What is compliance in preventive maintenance?
Preventive maintenance is not always the best maintenance strategy. But if you don’t have condition monitoring devices at your disposal or can’t develop predictive maintenance algorithms, it is the safest strategy. The big problem is that it often ends up with endless lists of preventive tasks that you can rarely fulfil.
Adherence to the preventive maintenance plan is also known as compliance. In the same sense, a failure to adhere to the plan is known as “non-compliance”. When it comes to performance indicators (KPI), we assess compliance in preventive maintenance through the preventive maintenance compliance rate.
How to calculate preventive maintenance compliance / preventive maintenance compliance rate?
The preventive maintenance compliance rate is the percentage of preventive maintenance carried out within the expected time. Therefore, simply calculate the ratio between tasks performed and planned tasks and multiply by 100. The formula to calculate the preventive maintenance compliance (PMC) is as follows:
For example, if you had planned 200 maintenance tasks and only executed 178, you can calculate the preventive maintenance plan compliance like this:
But beware! In preventive maintenance, there is a 10% rule. A task must be completed within a margin of 10% of the stipulated date. For example, if you have a task scheduled every 30 days, then you must complete it three days earlier (on day 27 of the cycle) or 3 days later (on day 33). So, if you completed the task on day 33, you are still ‘on schedule’. However, you should not abuse this rule!
If you use this exception in one month to stay on schedule, it is very important that you “catch up” the next month and meet the deadline. Think of the 10% rule as emergency contraception that you can only use when there is a serious unforeseen event, and not constantly! Imagine: if you do this every month, at the end of the year you will only do the periodic maintenance 11 times (not 12).
The 10% rule didn’t come out of nowhere.
We know that even at peak performance “only” 90% of maintenance tasks are preventive. The remaining 10% is reactive maintenance due to failures that can’t be predicted. So these guidelines ensure that your team has room for manoeuvre in the event of any unexpected failures.
👉 You should aim for an 80/20 ratio — 80% preventive maintenance, 20% reactive maintenance.
The 4 steps to calculate the preventive maintenance compliance score
- Defining a preventive maintenance plan and a list of tasks to be performed on each asset;
- Executing the preventive maintenance plan in your previously established time period;
- Monitoring the number of tasks completed on time;
- Calculating the percentage of maintenance work orders completed within schedule.
How to increase compliance in preventive maintenance?
Organise all tasks
Do you still use paper to organise your maintenance plans? Do you keep scrolling through Excel spreadsheets to find the tasks you’re looking for? Do you not know how many tasks have been completed on time? Then start by organising all your tasks on a maintenance management platform. By creating a digital record, it’s much easier to organise what you’re looking for and monitor compliance.
Eliminate unnecessary tasks
Did you know that 30% of preventive maintenance is performed too frequently? Now that you have organised your tasks, it is easier to see if you have duplicate tasks, over-frequent tasks, or tasks that do not correspond to any failure mode. As you eliminate tasks, you increase technician productivity and even reduce maintenance costs.
Analyse your backlog
We’ve reached a crucial point. Once you’ve logged all the information into a maintenance management platform, you’ll be making data-driven decisions. Look at your backlog and make a careful analysis. The first question you need to ask is “which tasks are taking longer than expected?” And the second question you should ask is “why?“.
Perhaps you are underestimating how long certain tasks take. But there may also be other operational obstacles that you’re not considering. We recommend you perform a root cause analysis to find out the real reason for the delays. This way, you correct the problem and avoid non-conformities in the future.
Possible causes for recurring non-compliances:
- difficulty in estimating the time each task requires (you should review the workload annually, depending on the state of the asset);
- poor scheduling of tasks, which does not optimise travel (something that can also be improved with intelligent maintenance software);
- poor MRO inventory management and resource management (see here how good MRO management reduces maintenance costs);
- gaps in technicians’ training or skillset, which you should correct through continuous training;
- the company does not see maintenance as a priority and adopts a strategy based on reactive maintenance, which “absorbs” all resources.
Automate workflows
When your tasks are written down in a table that you post on the corkboard or in an Excel that looks like the Wild West… it’s normal for technicians to forget! At the end of the month, it’s not surprising that several tasks have fallen behind. That’s why workflow automation is extremely useful to increase the preventive maintenance compliance rate.
With an intelligent maintenance management platform, you schedule tasks and, when the time comes, technicians receive a notification. It is also possible for the platform to automatically assign tasks to the most appropriate technician, which makes planning even easier. Plus, if you choose intuitive software, it’s easy to gather valuable intelligence to continue improving in the future.
Change strategy
And finally… change your strategy! If you have already eliminated all duplicate tasks and optimised all workflows, and it’s still not enough, you need to better allocate your resources. You can adopt a risk-based maintenance strategy, for example. While not ideal, it ensures the safety of the facility with the limited resources you have.
Again, the intelligence you collect on the platform is essential to assess the criticality of assets and define your priorities. Then, track all indicators over time, namely the preventive maintenance compliance rate, mean time between failures (MTBF), and mean time to repair (MTTR).
As you’ve seen, automation and intelligent maintenance make maintenance compliance easier. If you need help modernising your operations or implementing an intelligent maintenance solution, talk to one of our experts!
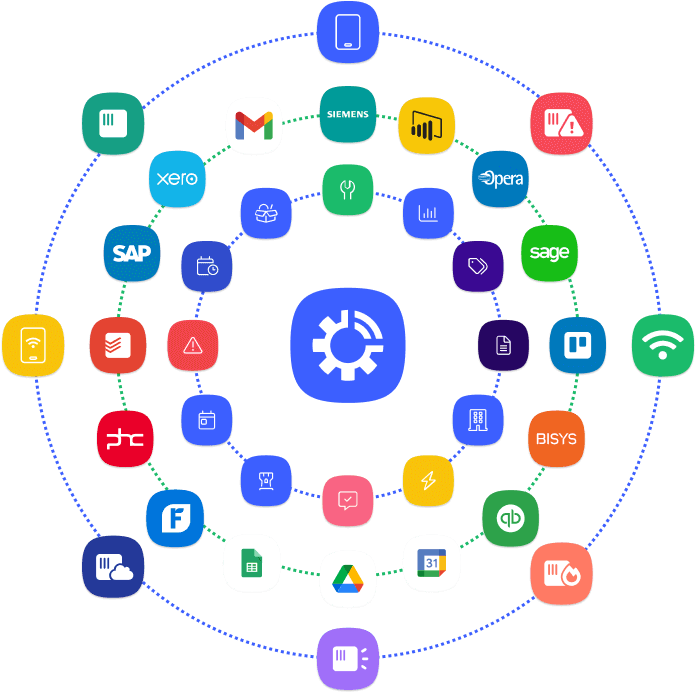