When there’s only one option left, it’s easy to make decisions. That’s why many companies only worry about maintenance after a breakdown. Until it reaches a critical point, one of no return, there’s ‘faith’ that everything will be fine. But, if you’re not feeling much of a believer, today we explain how to create an asset maintenance strategy.
1. What, where, in what condition
The first step in defining an asset maintenance strategy is to do the “reconnaissance” work. How many assets do you have? What type of assets? Where are they located? In what condition are they operating? In other words, you need to do a criticality analysis.
Another way to look at this question is to ask, “if an asset fails, what are the consequences?” Does it lead to loss of production? Does it cause safety problems? Environmental problems? How does it prevent the institution from achieving its goals or fulfilling its mission? Criticality analysis should be holistic, not least because there are assets that should never fail.
Want a real-life example? In 2018, daily breakdowns in radiotherapy equipment at São João Hospital in Porto, Portugal, meant that several users were unable to fulfil their treatment plan. In the most serious case, one patient waited from April to October to start treatment, which reduced his life expectancy.
Unfortunately, this was not an isolated case. A study published in 2008, based on patient data from a hospital in S. Paulo, Brazil, came to the conclusion that maintenance is the main cause for the interruption of radiotherapy treatments (55%), far above reactions to treatment (6%) or clinical worsening (3%).
2. Find the source of the breakdowns
Now it’s time to find the “rotten apple”: what is failing the most and consuming the most resources? Watch out, it is easy to get carried away by intuition. “But we are always repairing the lift in building x” is not an argument. Analyse the data! Evaluate the downtime costs, the repair costs, and the severity of the consequences. This cross-check should define your priorities.
When you analyse the consequences of the breakdown in terms of quality, safety, and environmental impact, as well as all the financial aspects, you will arrive at a reduced (or at least hopefully reduced!) set of critical assets. These are assets that you should focus on first.
The goal is to understand why these assets are failing and how they might fail. To do this, we need to retrieve one of our best weapons: root cause analysis. You can read here our full guide to root cause analysis and how to use some of the most common tools.
Root cause analysis can reveal some uncomfortable truths about your management. For example, you may discover that you are misusing equipment, that you are exceeding the number of cycles recommended by the manufacturer, or that your maintenance plan is insufficient.
Still on the breakdowns at S. João Hospital, the hospital’s management admitted in 2019 that the radiotherapy equipment in question was “very old” and lacked “the robustness needed to work continuously”. The hospital eventually replaced the device, already at the end of its life, with a completely new one. Regarding this case, you can see here how to calculate an asset’s life expectancy.
📝 You may also like: 10 best asset management software
3. Plan, manage and assess
Phew! We need a moment to catch our breath. By now, you know (1) which assets are most critical, (2) the consequences of breakdowns on these assets, and, through root cause analysis, (3) what causes these breakdowns. Therefore, you have all the information you need to start designing your strategy.
Whenever you decide to repair and not replace the asset, you must re-evaluate the maintenance plan:
Optimise preventive and predictive maintenance
The best way to avoid prolonged breakdowns and maintain the reliability of your assets is to optimise condition monitoring, preventive maintenance, and predictive maintenance. To do this, you must make sure that each scheduled work order prevents or detects a specific, predictable failure mode.
⚙️ Here’s how to choose the right maintenance strategy.
Defining/improving your maintenance plan
Next, you need to review your maintenance plan. If you already have a robust maintenance plan in place, remove tasks that do not correspond to a failure mode and implement new practices according to the results of the root cause analysis. Don’t forget to set KPIs to compare the “before” and “after”.
If this is the first time you are going to make a long-term plan, we have simplified how to make a maintenance plan in 5 steps.
Managing work orders and resources
Let’s go from theory to practice! Your work orders should be clear and complete to reduce intervention time to a minimum. We suggest you use an Intelligent Maintenance Management Platform to schedule work orders and link all costs and materials automatically. This way you get more reliable data for the next criticality assessment.
☑️ Do you need a template for your work orders? Download our template for work orders (free and without forms!).
Generate reports and evaluate results
If you have recorded all the information in your maintenance management software, you can generate automatic performance reports. This allows you to track KPIs you have defined and evaluate results: did it solve the problems you identified? Or do you still need to improve? Are there any assets that are beginning to require more care? Restart the cycle.
9 good practices in asset management
Make communication easy
A lot of different people will use and interact with assets over the course of their lifecycles. From capital allocation, installation and daily use to maintenance, repair, and eventual disposal — assets involve personnel across a bunch of departments.
Facilitating smooth communication between these departments is one of the most important enterprise asset management best practices. This ensures repairs are not delayed by communication delays, as decisions can be made quickly.
