What is asset management?
Asset management coordinates the life cycle of assets. This involves assessing opportunities and risks at every point in time to achieve the desired performance. The aim of asset management is to extract the highest possible return from each investment and thus make the company more competitive.
Naturally, we are focused on the management of tangible assets. In this context, physical asset management encompasses all phases of the assets’ life cycle. Planning what can be useful for the company’s objectives, acquiring new assets, monitoring their performance over time, and deciding when to replace them. The international standard governing asset management is ISO 55000:2014.
What is the life cycle of assets?
It is understood that the life cycle of assets has four phases:
- Planning. The manager becomes aware of an obstacle in one of the company’s processes and looks for the best equipment to solve the problem.
- Acquisition. The potential ROI of the asset is calculated, the available capital is assessed, and a final decision is reached.
- Operation & Maintenance. The asset begins to bring benefits to the company. As time goes by, it requires more and more maintenance. This stage is often represented by the bathtub curve.
- Disposal. The asset has reached the end of its life and has to be dismantled, recycled, or sent to a landfill.
Many companies tend to focus on the third stage, where the asset influences the company’s performance. However, neither phase should be overlooked. Take the aviation industry, for example, where airlines have to order aircraft years in advance for each route, ensure they are kept safe, and provide passenger comfort.
But just as important, if not more important, than knowing the life cycle of assets is having an estimate of their useful life. Only then can you know if the asset “still has a lot to give” or if it is in its decline phase. This type of data is essential to decide whether to repair or replace an asset that begins to show signs of failure.
Difference between asset management and asset maintenance management
Although maintenance management is essential for good asset management, we should not confuse the two. While asset management is concerned with managing the entire life cycle of each piece of equipment, costs, and depreciation, etc., maintenance management is a continuous process to improve the availability, reliability, safety, and condition of physical assets during their useful life.
In asset-intensive industries, ensuring the availability, reliability, and profitability of assets is a huge competitive advantage.
In other words, maintenance management is about planning maintenance tasks, scheduling them, and managing resources (including parts, labour, and budget). It is one of the main parts of asset management, but not the only one. We further explore the differences between maintenance management, facility management, and asset management here.
What are the benefits of asset management?
Centralise all your data
Asset management software gives you a comprehensive overview of all your company’s assets. This includes both on-site, fixed assets and mobile or remote assets. Using a single platform, a complex system of assets becomes streamlined into digestible information that can help you stay in control and handle work orders.
Complete lifecycle management
Proper asset management provides a framework to monitor the performance of assets and acts as a repository for information over their entire lifecycle. You can then use this asset data to improve maintenance processes and even predict behaviour over time.
Increase asset uptime
Asset management allows you to find out when assets are underperforming using specific benchmarks and generate work tasks automatically. This helps you to take action before failure occurs and keep assets running at their best. Not only does this help you meet Environmental, Health and Safety obligations, but also reduces unplanned downtime.
Make decisions in real-time
Using an asset management software makes it easy to prioritise repairs and maintenance. This allows you to give critical assets a higher priority, for example, to ensure they continue to run as efficiently as possible.
Improve financial planning and efficiency
As you analyse the entire asset life cycle, you can better predict what the useful life of each piece of equipment is and when is the right time to replace it. This means you can plan much better the purchase of equipment and the cost of maintenance at each stage of the asset’s life.
Assure compliance with processes and standards
Finally, by monitoring all your assets and ensuring they remain reliable, you can meet all your industry standards and ensure compliance with quality and safety rules.
📝 You may also like: Why inventory control is crucial for streamlining facility operations
What is Enterprise Asset Management?
Enterprise Asset Management (EAM) is the process of tracking, monitoring, and maintaining physical assets and infrastructure. Asset-intensive organisations use EAM to keep an eye on their property and make sure everything’s working as it should.
EAM is now a multi-billion pound industry and is expected to be worth £4.8 billion by 2026. A more comprehensive approach helps reduce costs and maximise the performance of physical assets. Without EAM, assets may not run at their best. This can reduce the performance of critical assets, affect productivity, and ultimately impact your bottom line.
How does EAM software work?
