Interoperability, within the context of maintenance management, is the capacity of systems, applications, and devices to connect, communicate, and function together harmoniously.
In today’s highly connected digital landscape, getting systems to “talk to each other” is crucial. Otherwise, data remains siloed – stagnant – when it could drive efficiency across multiple systems.
For instance, in one Deloitte study, 75% of businesses reported data siloing and interoperability issues. A second study by Mulesoft found 38% of surveyed businesses reported system interoperability as the chief barrier to digital growth.
This concept goes beyond mere compatibility between different systems – it’s about achieving a well-orchestrated synergy among diverse technologies.
Impact of interoperability in maintenance
Integrating software systems like ERPs, facility management software, accounting software, and automation platforms has multiple impacts. The exact benefits depend on your software stack, but here’s a small selection of what maintenance interoperability can do:
- Improved workflow efficiency: Interoperability allows for fluid data exchange between different systems. This leads to faster data exchange, streamlined workflows, and reduced operational delays. Build automated workflows that minimise human input and drive efficiency.
- Enhanced decision-making: Additionally, interoperability permits the integration and analysis of data from multiple sources. For maintenance purposes, this enables organisations to network different software platforms like ERPs, BIs, accounting software and IoT platforms.
- Delivering effective outcomes: Integrating software platforms is a force multiplier – it squeezes that bit extra out of your data to build a quicker, more efficient system. For example, instead of manually copying data from one platform to another, you can directly integrate to automate work orders with accounting software or maintenance operations with productivity software. This increases building performance and asset reliability.
Interoperability and productivity
Integrating maintenance systems with other software boosts productivity for maintenance managers, technicians, and other staff involved in the operation and maintenance of buildings and their assets.
Here’s how:
Reducing manual labour
Firstly, interoperability reduces the need for manual data entry across multiple systems. It’s no secret that manual data entry is time-consuming and risks human error.
According to a study by Experian, 84% of organisations report that inaccurate data directly impacts their bottom line.
Automating data entry processes across systems reduces the time spent on data entry tasks and lessens the risk of human error.
This ensures accurate, reliable data exchange – and means staff can redirect their focus to other critical tasks.
Teamwork and collaboration
Interoperability enhances communication among maintenance managers and their teams. A study by McKinsey found that improved communication and collaboration through technology raise the productivity of workers by 20 to 25%.
Interoperable maintenance systems enable teams to share updates, data, and information between departments, making tracking progress on tasks easier and ensuring everyone is on the same page.
For instance, maintenance workers can quickly relay information about asset status to their managers or other departments. Managers can track maintenance schedules and task completion in real-time, enabling them to allocate resources more efficiently.
This efficient flow of information fosters a collaborative maintenance environment and reduces miscommunication.
Data sharing
If you run multiple software systems to manage buildings, assets and teams, getting them to share data just makes logical sense. Indeed, McKinsey showed that organisations that network their systems outperform those that don’t.
Moreover, interoperability provides a unified view of operations. Maintenance managers can comprehensively overview all activities, resources, and tasks from a single platform.
With all the data at their fingertips, maintenance managers can monitor and analyse performance, identify bottlenecks, and address issues.
Examples of interoperability in maintenance
There are numerous examples of cross-platform communication between different systems, and the exact configuration depends on your software stack.
By allowing systems to work together, interoperability improves efficiency, reduces the potential for human error, and ensures a seamless flow of data between various platforms.
Below are three key examples that showcase the potential of interoperability in maintenance management.
ERPs – SAP
Interoperating maintenance management software with the SAP ERP enables businesses to automatically issue invoices when they buy or sell services and materials.
Linking maintenance management to ERPs enables automated inventory management systems, ensuring stock levels are always accurate and up-to-date.
Accounting – Xero
Integrating with Xero enables the automatic creation of invoices in Xero whenever a sale is processed through your maintenance management software.
This simplifies your accounting procedures and ensures that financial records are updated in real-time, eliminating the chances of errors due to manual data entry.
Industry-specific – Opera
Regarding hotel management, integrating your maintenance software with Opera can streamline housekeeping operations with automatic check-in and check-out registrations and real-time room status synchronisation.
This enables maintenance staff to respond quickly to any issues, boosting productivity.
Interoperability challenges
Building integrated systems involves several frictions related to data sharing, security and establishing functional interoperability frameworks for multi-vendor software.
Before API integration, a lack of mutual interoperability standards complicated the process of linking different platforms together. This has changed, making interoperability far more straightforward.