Modern asset management solutions, such as Infraspeak, use mobile alerts to ensure parties can communicate instantly and all have access to the same information in real time via the cloud.
Technicians, for example, can use an Intelligent Maintenance Management Platform (IMMP) to generate reports on the performance and condition of an asset. This can then be sent to managers, who can then make informed asset viability and cost-effectiveness decisions.
Standardise guidelines
Creating standardised guidelines makes sure everyone knows their roles and responsibilities.
Ideally, you should write guidelines in clear, plain language and make them accessible to all staff, contractors, and third parties if necessary. This way, anyone interacting with Enterprise Asset Managament (EAM) software and assets will understand what’s required of them.
Your guideline documentation should include rules and advice regarding the following:
- Standard operating procedures for completing tasks (e.g. lockout tagout)
- Responsibilities of specific roles (managers, technicians, staff, etc.)
- Preventive maintenance checklists
- Tracking and updating MRO inventory
- Supplier and vendor negotiation guidelines
- Onboarding personnel to asset management’s best practices
Capture as much data as possible
EAM solutions act as a centralised database of asset information with the ability to monitor data in real-time. This involves utilising sensors, IoT devices, and live data feeds to gather as much usable asset information as possible.
Technicians and staff should also understand how to use EAM software to update asset data to ensure accurate records.
Data should include:
- Procurement and installation dates
- Make, model, and location
- Repair and maintenance information
- Temperatures
- Performance metrics
These measures will help you make informed decisions when necessary. The more data, the better, as AI EAM solutions, such as Infraspeak, can now analyse this information and recommend preventive actions.
This allows asset professionals to precisely monitor the efficiency and cost-effectivity of assets.
Improve financial planning and efficiency
As you analyse the entire asset life cycle, you can better predict what the useful life of each piece of equipment is and when is the right time to replace it. This means you can plan much better the purchase of equipment and the cost of maintenance at each stage of the asset’s life.
Assure compliance with processes and standards
Finally, by monitoring all your assets and ensuring they remain reliable, you can meet all your industry standards and ensure compliance with quality and safety rules.
📝 You may also like: Why inventory control is crucial for streamlining facility operations
What is Enterprise Asset Management?
Track assets over their whole lifecycle
Asset managing professionals use intelligent software to track and monitor assets at every stage — from procurement to disposal. This way, you not only know when a machine needs repair, but you can also see when a machine has become inefficient.
Fed enough data, these solutions allow you to spot discrepancies that can prevent major downtime. And, with work order management built in, IMMPs can generate preventive actions automatically, making the life of asset managers a lot easier.
Utilise preventive and predictive maintenance
Unscheduled downtime can cause you and your organisation a lot of headaches.
As well as your existing asset maintenance strategy, this should involve preventive maintenance and also predictive maintenance. These features are included in modern enterprise asset management software. Then, this can automatically schedule maintenance when assets are due and use performance benchmarks and even AI to predict repairs for you.
Using a combination of preventive and predictive maintenance with EAM-savvy technicians, you can then keep assets running at their best now and in the future.
Use NFC tags
To keep track of assets more efficiently, use Near Field Communication (NFC) tags. These allow technicians and other personnel to quickly access information about an asset using their mobile.
Technicians can use NFC tags to quickly pull up information such as a manual or previous maintenance record. Managers can then register when and where technicians are on-site for their records.
This also dramatically improves data capture with a seamless connection to the asset in EAM software. Infraspeak is innovating NFC technology in the maintenance space with our strong, weatherproof tags capable of lasting nearly 30 years.
Store documentation on the cloud
Use EAM software to store documentation securely online.
This way, everyone within an organisation knows where they can find documentation regarding an asset. For technicians, this could be a manual for a machine, allowing them to complete a repair sooner. Managers, too, can find compliance documentation to stay on the right side of the law and SLAs.
You can therefore use enterprise asset management software as a repository for all your asset and compliance documentation.
Set goals and monitor KPIs
Asset managers should work with other departments to establish goals. This could be to reduce repair costs by 10%, improve uptime by 10%, or even eliminate the need for enquiring phone calls, freeing up managerial time.
Whatever your goals are, achieve them by establishing your key performance indicators (KPI) and benchmark metrics within EAM software. Consider KPIs such as Mean Time to Repair (MTTR), Mean Time Between Failure (MTBF), and Overall Equipment Effectiveness (OEE) or set your own using EAM software.
Enterprise asset management software allows you to track and monitor these KPIs in real time and catch anything amiss before it upsets your goals.
Scale and adapt accordingly
EAM software should be scalable and agile enough to meet the growing demands of your organisation. This means your EAM platform should have a comprehensive suite of features and include the ability to expand data storage and access.
