What is Time-Based Maintenance?
At its core, Time-Based Maintenance is a proactive maintenance strategy where equipment is serviced or replaced at predetermined intervals, irrespective of its actual condition. This scheduled approach aims to prevent unexpected breakdowns and extend the operational life of assets.
In the ever-evolving landscape of maintenance strategies, Time-Based Maintenance (TBM) stands as a stalwart approach to ensuring the longevity and efficiency of machinery and equipment.
Examples of Time-Based Maintenance
- Regular oil changes in vehicles
- Routine inspections of electrical panels
- Periodic cleaning of air filters in HVAC systems
- Greasing and lubrication of Machinery
These actions are performed based on a predefined time interval rather than waiting for signs of deterioration.
Advantages of TBM
The adoption of Time-Based Maintenance offers several advantages to industries and businesses:
Predictability and Planning
One of the key benefits of TBM is its ability to provide a predictable maintenance schedule. This enables organisations to plan and allocate resources efficiently, reducing the risk of unexpected downtime.
Extended Equipment Life
By consistently addressing wear and tear, Time-Based Maintenance contributes to the prolonged life of equipment. This, in turn, leads to a better return on investment and reduced capital expenditures on premature replacements.
Compliance and Safety
In industries where compliance with safety regulations is paramount, TBM ensures that equipment is regularly inspected and maintained, promoting a safer working environment for employees.
Disadvantages of TBM
While Time-Based Maintenance has its merits, it’s essential to acknowledge its limitations:
Over-Maintenance
One notable drawback is the risk of over-maintenance. Performing tasks strictly based on a predetermined schedule may lead to unnecessary maintenance, resulting in increased costs without corresponding benefits.
Ignoring Actual Equipment Condition
TBM doesn’t take into account the real-time condition of equipment. If an asset requires maintenance before the scheduled interval, TBM may overlook these critical signs, potentially leading to breakdowns.
📝 Read also: What is Condition-Based Maintenance?
When to use Time-Based Maintenance
Determining when to implement Time-Based Maintenance depends on various factors, including the type of equipment, industry regulations, and the criticality of the asset. Generally, TBM is suitable for assets with predictable failure patterns and those where preventive actions can be applied effectively.
Differences between Time-Based Maintenance and Condition-Based Maintenance
Time-Based Maintenance (TBM) and Condition-Based Maintenance (CBM) are two distinct approaches to managing maintenance activities. Here are the key differences between them:
Timing of Maintenance
- TBM: Maintenance tasks are performed at predetermined intervals, regardless of the actual condition of the equipment.
- CBM: Maintenance is triggered based on the real-time condition of the equipment, using sensors and monitoring systems to detect signs of degradation.
Cost Implications
- TBM: May lead to over-maintenance, as tasks are performed according to a fixed schedule, potentially increasing costs.
- CBM: Tends to be more cost-effective, as maintenance is performed only when necessary based on the actual condition of the equipment.
Complexity of Implementation
- TBM: Generally simpler to implement as it relies on predefined schedules and routine tasks.
- CBM: Requires sophisticated monitoring systems, sensors, and data analytics, making it more complex and technologically advanced.
Flexibility and Adaptability
- TBM: Offers less flexibility, as maintenance tasks are determined in advance and may not adapt to rapidly changing equipment conditions.
- CBM: Provides greater adaptability by responding to real-time data, allowing for more dynamic and flexible maintenance planning.
Risk of Unplanned Downtime
- TBM: May result in unexpected breakdowns if equipment fails before the scheduled maintenance interval.
- CBM: Reduces the risk of unplanned downtime by addressing potential issues as soon as they are detected, minimising the impact on operations.
Equipment Monitoring
- TBM: Relies on a calendar-based approach and historical data, without continuous monitoring of equipment conditions.
- CBM: Involves continuous monitoring of equipment using sensors and IoT devices, enabling proactive maintenance based on real-time data.
Optimisation of Resources
- TBM: May lead to suboptimal resource allocation, as maintenance activities are performed based on a fixed schedule.
- CBM: Optimises resource allocation by focusing efforts on equipment that actually requires maintenance, reducing unnecessary tasks and associated costs.
Applicability to Different Equipment
- TBM: Generally suitable for equipment with predictable failure patterns and where preventive actions can be applied effectively.
- CBM: Particularly effective for critical or complex equipment where real-time monitoring provides valuable insights into performance and potential issues.
How to optimise your Time-Based Maintenance programme
Data-Driven Decision Making
Incorporate data analytics and predictive maintenance tools to enhance the accuracy of your maintenance schedules. You can do so by utilising historical data and real-time monitoring to refine the timing of maintenance activities.
Continuous Improvement
Regularly assess and reassess your TBM programme. This will allow you to evaluate the effectiveness of your maintenance tasks, identify areas for improvement, and adapt your strategy accordingly.
Training and Skill Development
Empower your maintenance team with the necessary skills and knowledge. Well-trained personnel can identify potential issues more effectively and contribute to the success of your TBM programme.
Intelligent Maintenance Management Platforms and TBM
An intelligent maintenance management platform can significantly enhance the effectiveness of Time-Based Maintenance by leveraging advanced technologies and data-driven insights. Let’s delve into the ways such a platform can assist in optimising TBM:
Intelligent Analytics
An IMMP can analyse historical data and equipment performance to predict potential failures. By identifying patterns and trends, it can forecast the optimal time for maintenance tasks, reducing the likelihood of unplanned downtime.
Real-Time Monitoring
Utilising sensors and IoT devices, the platform can provide real-time monitoring of equipment conditions. This allows for a more dynamic approach to maintenance, addressing issues as they arise rather than relying solely on predefined intervals.
Data-Driven Decision Making
The platform empowers maintenance managers with comprehensive data analytics and reporting tools, which allows for continuous improvement by assessing the performance of TBM strategies, identifying areas for optimisation, and making informed decisions.
Resource Optimisation
By optimising maintenance schedules based on real-time data, the platform helps in efficient resource allocation. This prevents unnecessary downtime and minimises costs associated with both over-maintenance and emergency repairs.
Integration with IoT and Industry 4.0 Technologies
The integration with these technologies enables a more interconnected maintenance ecosystem. The result? Seamless data exchange between various systems, providing a comprehensive view of the entire maintenance landscape.
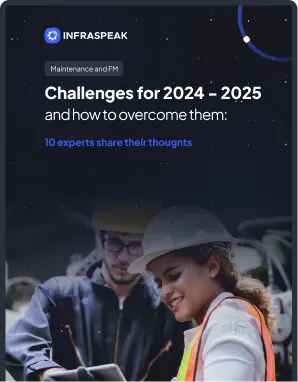