La maintenance corrective est l’activité technique réalisée après qu’une défaillance s’est produite. Son objectif est de restaurer un actif à un état dans lequel il peut accomplir sa fonction prévue, soit en le réparant, soit en le remplaçant.
Cela ne signifie pas que la maintenance corrective doit être utilisée seule. Elle peut être intégrée dans une stratégie plus large pour planifier votre maintenance.
À quoi sert la maintenance corrective ?
Si la maintenance corrective est utilisée seule, elle est souvent surnommée maintenance « à l’échec ». Aucune action préventive n’est réalisée sur un équipement qui est délibérément laissé en fonctionnement jusqu’à ce qu’il tombe en panne. Ce n’est qu’après coup qu’il est réparé ou remplacé.
Cette approche « jusqu’à l’usure » est en fait idéale pour les équipements de faible priorité, sans lesquels les opérations de l’entreprise peuvent continuer à fonctionner normalement. C’est également une approche viable pour les actifs de moindre valeur, où une surveillance ou une maintenance régulière peut finalement s’avérer plus coûteuse que les réparations ou les substitutions en cas de dysfonctionnement.
Cependant, lorsqu’elle est appliquée à des équipements de haute priorité, elle peut éventuellement entraîner des temps d’arrêt, car les opérations normales devront être interrompues pendant que les techniciens travaillent. Elle peut également entraîner des coûts très élevés à long terme si elle est appliquée à des actifs de grande valeur.
Maintenance d’urgence
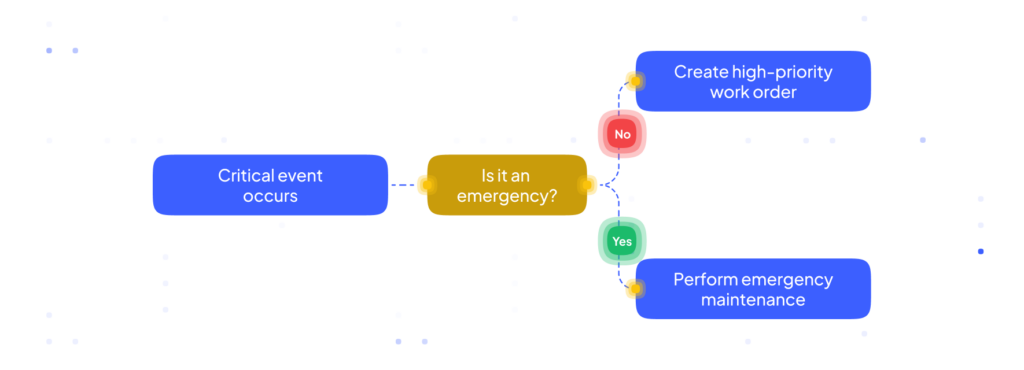
La maintenance d’urgence fait référence aux actions immédiates prises pour restaurer la capacité opérationnelle d’un actif. Elle est souvent déclenchée par des exigences de sécurité urgentes ou la nécessité de prévenir des arrêts prolongés et des pertes potentielles. Des facteurs tels que la disponibilité des pièces de rechange et l’ampleur des réparations peuvent influencer l’exécution de la maintenance d’urgence.
La maintenance d’urgence est généralement plus coûteuse que la maintenance corrective en raison de l’urgence, qui nécessite souvent la sous-traitance de services de maintenance et le paiement de frais supplémentaires pour la livraison rapide des pièces de rechange.
Exemples de maintenance corrective
Imaginez une installation de fabrication où une machine critique tombe soudainement en panne, entraînant un arrêt complet de la production. Face à cette situation d’urgence, l’équipe de maintenance est immédiatement appelée pour résoudre le problème. Elle diagnostique rapidement la panne, procure les pièces de rechange nécessaires en urgence et travaille avec diligence pour rétablir le fonctionnement de la machine le plus rapidement possible. Cette maintenance d’urgence est essentielle pour minimiser les temps d’arrêt, prévenir les pertes financières et assurer la continuité de la production.
Voici un autre exemple : un bâtiment commercial où le système de climatisation commence à montrer des signes d’efficacité de refroidissement réduite. Bien que le système ne soit pas encore totalement en panne, l’équipe de maintenance reconnaît les signes avant-coureurs et prend des mesures correctives. Elle planifie une session de maintenance pour nettoyer le système, remplacer les composants usés et optimiser ses performances.
En abordant de manière proactive le problème avant qu’il ne s’aggrave, l’équipe de maintenance effectue efficacement une maintenance corrective pour prévenir une panne potentielle et maintenir une fonctionnalité optimale.
Maintenance corrective vs. maintenance proactive
Même avec des plans de maintenance préventive ou prédictive complets en place, la maintenance corrective peut (et doit) être utilisée.