Be sure to use EAM software that allows you to switch features on and off as you need them. This can streamline the EAM process for users and allow integrations to other platforms for expanded capability.
Choosing an asset maintenance management strategy
Wrapping up…
Over the asset’s useful life, it is important to choose the right maintenance strategy for each asset. But again, you need to take a holistic view and consider the entire asset portfolio — not just each asset in isolation. A good asset maintenance strategy makes for more reliable assets. That’s what allows us to offer a quality service to users. But performing a good asset maintenance management involves knowing the condition of each piece of equipment, understanding its life cycle, and scheduling maintenance according to these variables.
A first assessment is essential to first understand what the appropriate conditions to operate each piece of equipment are. It allows you to classify them according to their criticality, which is essential to define priorities.
Next, you need to analyse the potential causes of failure. Conducting a root cause analysis is extremely valuable in this part of the process. Each predictive or preventive work order should correspond to a specific cause of breakdown to ensure no work is done in vain.
Finally, don’t forget to define the main performance indicators (such as MTBF, MTTR, OEE, among others). Thanks to these indicators, you will understand whether your strategy is being effective and make more informed decisions. After all, “information is power”!
Technology is a great ally in this whole process. An Intelligent Maintenance Management Platform is key to manage the entire portfolio, monitor the status of assets in real-time, plan maintenance, calculate KPIs, and generate automatic reports.
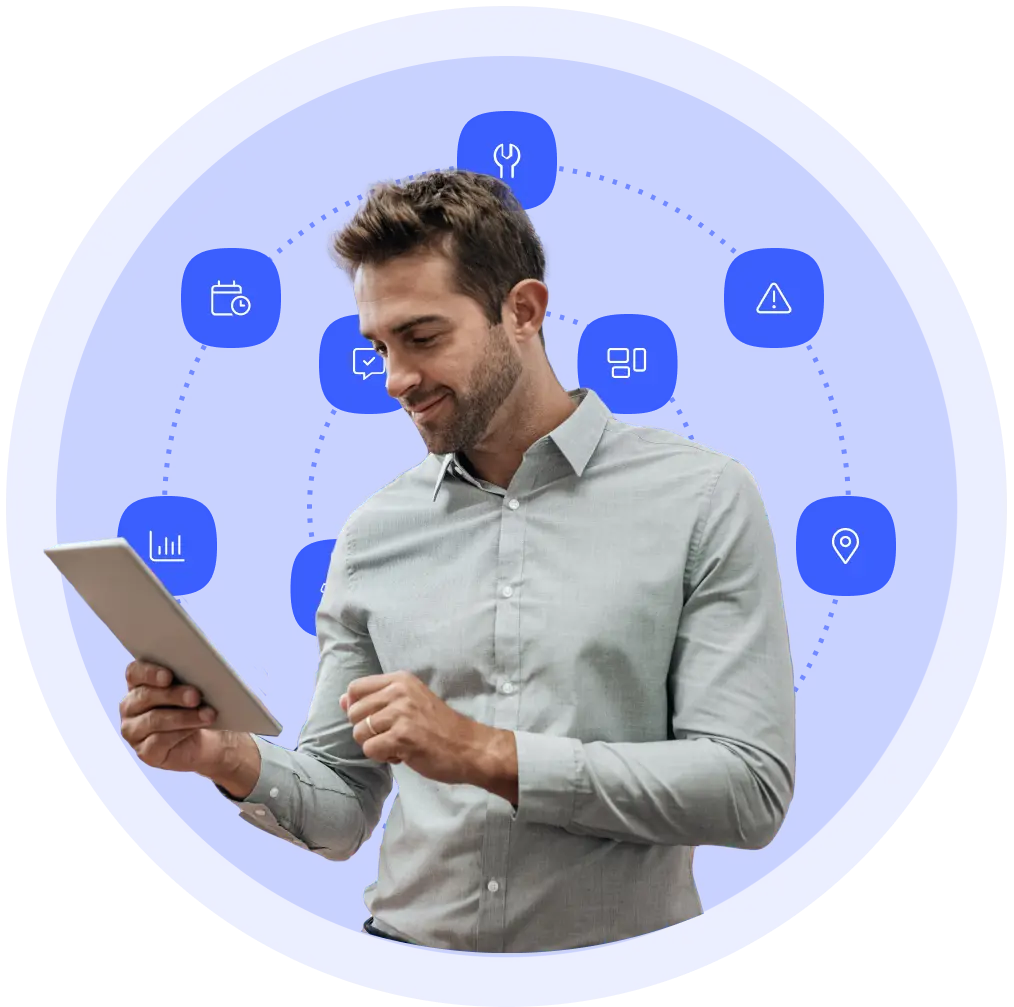