may have guessed, the preventive maintenance schedule. The main difficulty is to calculate the exact time to be assigned to each task and fit it into the company calendar. If you overestimate the time a certain activity takes, you will waste time and money. On the contrary, if you set aside too little time, you risk delaying the entire schedule, compromising the plan and having dissatisfied technicians. And since we want to be a source of a good life for all maintenance teams around here, let’s go to step 1.
1. Determining Labor Productivity
The first thing you should keep in mind when drawing up a preventive maintenance schedule is the productivity of the workforce. Where are we going with this? It’s unrealistic to think that technicians are performing maintenance work 100% of the time. In fact, it is estimated that only 25-35% of the working hours are for actual work. You read it well: above 30%, you can already consider your team much more “productive” than the average.
The remaining “unproductive” hours are spent searching for tools, displacements, clarifying doubts, interruptions, and idleness. Although some of this time can be optimised with a good schedule (for example, avoiding necessary displacements), it is important to have realistic expectations. If you use maintenance management software, use the available data to see how many hours were actually spent on maintenance work in the same period.
📝 You may also like: 10 best preventive maintenance software
2. Analysing the Backlog
Before you start on a new schedule, you need to deal with the “elephant in the room”: the backlog of tasks. Or, in plain English, the list of tasks left unfulfilled from the previous maintenance plan. Even so, we recommend that you finish these pending tasks before going full speed ahead with a new schedule, because you can run… but you can’t hide.
3. Dig deep into the Preventive Maintenance Plan
Now it’s time to board Captain Obvious’s ship: you can’t draw up a good preventive maintenance schedule without digging deep into the preventive maintenance plan. You have to analyse all the tasks to calculate how many employees you need for each activity, how many hours you have to allocate (taking into account the productivity of step 1) and what materials and tools you will need for each task, among other things.
There is another key point: the schedule must also take ito consideration the best time to do scheduled maintenance. For example, if we are talking about a building that needs a new roof, it might be more cautious to schedule these works for the summer. If we are talking about completely renewing a hotel’s cooling system, it might be better to wait for the winter/low season. Make an effort to make the planned downtime as less damaging to your customers as possible.
4. Setting Priorities
“But shouldn’t that be laid out in the maintenance plan?” Of course, it should. But no maintenance plan, no matter how good, is 100% foolproof. As inconvenient as it is for all maintenance managers, the world does not work as an algorithm: breakdowns and unforeseen events will always happen. One way to address the problem is having some flexibility regarding the daily schedule and being specific only on a monthly or weekly basis.
The other answer is to set clear priorities on how to change the schedule during an unforeseen event. How should you react to each type of risk? What does an immediate response require, even if it means stopping the usual plan? What are the maximum response times you need to ensure? ” Predicting unforeseen events” is a game that, by definition, we can never win — but we can lessen the losses. Which is like avoiding that naughty backlog of step 2.
5. Scheduling the day-to-day
We have reached the last step. It’s worth recapping what was said before. You already know how many hours you need for each task (realistically, taking into account real productivity!); what tasks you have to finish and what tasks you have to start; what resources you will need for each one. So now all that’s left is to put the two pieces that were missing in the middle of the puzzle together: the dates and the times.
Finally, and to complete the cycle, remember that a well-designed preventive maintenance schedule also allows you to increase productivity. Avoid scheduling tasks that require large displacements after one another, gather activities that need the same type of tools and try to include all the necessary information in the work orders so that the technicians can act faster.
Extra: using a Preventive Maintenance schedule software
Infraspeak is a comprehensive maintenance management platform that allows you to set up and manage preventive maintenance schedules efficiently. Here’s what it can do for you:
1. Asset and Equipment Management
– Add and categorise all your assets and equipment
– Store detailed information about each asset, including manuals, specifications, and history.
2. Task Creation and Management
– Define preventive maintenance tasks for each asset
– Specify the procedures, tools, and materials needed for each task
– Set task priorities and estimated completion times.
3. Scheduling and Frequency Setting
– Set the frequency for each preventive maintenance task (daily, weekly, monthly, annually, etc.)
– Specify exact dates and times for tasks to be performed
– Use calendar views to visualise and manage the maintenance schedule.
4. Preventive Maintenance Plans
– Create comprehensive preventive maintenance plans that group tasks together
– Assign these plans to specific assets or groups of assets
– Adjust plans dynamically based on changing requirements or findings.
