How long does an HVAC appliance last? With proper maintenance, more than 15 years. However, the benefits are not just about extending the life and ROI of your equipment. The advantages add up:
- avoid costly breakdowns, which can decrease by up to 95%;
- reduce energy costs and decrease the company’s environmental footprint;
- improve indoor air quality and maintain optimum and stable conditions;
- prevent diseases such as Legionella, asthma, or allergic rhinitis.
But if there are no doubts about the advantages, the same cannot be said about how to plan HVAC preventive maintenance. How can you be sure that you won’t miss any AC units? Or schedule routine maintenance with a reduced team? Is there any way to manage this giant – the HVAC system – without hyperventilating?
How to make an HVAC preventive maintenance plan
Relax: you can breathe now, because we will explain how to make a maintenance plan for HVAC in just 4 steps:
1. Inventory
Like a recipe, our guide to making a maintenance plan starts with the two ingredients: “inventory” and “maintenance software”. The first thing – and the ingredient you really can’t replace in this recipe – is asset inventory.
Create a comprehensive inventory of all your HVAC equipment. The inventory should include location, equipment status, supplier, and even supplementary information such as asset history, manufacturer recommendations, and proof of warranty.
How you create and organise this inventory is up to you. It can even be on paper or Excel! But we recommend doing it in a maintenance software to centralise all the information. While the most common is a CMMS, explore other options, including intelligent maintenance management platforms.
2. Checklists for each asset
Now that the inventory is ready, you begin to realise the magnitude of the task. Associate work orders (WOs) to each asset type – if you use a smart maintenance platform, you can link a group of assets (“all AC units”) to the same WO (“change filters”).
👉 See how Sotécnica reduced administrative work by 87% with Infraspeak.
Generally, there is an annual HVAC maintenance, which includes a complete inspection, a deep cleaning, and retightening the electrical connections. Then there is recurring maintenance that, depending on the piece of equipment, can be monthly, quarterly, or weekly, such as changing filters, adding lubricant and coolant, among others.
With a software, you also don’t need to create a WO for each of these routine actions. In Infraspeak, for example, define “planned tasks” for annual tasks and “cyclical tasks” to automatically schedule routine tasks. This way, nothing gets forgotten!
3. Schedule and assign all tasks
We have already explained the advantages of using maintenance software to schedule HVAC preventive maintenance. But to schedule all tasks, there’s still one more thing you need to do: the maintenance schedule. This is what will guide your daily operations.
Start by making a realistic prediction of how long each task will take. Then, take into account that technicians are only productive 25-35% of the time. Based on that forecast, make sure you’re not scheduling too many tasks for a single day, creating a never-ending backlog.
Finally, don’t forget to pick the best time to do all your annual inspections. If you own a hotel, for example, it’s a good idea to take advantage of the low season to avoid disturbing guests and have everything ready for the peak season. But each case is unique!
4. Analyse KPIs and keep improving
Once you have the entire HVAC maintenance plan set up in the software, it’s a great policy to analyse the KPIs. Many programs generate automatic reports to calculate downtime percentage, mean time between failures, and mean time to repair.
👉 Review the key maintenance indicators here
Based on these indicators, you can better control maintenance costs, equipment reliability, the efficiency of your plan, and team productivity. From here, you can improve the plan’s “weak points”, track the life cycle of assets, and make more informed decisions.
For example, if a device is constantly breaking down and draining your resources, you should consider whether it is preferable to continue repairing or to replace it. Keep an eye out for frequent breakdowns, difficulty maintaining the set temperature, increased energy expenditure, and excessive corrosion or wear and tear.
Like almost everything else, preventative maintenance gets easier with the help of technology. Whether you’re a service provider or looking for a system to manage your building maintenance, a custom platform will save you time, paperwork, and many hours of planning.
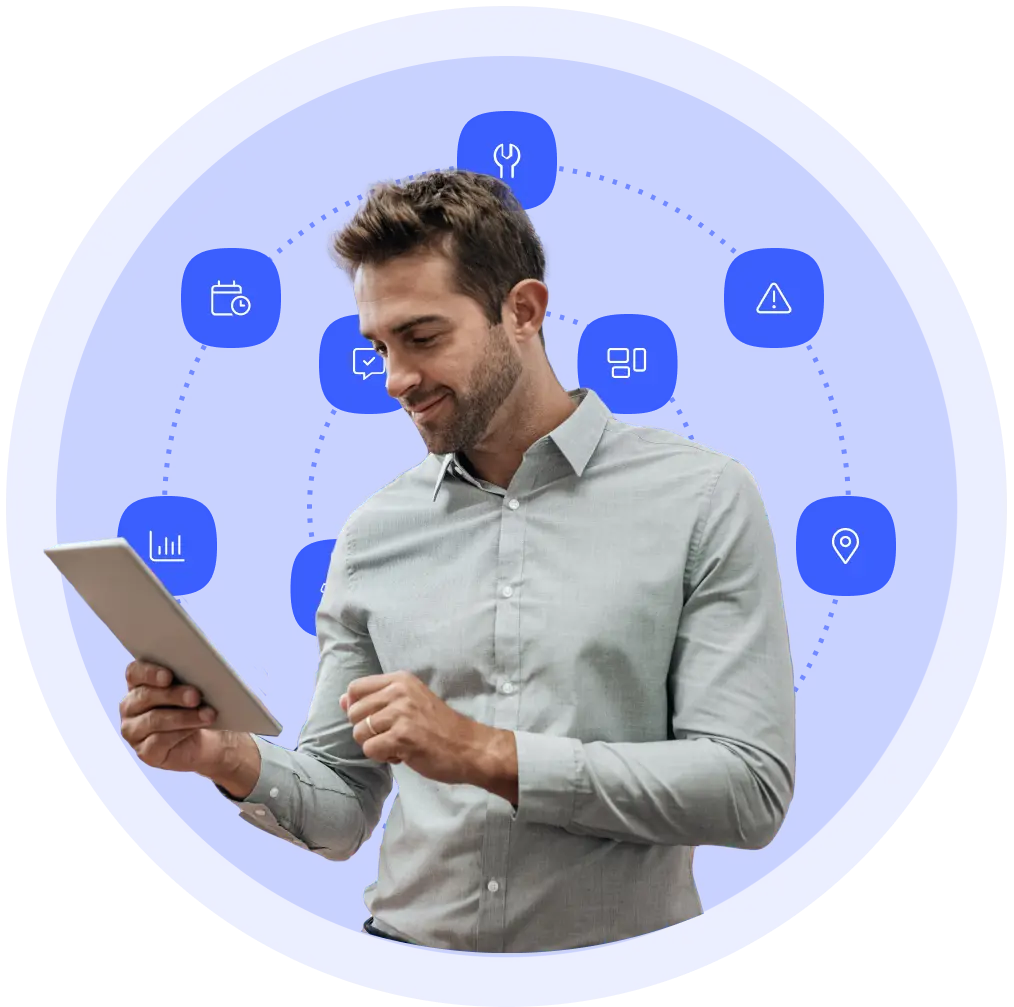