Having software dedicated to maintenance is a turning point in asset management for any company of any type or size.
The strategy of any company (that is, if it’s well-managed) aims at economic and financial results, business continuity, brand expansion, respect for standards and legislation, respect for the safety of workers and users of its products and services, and sustainability.
What is asset maintenance software?
No one buys a software subscription for the sake of having it. If we have used a management tool, it’s because we have some business requirements to meet.
In the best companies in the industry, asset management is a very serious thing and is developed to support operations and/or production, enabling the achievement of the organisation’s long-term goals.
An asset maintenance software is, therefore, essential to support the company’s business strategy. Its purpose is to manage and optimise the maintenance and performance of a company’s assets, that can include equipment, machinery, vehicles, facilities, or any other physical assets that are critical to the operations.
What types of asset management software are available?
You can implement Enterprise Asset Management (EAM) software on-site via local servers or remotely via the cloud. Both approaches have their pros and cons, but cloud-based platforms are generally considered the superior of the two:
SAAS/Cloud EAM
- Easy and cheap to startup
- No maintenance or updates required
- Data secure
- Highly customisable
- Ongoing expense
- Downtime issues
Cloud-based EAM software is offered on a subscription model, which you access through a website or mobile app. Subscription plans are typically offered on a monthly or yearly basis.
As everything’s hosted in the cloud, there’s no need to install software onto your computer or company servers. Instead, EAM platforms will host everything on their end, including storing your data securely in accordance with GDPR regulations.
This makes it a lot easier and cheaper to implement an EAM system. There are no startup costs, as everything’s ready to go. You also don’t need to worry about maintenance or updates, as this is all handled on the platform’s servers, not your own. Having everything on secure servers also means your data is safe.
Local EAM
- Customisable
- In-house support
- In control of data
- Complicated startup and integration
- Can be expensive to maintain
- Hard to scale
- Often lacks mobile features
Having an EAM installed locally on your organisation’s servers is another option. This involves purchasing EAM software, typically with a one-off fee. This gives you more control over the implementation of your EAM and how your data is stored, which be an important consideration for some information-sensitive companies that don’t want third parties handling their data.
On-premise EAMs, however, are much harder to set up and install. Implementation will require IT specialists, and unforeseen issues are not unusual. Because of this, local EAMs can be more difficult to scale or relocate if necessary. Having things installed locally also means you’re usually missing out on some mobile features that can keep remote asset data up to date.
IMMP
- Highly customisable
- Highly scalable
- AI-based predictive maintenance
- IoT enabled
- Maintenance 5.0 ready
A third (and most advanced) option is an Intelligent Maintenance Management Platform (IMMP). This option resembles cloud-based solutions but is designed from the ground up to be human-centric and use technology to meet the needs of asset managers.
Infraspeak’s IMMP solution achieves this by offering a highly customisable EAM interface. You can easily access third-party integrations and switch features on or off as required, making it highly scalable. Your organisation can even make use of IoT devices which can update asset data live.
AI is also utilised to accurately predict when assets require maintenance. Using complex algorithms, IMMPs learn from asset data and discover inefficiencies that may otherwise go unnoticed. Asset managers are then alerted via a human-first interface.
Best asset management software in 2024
- Infraspeak
- eMaint CMMS
- Valuekeep
- monday.com
- MaintainX
- Maintainly
- EZOfficeInventory
- Wrike
- Asset Panda
- UpKeep
The reviews below are sourced from Capterra.com.
Infraspeak
Infraspeak is a solution that assists maintenance managers and teams in efficiently planning and optimising maintenance activities, streamlining asset and inventory management, and ensuring regulatory compliance. It goes way beyond basic functionalities by providing intelligent insights that significantly impact your operations.
With our Intelligent Maintenance Management Platform, you can achieve remarkable results, such as reducing Mean Time to Repair (MTTR) by up to 83%, cutting unpredictable costs by up to 3.2 times, and boosting your Service Level Agreement (SLA) completion rate by up to 91%. Additionally, Infraspeak’s innovative features enable you to save valuable time by automating over 60% of your administrative tasks.
Using Infraspeak’s Enterprise Asset Management software, you can:
- create case-by-case preventive maintenance plans based on the actual utilisation of your assets
- plan recurring tasks, assign sets of tasks to specific planned jobs and automate task assignments
- access real-time KPIs and customisable reports for your maintenance operations
- connect to a world of 100+ integrations, including IoT sensors and Building Management Systems (BMS)
- automatically identify spikes and variations in utility spending to reduce costs, optimise energy consumption and make your operations more sustainable
- improve decision-making through intelligence & insights
An IMMP adds predictability to your preventive maintenance through optimal asset management. Stay ahead, protect your assets and avoid unplanned downtime.
