Não há um gestor de manutenção que não gostaria de prever quando um dano vai acontecer. Mas, já parou para pensar como fazer isso? A IoT dá uma ajuda. Recorrendo a sensores e novas tecnologias que monitoram sinais de deterioração e alterações no desempenho das máquinas, os gestores podem estimar quando uma falha vai acontecer. E assim nasceu um novo tipo de manutenção, a manutenção preditiva.
O que é a manutenção preditiva?
A manutenção preditiva é uma estratégia de manutenção proativa, cujo objetivo é evitar danos. Considerando os dados recolhidos e algoritmos preditivos pré-definidos, é um meio de tentar estimar quando um dano vai acontecer. Depois, as atividades de manutenção são programadas com base nessas previsões.
Agora, precisamos fazer uma pequena observação. A manutenção preditiva é muitas vezes confundida com a manutenção com base na condição, mas há um detalhe importante que as distingue. Enquanto a manutenção preditiva programa as tarefas com base nos dados recolhidos e em fórmulas, a manutenção baseada na condição só age quando esses parâmetros atingem níveis alarmantes.
⚙️ Entenda a diferença entre a manutenção preditiva e a manutenção baseada na condição
Como a manutenção preditiva funciona?
Em teoria, é fácil entender como a manutenção preditiva funciona. Ela acontece por meio da reunião de informação sobre os seus ativos. A partir daí, são extraídas informações que permitem calcular quando é necessário fazer manutenção. Na prática, podemos dividir o processo em três etapas:
Recolha de Dados (data collection)
Como já vimos, a ideia é prever quando um dano vai ocorrer. Como isso depende de obter dados de qualidade, o primeiro passo é instalar sensores capazes de recolher informação em tempo real sobre o desempenho e a ‘saúde’ do equipamento.
Os dados que estes sensores precisam medir e recolher dependem das técnicas que pretende se usar para monitorar o equipamento. É possível controlar a vibração, temperatura, pressão, o nível de ruído ou os níveis de corrosão, entre outros, segundo o que for mais indicado para o seu equipamento. Vamos explorar diversas ferramentas de manutenção preditiva daqui a pouco.
Prospecção de dados (data mining)
Acumular dados sobre os seus ativos não serve para nada se você não souber como os explorar. É a Internet das Coisas (IoT) que permite que os sensores enviem toda a informação para um sistema central ou software de gestão de manutenção que te permite analisar o que se está acontecendo. A manutenção preditiva é muito mais eficaz e muito mais cirúrgica em sistemas onde os diversos ativos estão integrados.
Cálculos e “Machine Learning”
Algumas pessoas podem acreditar que a manutenção preditiva fica por aqui. Mas se você está agindo apenas quando os sensores detectam problemas, você está apenas executando manutenção baseada nas condições – como vimos acima. Os grandes diferenciais da manutenção preditiva são a construção e a aplicação de algoritmos que oferecem um prognóstico.
No início, você pode se basear no histórico do equipamento, logs de manutenção e estatísticas (os relatórios do seu CMMS são extremamente úteis neste passo). No entanto, à medida que a Inteligência Artificial fica cada vez mais sofisticada, é possível detectar anomalias ainda mais cedo, encontrar correlações e receber sugestões inteligentes para prevenir um dano. Esta manutenção inteligente está dando origem a um novo tipo de manutenção, a manutenção prescritiva.
Ferramentas de Manutenção Preditiva, Aplicações e Exemplos
Por isso é tão importante encontrar os testes não destrutivos (NDT, do inglês non-destructive testing) indicados para diagnosticar as falhas dentro da infraestrutura.
Os testes não destrutivos são técnicas que não comprometem nem danificam o equipamento analisado, assim como os testes numa consulta de rotina no médico. Análises de sangue, ecografias, ecocardiogramas, exames oftalmológicos: nenhum deles faz mal, mas fazem parte de qualquer checkup.
Entre as técnicas mais avançadas de manutenção preditiva estão a análise de vibração, análise de óleo, acústica, testes de infravermelho ou imagem térmica (termografia) e a análise de circuito de motores (em inglês, motor circuit analysis).
Análise termográfica e análise de infravermelhos
- aplicações: conexões e sistemas elétricos, sistemas de aquecimento, analisar fluídos, padrões de descarga, manutenção de coberturas
A análise termográfica consegue detectar desgaste, corrosão, delaminações e desconexões que ainda não conseguimos ver a olho nu.
A vantagem dos infravermelhos é que permitem fazer mapas de temperaturas, inclusive à distância. Esta técnica é usada, por exemplo, na manutenção de sistemas de aquecimento. As variações de temperatura são úteis para avaliar a condição de motores e componentes mecânicos, elétricos, o isolamento do edifício e até o estado dos painéis solares. A grande desvantagem é que não pode ser utilizada em superfícies refletoras.
🤖 No futuro, a análise de temperatura ao CPU será uma das principais formas de testar a saúde dos robôs.