Aussi utiles que puissent être ces plans dans certaines circonstances, ces stratégies de maintenance proactive ne sont pas efficaces à 100 %. Il y aura toujours des pannes inattendues, bien que moins nombreuses, avec la maintenance préventive ou prédictive. Des mesures correctives devront souvent être prises pour réparer les pannes imprévues, et il est donc très utile de former votre équipe à les comprendre.
En général, les experts suggèrent d’observer la règle des 80/20. Cela signifie que seulement 20 % de la maintenance doit constituer des actions correctives, tandis que les 80 % restants doivent être consacrés à la maintenance proactive. En réalité, les équipes passent entre 34 % et 45 % de leur temps à effectuer de la maintenance corrective.
Voici un exemple de flux de travail de maintenance planifiée :
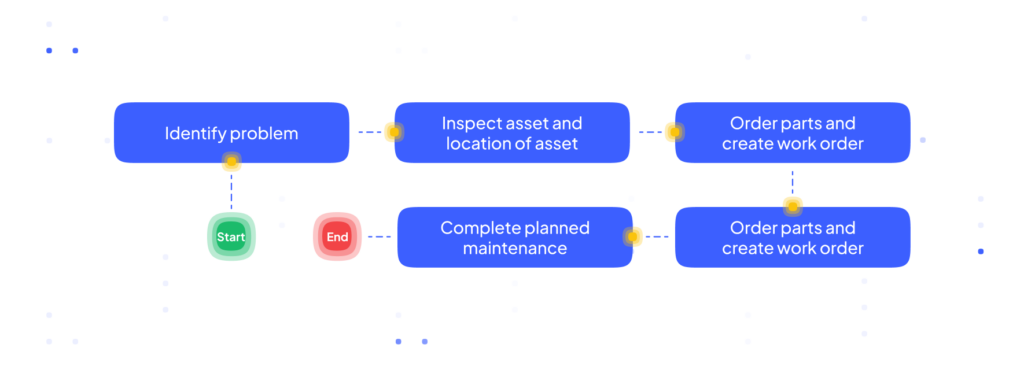
📌 Avantages de la maintenance corrective
De nombreux professionnels ne considèrent pas les avantages de la maintenance corrective, mais il est important de reconnaître que dans certains cas, elle est non seulement conseillée, mais en fait importante.
Dans le cas où un actif de faible importance devient défectueux, les coûts impliqués pour simplement le « réparer » seront considérablement inférieurs à ceux d’une enquête complète en utilisant une méthodologie préventive. Pour les équipements qui ne sont pas cruciaux pour le fonctionnement de vos opérations, une approche plus directe et corrective peut être meilleure. Voyons cela :
- Coûts à court terme réduits : En raison de sa nature corrective, il y a très peu de coûts administratifs ou financiers jusqu’à ce que quelque chose tourne mal. Si tout reste fonctionnel, vous ne payez rien !
- Planification minimale requise : La maintenance corrective consiste en des actions très ciblées sur des composants spécifiques d’installations ou de dispositifs défectueux. Elle nécessite une planification complexe très limitée.
- Processus simplifié : Le processus est facile à comprendre, car il suffit d’intervenir lorsqu’un problème survient.
- Meilleure solution dans certains cas : Il y aura des moments où le temps et l’argent investis dans la planification et la stratégie de maintenance préventive seront bien plus élevés que les simples coûts de « réparation » de la maintenance corrective.
📌 Inconvénients de la maintenance corrective
- Imprévisibilité : Compter sur la maintenance corrective peut être problématique si l’équipement n’est pas surveillé après son achat, ce qui entraîne davantage de pannes très imprévisibles dont la cause est inconnue.
- Opérations interrompues : Les pannes inattendues peuvent être ralenties par l’impossibilité d’accéder aux matériaux, ce qui peut entraîner des périodes d’inactivité prolongées.
- Équipement non maximisé : Cette approche ne protège pas ou ne prend pas soin de l’équipement, réduisant ainsi la durée de vie des actifs. Elle ne fait que réparer l’actif à court terme.
- Coûts à long terme plus élevés : La maintenance corrective est appliquée lorsqu’il est estimé que les coûts d’arrêt et de réparation en cas de défaillance seront inférieurs à l’investissement nécessaire pour une maintenance planifiée. Mais cela ne se produit pas toujours. Lorsqu’une défaillance plus grave survient, elle peut être extrêmement coûteuse et lente à réparer. Les longues périodes d’inactivité ont des effets négatifs sur la réputation, la satisfaction des clients, la sécurité et la capacité à gérer une entreprise de manière efficace et productive.
Comment réduire votre charge de maintenance corrective
Comme nous l’avons vu, la maintenance corrective est un choix tout à fait approprié dans certains scénarios. Cependant, chaque fois que possible, vous voudrez planifier vos interventions à l’avance (rappelez-vous la règle des 80/20).
Pour réduire la quantité de maintenance corrective que vous effectuez, vous pourriez essayer de…
Fournir les outils appropriés
Tout le personnel doit avoir accès à un ensemble complet d’outils fonctionnels afin de pouvoir agir rapidement et efficacement. L’utilisation d’un logiciel de gestion de maintenance pourrait être une solution appropriée car il peut regrouper tous les manuels et documents relatifs aux équipements sur une seule plateforme et y donner accès à tous.