What users love about Infraspeak
“Operators can now relax and look at the dashboard — everything is working more smoothly and transparently.” — Andrew Voisey, Maintenance Manager at Primark
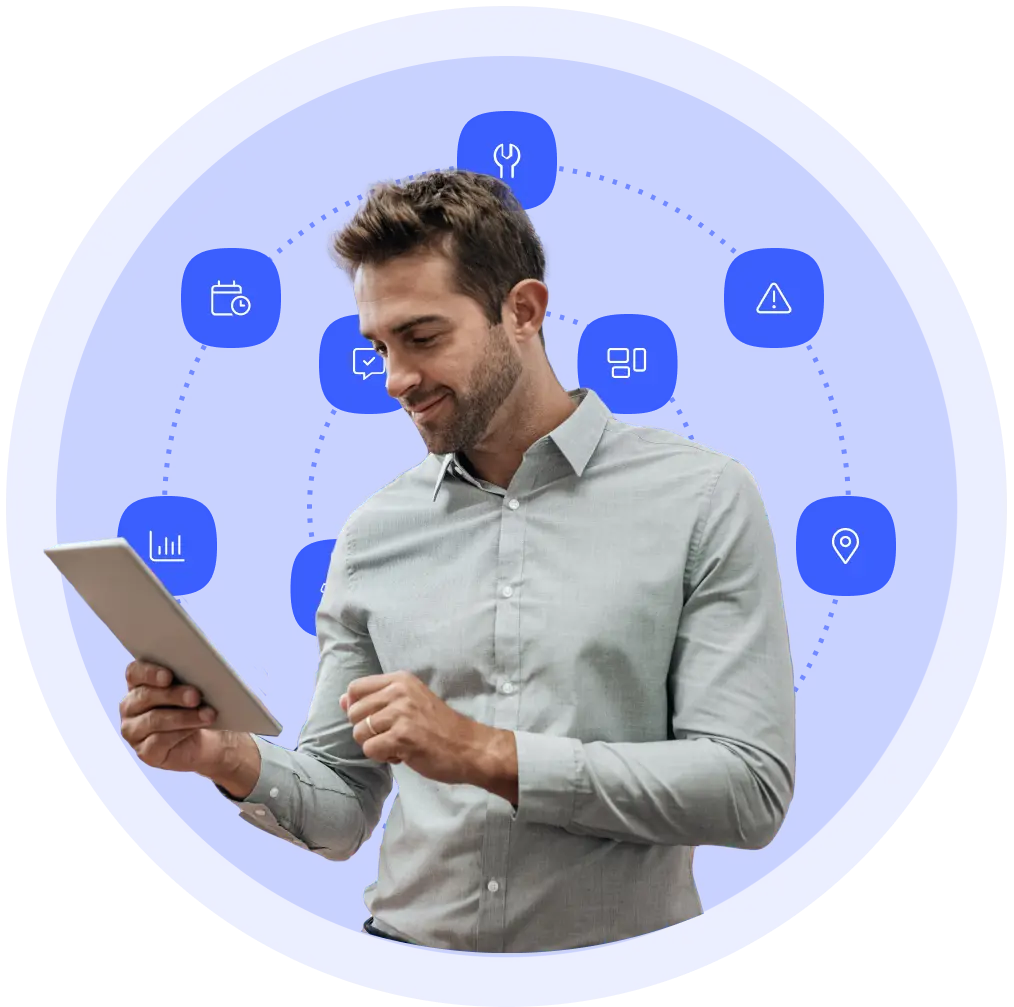
eMaint CMMS
eMaint enables you to optimise workflows, automate preventive maintenance tasks, and ensure the availability of spare parts for upcoming work orders. It offers quick generation of regulatory compliance reports and provides a comprehensive view of work order status.
Valuekeep
Valuekeep focuses on optimising maintenance management, improving asset tracking, and increasing the return on assets.
monday.com
A customisable work and project management platform that helps enterprises organise all their assets effectively. It provides features such as visual boards for team collaboration, and informative dashboards for tracking progress and results.
MaintainX
A platform that combines user-friendly mobile app, cloud technology, real-time analytics, and open APIs to enhance productivity and efficiency.
Maintainly
Maintainly offers maintenance management with asset tracking, inventory management, reporting, and mobile apps.
EZOfficeInventory
A solution that offers an intuitive interface with features designed for all asset management needs, including reservations, maintenance, checkouts, audits, and scanning functionality.
Wrike
Wrike is a work management platform that includes dashboards, Gantt charts, and time tracking features to help manage enterprise assets effectively.
Asset Panda
A cloud-based asset tracking platform with mobile apps for iOS and Android. It offers comprehensive asset tracking functionality.
UpKeep
Upkeep provides EAM and CMMS software for streamlined work orders, facility management, and asset management.