- Challenges include technical issues like the absence of standardised, interoperable protocols for data exchange – though this has been largely alleviated by APIs.
- There are also data security concerns to consider and potential resistance from personnel accustomed to traditional systems.
- Setting up interoperable systems is initially time-consuming.
Interoperability and integration between different software systems have become more straightforward in recent years. It’s now possible to build intuitive and easy-to-use automated workflows.
Interoperability and intelligence: the role of IMMPs
Interoperability enables organisations to multiply the potential of their software and data, streamlining maintenance tasks and creating a slicker, high-performing workflow that benefits everyone involved.
This is precisely what Intelligent Maintenance Management Platforms (IMMPs), like Infraspeak, does. Infrapeak’s IMMP is a powerful, intelligent maintenance management tool that equips maintenance managers with a plethora of tools for improving their building and asset performance.
Additionally, Infraspeak Hub offers integration with Xero, SAP, Opera, Zendesk, Teams, Sage, Google Calendar and more, enabling you to share data, build intuitive automated pipelines and unlock new approaches to maintenance management.
Infraspeak offers extensive integration options, allowing for effective collaboration between different systems. Book a demo to explore cutting-edge maintenance and facility management.
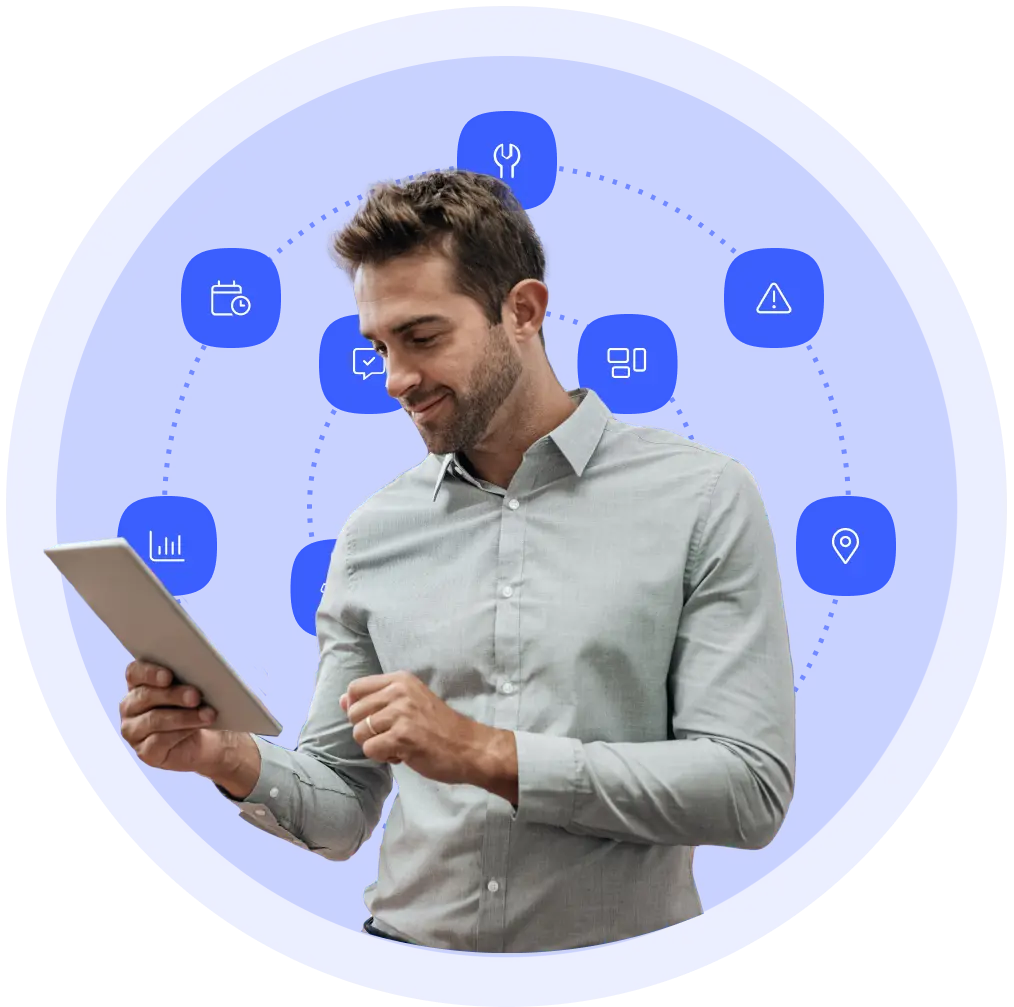