Análise de circuitos do motor
- aplicações: avaliar a degradação do motor, o alinhamento do eixo e do rotor, o isolamento, as engrenagens, despistar curto-circuitos
A análise de circuitos do motor usa uma técnica conhecida como electric signature analysis (ESA), ou análise de assinatura elétrica, em Português, para encontrar problemas em motores elétricos. Além de analisar o circuito e as componentes, avalia a voltagem e a corrente que entram no motor. Não menos importante: funciona em motores AC e DC e pode ser utilizada enquanto o equipamento está funcionando.
Análise de óleo
- aplicações: turbinas, sistemas hidráulicos e eletro-hidráulicos, avaliar motores, transmissões, engrenagens e os níveis de lubrificante
O objetivo da análise de óleo é testar a viscosidade, a quantidade de água e a presença de outros materiais, incluindo metais, para determinar o desgaste do equipamento.
Tenhamos em conta um sistema hidráulico que consiste em duas componentes base, as partes móveis e o lubrificante. À medida que o equipamento se desgasta, a amostra vai mostrar partículas produzidas pelo superaquecimento e pelo processo de oxidação.
Diferentes partículas revelam diferentes danos em diferentes componentes. Por exemplo, a presença de silicone acima das 15 ppm pode indicar que o isolamento está se desgastando, enquanto o sódio pode denunciar contaminação com água salgada. Siga um guia de metais (página 71, informação em inglês) quando estiver usando o espectómetro.
Análise de vibração
- aplicações: testar o alinhamento das componentes, despistar desequilíbrios, folgas, ressonâncias, falhas de engrenamento
Este tipo de análise é ideal para equipamentos e máquinas rotativas, como compressores, bombas de água e motores. O que fazemos é ligar um sensor capaz de detectar movimentos ou aceleração, conforme o caso. O sensor detecta ondas de som criadas pelo movimento, que por sua vez geram impulsos elétricos e fazem vibrar o equipamento.
Portanto, esta técnica de manutenção preditiva é ideal para infraestruturas com um sistema de fornecimento de água complexo, como hotéis, spas ou parques aquáticos.
Análise acústica
- aplicações: tubos e canalizações, condensadores, sistemas de vácuo, ventoinhas, compressores de ar
Já vimos acima que as ondas de som são nossas aliadas. A análise acústica permite detectar problemas na performance técnica dos materiais, localizar a fonte do problema e monitorar a “saúde” do equipamento. Como? Ao detectar diferenças nas frequências de som.
Todas as máquinas em funcionamento fazem barulho, mas a frequência e amplitude mudam quando há vazamentos ou mudanças de pressão, por exemplo. Esta é uma técnica de manutenção preditiva especialmente eficaz em tubagens que transportam líquidos ou gás. Algumas ferramentas mais modernas incorporam termômetros e câmaras para aprofundar a análise à distância.
A manutenção preditiva resolve todos os problemas?
A manutenção preditiva nasceu para evitar danos, mas não podemos viver de ilusões. Falhas aleatórias sempre vão acontecer, especialmente aquelas que são impossíveis de prever ou prevenir. Além disso, não podemos esquecer que a manutenção preditiva exige uma grande infraestrutura. Por isso, a manutenção preditiva só é recomendável para ativos críticos e com modos de falha previsíveis.
Vantagens da manutenção preditiva
- A principal vantagem da manutenção preditiva é agir no tempo adequado, o que diminui o tempo de paradas e aumenta a disponibilidade dos ativos.
- Como a manutenção é programada considerando as necessidades, você evita desperdícios de estoque e mão de obra em manutenção desnecessária.
- Ao reduzir as reparações de emergência e os desperdícios que mencionamos acima, você contribui para controlar melhor o orçamento de manutenção.
- As paradas programadas são planejadas, o que permite agilizar a manutenção e a atividade normal da empresa de forma mais efetiva.
- Boa utilização do equipamento durante todo o ciclo de vida.
⚙️ A manutenção preditiva também é um alicerce da manutenção lean e da produção ‘just-in-time’.
Desvantagens da manutenção preditiva
- A necessidade de investir em equipamentos de monitoramento específicos, assim como em treinamentos para que as equipes saibam usar e interpretar os dados recolhidos.
- Para ativos com pouca criticidade, a manutenção preditiva pode não oferecer uma grande economia em relação às alternativas.
- Não é indicada para ativos com modos de falha aleatórios ou sem dados iniciais para prever danos (nestes casos, é preferível começar por manutenção baseada na condição e ir fazendo a transição).
Vale a pena o investimento em manutenção preditiva?
Já mencionamos que o custo de implementação é alto, mas mesmo assim a manutenção preditiva tem um ROI elevado, que pode chegar a ser 10 vezes o investimento. Um estudo feito pelo Departamento de Energia dos Estados Unidos em 2010, quando a instalação de sensores era ainda mais cara do que agora, aponta para reduções de 25-30% nos custos com manutenção, 35-45% menos paradas e 70-75% menos danos.