26 reasons to have a good asset management software
The list of reasons to have a good software in asset management and asset maintenance is relatively long, as are the needs and the scope of whoever is in charge of the department:
Reduction of Asset-Related Costs
1. Reduce operating and maintenance costs of assets through appropriate care and use of tools such as root cause analysis.
2. Extend the lifespan of assets, thus avoiding expenses with frequent replacements.
3. Reduce the working capital employed in stock by ensuring that adequate storage principles are followed and by reviewing the policies linked to the stock of spare parts.
Reduction of Asset-Related Risk
4. Reduce risks associated with legal demands for safety, environmental protection, health, HACCP — Hazard Analysis and Critical Control Points — and quality.
Improvement of Asset Performance
5. Implementation and application of best practices and improvement actions related to KPIs.
Planned Maintenance and Services
6. Implementation of planning and scheduling of activities, whether reactive, preventive, predictive or improvement maintenance.
7. Downtime management.
Maintenance Master Plan
8. Enable the constant updating of the definition of Asset Criticality, classifying equipment for maintenance practices purposes.
9. Construction and constant revision of the database of work instructions and existing maintenance plans.
10. Development and control of inspection tasks (checklists) applicable to all kinds of equipment and infrastructures.
11. Creation and execution of the annual 52-week Maintenance Master Plan with 5-year Multi-year coverage, in some cases, for critical equipment.
Logistics and Strategic Supplies
12. Qualitative and quantitative selection of critical materials and parts.
13. Stock management of critical spare parts and materials in constant use.
14. Development and monitoring of suppliers and strategic services;
15. Management of material purchases, services, and long-term contracts.
16. Contract management.
Documentation Management
17. Storing information through document management.
18. Updating of schematics regarding modifications, expansions, and disposals of equipment and installations.
19. Provision of a library of procedures and operational flows.
Reliability Engineering
20. Implementation of a methodology to increase Reliability and Maintainability of equipment, facilities and new projects.
21. Commissioning Operations of new facilities.
22. Support to management programs such as Total Productive Maintenance, 5S, and Failure Analysis.
23. Lifecycle Cost (LCC) Management.
Work Safety
24. Constant updating and application of existing legislation.
25. Building, constant revision and use of the Labour Safety Instructions database and contingency plans;
General Management Indicators Dashboard
26. Gathering information, controlling data and having the main Management Indicators such as Costs, Availability, Reliability, Failure Rate, Maintenance Plan Compliance, etc., displayed to you in a single place.
- Improved efficiency in facility management.
- Better visibility into asset and team performance.
- More informed and data-driven decision making.
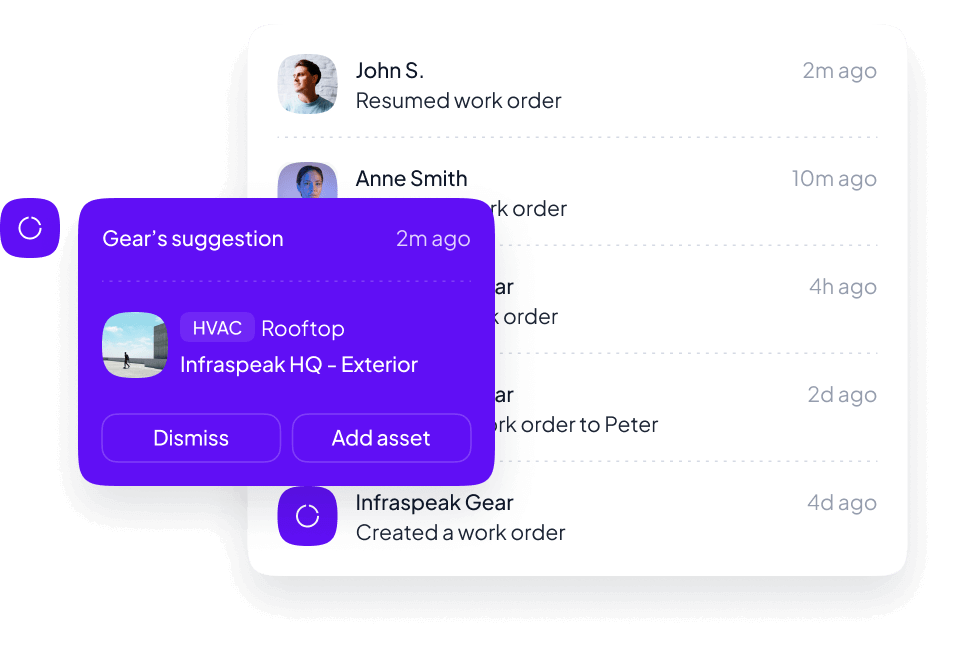