O monitoramento da condição consiste na medição de parâmetros que indicam falhas do equipamento. Idealmente, você vai conseguir detectar alterações nos padrões habituais a tempo de evitar um dano e, assim, poupar na manutenção corretiva e prolongar a vida útil do ativo. Mas, só será possível usufruir destes benefícios se você escolher as técnicas corretas de monitoramento da condição do equipamento e da operação.
A manutenção com base na condição muitas vezes coincide, como é normal, com manutenção preditiva. O acompanhamento do comportamento dos ativos é uma grande parte da manutenção preditiva — os dados recolhidos fornecem a base para encontrar tendências e aperfeiçoar algoritmos. Faz sentido, contudo, falar de monitoramento da condição em tempo real, mesmo sem um programa de manutenção preditiva.
Monitoramento da condição, IIOT e confiabilidade
Quando se fala em manutenção preditiva, duas das maiores barreiras são o investimento que esse método exige e a dificuldade em desenvolver algoritmos. Mas a Internet das Coisas (IoT) e a Internet Industrial das Coisas (IIoT) trouxeram uma grande mudança para a indústria. Os sensores e dispositivos de monitoramento da condição estão agora ligados a plataformas de manutenção, fornecendo dados em tempo real.
Esta nova conectividade é simultaneamente mais acessível e mais fácil de implementar do que a manutenção preditiva. Os dados em tempo real permitem aos gestores ajustar os planos de manutenção preventiva, ao mesmo tempo que proporcionam maior confiabilidade. A AI ainda processa estes dados para reconhecer padrões, o que é um dos avanços mais promissores para a “confiabilidade digital”.
Dessa forma, independentemente da capacidade de implementar imediatamente um plano de manutenção preditiva, o monitoramento da condição apresente, por si só, benefícios.
Vantagens em monitorar a condição:
✓ Evita grandes danos e reduz o downtime.
✓ Permite melhor gestão de ativos durante toda a sua vida útil.
✓ Diminui os custos, especialmente com a manutenção de emergência.
✓ Fornece a base para desenvolver algoritmos preditivos no futuro.
9 tipos de manutenção com base na condição que você precisa conhecer
A manutenção com base na condição começa com inspeções simples. Pequenas alterações, como calor ou pressão anormais, sons estranhos, vibração excessiva ou cheiro diferente, são frequentemente sinais de que alguma coisa está prestes a estragar. No entanto, as técnicas de monitoramento da condição variam desde as inspeções mais simples até à tecnologia mais avançada. Estes são 9 tipos de monitoramento da condição que tem de conhecer:
Análise do óleo
A análise do óleo se aplica a óleos de máquinas, lubrificantes e fluidos. Pode detectar desgaste, superaquecimento e contaminação. Níveis elevados de ferro, por exemplo, indicam normalmente a presença de poeiras e areias. Se detectados a tempo, as falhas das caixas de velocidades podem ser reduzidas em 50%. Ao evitar a contaminação, a falha de rolamentos também diminui em 75%. Um estudo canadense sugeriu que o retorno sobre o investimento na análise do óleo é de 20:1.
Se quiser evitar estes danos, há vários métodos de análise de óleo disponíveis: ferrografia, testes de presença de água, testes de viscosidade, ICP/espetroscopia, teste de resistência dielétrica, análise microbiana, teor de ferro (índice de quantificação de partículas), espetroscopia infravermelha, espetroscopia ultravioleta, titulação potenciométrica (número total de ácidos/número total de bases) e testes de sedimentos. Esquecemos de algum tipo?
Análise de vibração
A análise de vibrações é um dos métodos mais populares de manutenção preditiva. Ela pode detectar desalinhamentos, desequilíbrios e desgastes cerca de 3 meses antes de causarem um dano. É também uma oportunidade para melhorar o consumo de energia, já que bombas de água desalinhadas, por exemplo, gastam até 15% mais energia. A medição de vibrações é também muito destacada na norma ISO 22096.
As técnicas de monitoramento da condição de análise de vibrações incluem análise de pulsos de choque (por exemplo, para equipamento rotativo), análise rápida de fourier, análise de vibração em banda larga (por exemplo, para detectar desgaste dos rolamentos), análise por ultrassom (por exemplo, para detectar vazamentos), densidade espectral de potência, análise da forma de ondas no tempo (por exemplo, para máquinas com sondas X-Y) e espectrograma.
Análise de circuitos de motores
A análise de circuitos de motores, também conhecida como teste MCA, avalia o estado dos motores elétricos. Pode ser utilizada para analisar o estado do motor (incluindo rotores, problemas de acoplamento/correia, qualidade da potência), desequilíbrios elétricos e isolamento. Mais do que prevenir falhas, o MCA pode ser utilizado para reduzir os custos energéticos e melhorar a eficiência do equipamento em 10-15%.
Termografia
A termografia estuda os padrões de calor e radiação em máquinas. A análise dos dados faz o resto, detetando padrões que indicam falhas ou degradação. Tem uma ampla gama de aplicações, incluindo a detecção de desalinhamentos, desequilíbrios, lubrificação inadequada, desgaste e tensão em peças mecânicas. No equipamento elétrico, identifica sobreaquecimento, vazamentos na tubulação e fragilidades nos reservatórios de pressão.