Em comparação com a manutenção reativa, gerava economias de 30-40%. Em comparação com a manutenção preventiva, a economia era entre os 8-12%. Segundo a metodologia RCM (reliability-centered maintenance ou manutenção centrada na confiabilidade, o ideal é que 45-55% da manutenção seja preditiva, 25-35% preventiva e apenas 10% reativa ou corretiva.
A Deloitte, em um estudo de 2017, é menos otimista. Ainda assim, a manutenção preditiva é muito promissora. Este estudo sugere que o uptime vai aumentar em 10-20% e os custos com manutenção vão reduzir em 5-10% na Indústria 4.0. O planejamento de manutenção pode demorar menos 20-50% de tempo.
Tendo em conta as vantagens e desvantagens que mencionamos acima, podemos concluir que a manutenção preditiva compensa o investimento para:
- empresas com muitos gastos operacionais e muito capital investido;
- empresas em que o tempo de parada causa um grande prejuízo;
- empresas com ativos no quais os danos são um risco de segurança.
Portanto, não é surpreendente que um setor pioneiro na manutenção preditiva tenha sido a aviação. A previsão de falhas é usada tanto durante o voo – com o monitoramento da temperatura e das vibrações do motor para evitar acidentes – como em terra, para diminuir atrasos e cancelamentos.
Outro dos setores que mais tem aderido à manutenção preditiva é a indústria. É fácil entender o motivo: uma parada na produção pode causar prejuízos enormes. Nos próximos anos, é provável que também ganhe maior expressão na gestão de frotas, na saúde, indústria mineira, na extração e produção de energia.
Como planejar a manutenção preditiva em 4 passos
Se você já decidiu investir em manutenção preditiva na sua empresa, recapitule os 4 passos que precisa para implementá-la:
Identificar ativos críticos.
O primeiro passo é identificar os ativos prioritários para incluir na estratégia de manutenção preditiva. Priorize ativos críticos para as suas operações e ativos com custos elevados de reparação.
Reúna informação sobre o histórico dos ativos e os modos de falha.
O segundo passo é reunir a informação necessária para conseguir transformar os dados que recolhe em ações. Se já tiver um CMMS é mais fácil organizar o histórico e desenvolver os primeiros algoritmos. Ao mesmo tempo, é conveniente estabelecer os modos de falha e a probabilidade de ocorrerem.
Implemente sensores para monitorar a condição.
Agora que já definiu prioridades e modos de falha, você pode começar a implementar os sensores. Nos equipamentos novos costuma ser um processo simples, mas pode ser mais complicado em máquinas mais antigas. Investigue com o fabricante a melhor forma de integrar modelos antigos com novas tecnologias.
Teste e experimente a manutenção preditiva.
Teste o funcionamento dos sensores e a precisão dos algoritmos apenas em algumas máquinas, seguindo um ciclo PDCA. Quando estiver conseguindo programar a manutenção e cumprir os seus objetivos, expanda esta estratégia para outras máquinas!
A manutenção preditiva já é uma estratégia que dá frutos e retorno para muitas empresas. No futuro, à medida que a IoT e a transformação digital se instalam, será ainda mais dominante, acessível e eficaz para prever danos.
Contudo, uma coisa que é clara: a manutenção preditiva se beneficia de sistemas inteligentes e integrados, como os que as Plataformas de Gestão de Manutenção Inteligente proporcionam. Fale com um dos nossos especialistas para entender como a Infraspeak apoia as suas operações, hoje e no futuro!
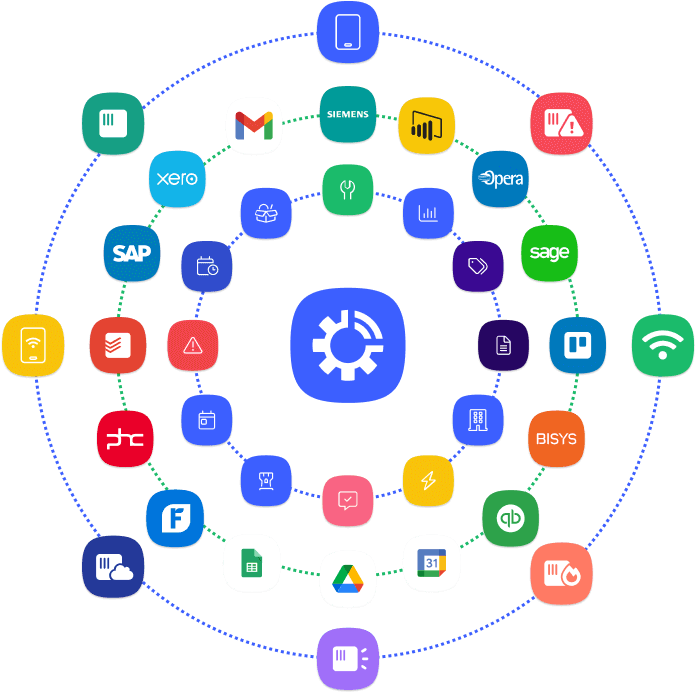