5. Automated Work Orders
– Automatically generate work orders based on the preventive maintenance schedule
– Include detailed instructions and checklists in work orders
– Track work order progress and completion.
6. Technician Assignment and Management
– Assign preventive maintenance tasks and work orders to specific technicians or teams
– Manage technician schedules and workload to ensure balanced task distribution
– Track technician performance and task completion rates.
7. Notifications and Alerts
– Set up notifications and alerts for upcoming maintenance tasks
– Receive reminders for overdue tasks or missed schedules
– Customise alert settings based on priorities and criticality.
8. Reporting and Analytics
– Generate reports on preventive maintenance activities, including task completion rates, downtime, and costs
– Analyse data to identify trends, common issues, and areas for improvement
– Use insights to optimise maintenance schedules and procedures.
9. Mobile Access
– Use the Infraspeak mobile app to access and manage preventive maintenance schedules on the go
– Allow technicians to receive, update, and complete tasks in real-time using their mobile devices.
10. Integration with Other Systems
– Integrate Infraspeak with other software systems (e.g., ERP, BMS) to streamline data flow and enhance maintenance management
– Use API integrations to automate and synchronise maintenance schedules with other operational processes.
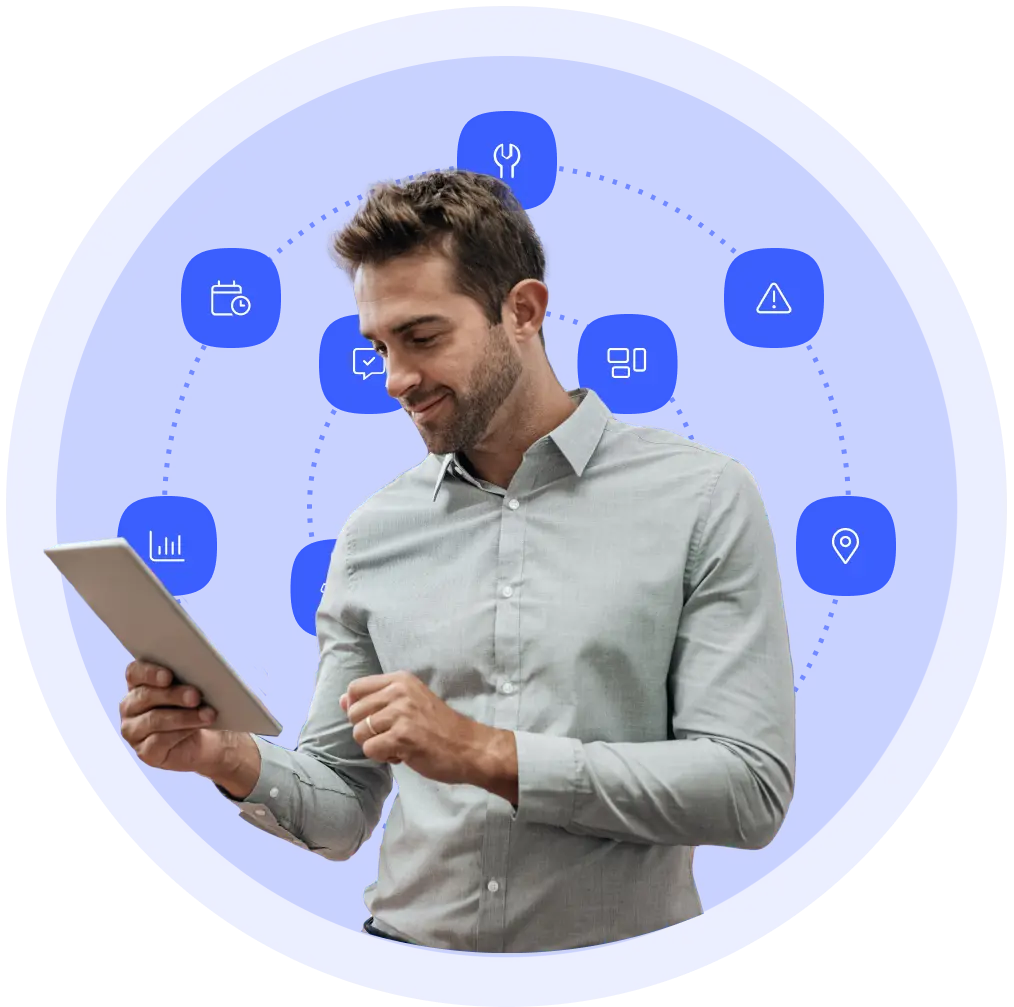