A termografia infravermelha, em particular, se tornou um método popular para manutenção preditiva e ensaios não destrutivos. Um estudo de 2013 concluiu que a termografia infravermelha foi extremamente eficaz na melhoria da segurança, reduzindo os “pontos perigosos” – e as potenciais causas de falhas – em 90%. Globalmente, a termografia reduz o risco, previne falhas, diminui os custos e as perdas.
Monitoramento por ultrassons
Já citamos a análise por ultrassom há pouco (não viu? Leia “análise de vibração” novamente), mas ela merece o seu próprio lugar nesta lista. Este tipo de monitoramento utiliza ondas sonoras de alta frequência para detectar vazamentos e mudanças de pressão, o que pode reduzir as inspeções em 30%.
O monitoramento por ultrassons é especialmente econômico quando é feito em conjunto com a análise de vibrações (alguns sensores captam ambas as coisas) e a termografia por infravermelhos. Os ultrassons aéreos e estruturais estão se tornando uma boa opção para detectar ‘ondas de tensão’ em máquinas rotativas. Outros métodos incluem a técnica de retrodifusão e a atenuação de eco da parede de fundo.
Radiografia
Assim como a termografia, a radiografia (incluindo a análise de radiação e a radiografia de neutrões) é um método muito exaustivo de ensaio não destrutivo. As imagens permitem aos técnicos inspecionar defeitos internos, como corrosão em peças próximas e falhas na solda. Contudo, a principal vantagem é que pode ser utilizada em todos os tipos de materiais, desde que os técnicos se protejam.
Interferometria laser
Os interferômetros laser medem alterações para calcular deslocamentos com base em comprimentos de onda gerados por laser. São utilizados no monitoramento da condição para identificar defeitos na superfície e subsuperfície como corrosão e cavidades. A interferometria inclui cisalhamento laser, ultrassons laser, mapeamento de deformação, interferometria eletrônica de padrão de mancha e holografia digital.
Monitoramento elétrico
Pouco mais de 53% de todos os incêndios domésticos acidentais no Reino Unido têm origem elétrica. Do mesmo modo, a eletricidade é uma das maiores razões por trás dos ferimentos e fatalidades no trabalho. A prevenção de falhas elétricas com um controle rigoroso não só evita danos como também melhora a segurança. Isto inclui testes para avaliar a resistência, indução, capacidade elétrica, resposta de pulso, resposta de frequência e degradação.
As técnicas de monitoramento da condição elétrica incluem testes de megohmímetro, testes de elevado potencial ou de resistência dielétrica (por exemplo, para determinar se o isolamento está em boas condições), análise de assinatura energética (para testar corrente e tensão), testes de impedância de bateria, testes de sobretensão e hipotensão (também para detectar falhas de isolamento) e, até certo ponto, também análise de circuitos de motor.
Medição Eletromagnética
A medição eletromagnética não deve ser confundida com o monitoramento elétrico. O monitoramento eletromagnético mede distorções do campo magnético para detectar fissuras, achatamentos, corrosão, fragilidades e outros defeitos (por exemplo, desgaste). Talvez, o método mais recorrente de monitoramento do estado eletromagnético seja o ensaio por correntes parasitas (ECT), que é utilizado na indústria petroquímica para detectar fissuras estreitas.
Além do ECT, existem outras técnicas, como correntes de Foucault pulsantes, correntes de Foucault à distância e próximas do campo, testes de correntes de Foucault saturadas de baixa frequência, matriz de correntes de Foucault, inspeção de partículas magnéticas, vazamentos de fluxo magnético e memória magnética metálica. Estas técnicas são especialmente adequadas para materiais condutores não ferrosos, como tubos, condensadores, caldeiras e superfícies de aeronaves.
Conclusão
Existem dezenas de técnicas de monitoramento da condição. Algumas são mais caras do que outras, mas não encontramos nenhuma que não ofereça uma boa relação qualidade/preço. Se escolher os métodos adequados ao equipamento, os integrar na plataforma de manutenção e analisar os dados, terá mais eficiência com a manutenção corretiva.
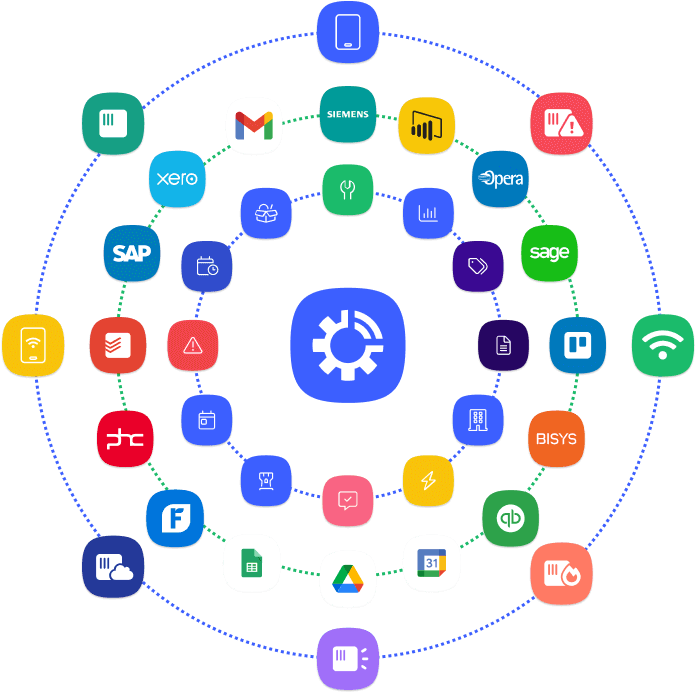