Il regroupe également des rapports importants, l’intégration avec d’autres modules et des capacités de surveillance avancées qui peuvent tous aider les techniciens à mieux faire leur travail.
Améliorer votre équipe
Vous devriez essayer de vous entourer de techniciens qualifiés formés pour agir rapidement et efficacement en cas de pannes et de dysfonctionnements des équipements. En plus de recruter l’équipe adéquatedès le départ, vous pouvez compléter le développement de votre équipe en leur fournissant une formation supplémentaire.
Étant donné la nature du travail de maintenance, qui nécessite une communication efficace à chaque instant, il est particulièrement important d’avoir une équipe motivée qui s’efforce de maintenir un bon niveau de service.
Former votre personnel
Tout membre du personnel au sein de l’organisation doit être capable de signaler une défaillance.
Le personnel non technique doit également être capable de détecter les problèmes potentiels de maintenance et de les différencier. Par exemple, tout le personnel doit être en mesure de reconnaître qu’un bruit inhabituel lors du fonctionnement de la machine peut signaler une défaillance potentielle. Le personnel peut utiliser un logiciel de maintenance pour résoudre ce problème. Cela facilitera également la tâche des gestionnaires pour attribuer le technicien le plus approprié à certains problèmes.
Automatiser l’attribution des techniciens
En fonction de la nature de la défaillance, les pannes doivent être automatiquement attribuées au technicien le plus approprié sans trop de travail administratif. Par exemple, lorsqu’une panne survient dans un circuit électrique, il est préférable que la tâche soit automatiquement et sans heurt attribuée à l’un de vos électriciens. Et si c’est dans le système d’eau, elle doit être attribuée à un plombier, et ainsi de suite.
Optimiser la charge de travail de l’équipe
Une bonne solution pour effectuer une maintenance corrective est de planifier les tâches en fonction de l’analyse de vos données d’ordres de travail. Cela vous aidera à prioriser vos tâches et à vous assurer que votre équipe de maintenance se concentre sur les travaux les plus importants.
Vérifier et organiser les pannes
Il est très utile pour les techniciens et les gestionnaires de pouvoir consulter des informations concernant les pannes et leur statut actuel à tout moment et depuis n’importe où. L’utilisation d’une plateforme de maintenance intelligente (PMI) permet au personnel de savoir exactement ce qui a été fait et quelles tâches sont encore en suspens.
Maintenir un bon stock d’équipements
Les réserves doivent être bien équipées de diverses pièces de rechange et de matériels. Les techniciens ne doivent pas avoir à attendre longtemps pour des articles simples comme des boulons et des vis !
Préserver les actifs
L’équipement doit être inspecté chaque fois qu’une maintenance corrective est effectuée. Cela aidera à identifier la cause de la panne et à permettre de prendre des mesures pour éliminer ou réduire la fréquence de pannes similaires. Un logiciel de gestion de maintenance, tel qu’Infraspeak, peut faciliter le travail des techniciens en leur permettant de consulter toute intervention tardive ou défaillance répétée.
Saviez-vous que… ?
Une Plateforme de Maintenance Intelligente (PMI) peut vous aider à gérer et évaluer votre stratégie de maintenance. Infraspeak vous propose une multitude de fonctionnalités, notamment la gestion des défaillances, des actifs, des bons de travail, des coûts, et bien plus encore.
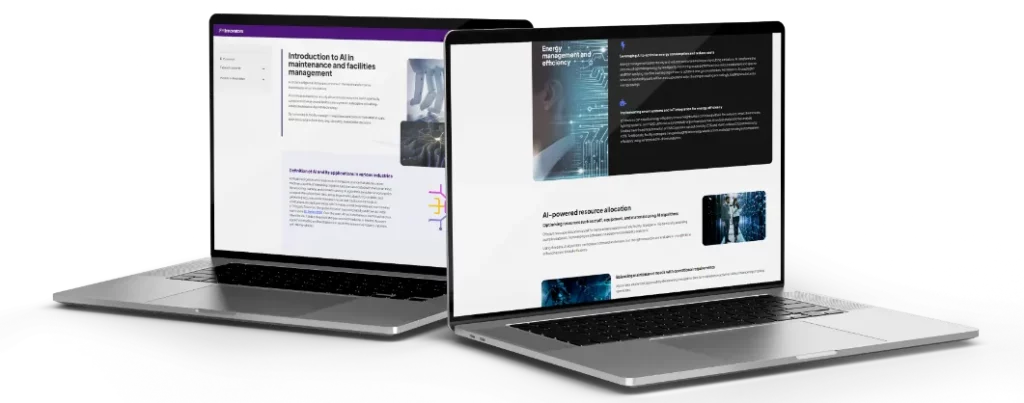