EAM starts with implementing a framework to categorise assets. While this can be something as simple as a spreadsheet, most organisations will use dedicated asset management software. You can either install this locally on-premises or use a remote cloud platform.
Asset managers can then edit asset details and add attachments as they wish. This can include important information such as documentation, manuals, and vendor contracts. Everything is kept together in one place, digitally.
Once assets are added, EAM systems make it easy to automate and manage the work order lifecycle. This includes preventive maintenance, issuing work orders, getting customers to sign off on invoices, and arranging work teams.
EAM also stores the status, repair and work history of each asset. This allows your EAM system to be used as a knowledge base for a facility’s assets. This central data store can then be used to spot useful information and generate reports. You can then use this to identify inefficiencies, stay compliant, and help train staff.
Who needs EAM?
Any organisation that handles a large number of assets should implement an EAM system. In most cases, you’ll be using EAM software if you are a maintenance manager, facility manager, or another kind of asset professional.
But EAM systems can be accessed by lots of different people though across different departments. These can all help keep asset information up to date and maintain accurate data.
Tell-tale signs that you need EAM software include:
- Manually tracking assets using paper or spreadsheets
- CMMS not providing accurate data
- Growing backlog of work orders
- Long asset downtime
- High energy consumption facilities
- Assets failing sooner than expected
What can Enterprise Asset Management software do?
The main function of an EAM system is to act as a knowledge base for all your assets. EAM acts as a point of reference for your company to keep asset data up to date, automate maintenance tasks, identify asset inefficiencies, and coordinate your field teams.
Whilst the bells and whistles of EAM systems can change from platform to platform, the core features include the following:
Monitor assets throughout their lifecycle
The most important feature of EAM is asset lifecycle management. Every asset in your company has a period of operating at peak performance before becoming inefficient. EAM helps extend this optimum operating life and identifies the point where repair and maintenance costs outweigh the cost of replacement.
Manage work orders (accountability)
Work order management is a core feature built into all EAM software. This helps you stay on top of maintenance requests. You can set enterprise asset management software to prioritise work orders automatically, with the status of each tracked in real time.
Co-ordinate and instruct field teams
EAM also helps you assign the right people to a job. Using EAM software, you can track the performance, training, and activity of individuals or entire teams. This allows you to deploy the right technicians to repair and maintenance tasks and can make auditing a lot easier. Your organisation can use mobile and NFC technology to update records on the fly, keeping EAM data accurate.
MRO inventory management
Using EAM software lets you take control of your supply chain and inventory too. At a glance, you can see stock levels of specific parts, past purchases, who your suppliers are, and even make forecasts. Understanding your company’s demand for materials and supplies through all departments can help identify real savings and reduce downtime of critical assets.
Generate reports and track KPIs
Using EAM software, you can also automatically generate different types of reports. These provide insights that can help make your business more productive and identify areas that are costing time and money. You and your team can then use key performance indicators to track progress with easy-to-understand visuals and reports — making it a cinch to identify the cause of problems.
Manage contracts and compliance
EAM software allows you to manage and keep track of all your contracts and comply with PAS 55 standards. Contracts with vendors, employees, customers and more are all centralised within an EAM system. This makes it easy for you to track compliance, costs, and identify redundant contracts.
📝 You may also like: a guide to facility management software
Companies use EAM software to track the condition of assets, so they can save money and be more efficient. EAM aims to make it easier for you to keep assets operating at their best for longer. As discussed, EAM achieves this by acting as a hub for asset data. This not only streamlines the reactive maintenance process but enables predictive maintenance.
EAM systems aim to catch problems early to stop a small problem from turning into a big one. Predictive maintenance is one of the very best ways an asset-intensive organisation can save money. In fact, a 2018 report found that companies that shift to a proactive repair schedule:
- Boost uptime by 9%
- Decrease asset costs by 12%
- Extend asset lifecycle by 20%
- Reduce associated risks by 14%
EAM helps asset professionals move away from a reactive approach towards a proactive one that is both preventive and predictive. As well as preventive scheduling and prioritising, proper asset management can utilise a wealth of asset data to keep you in the know about which assets may need attention.
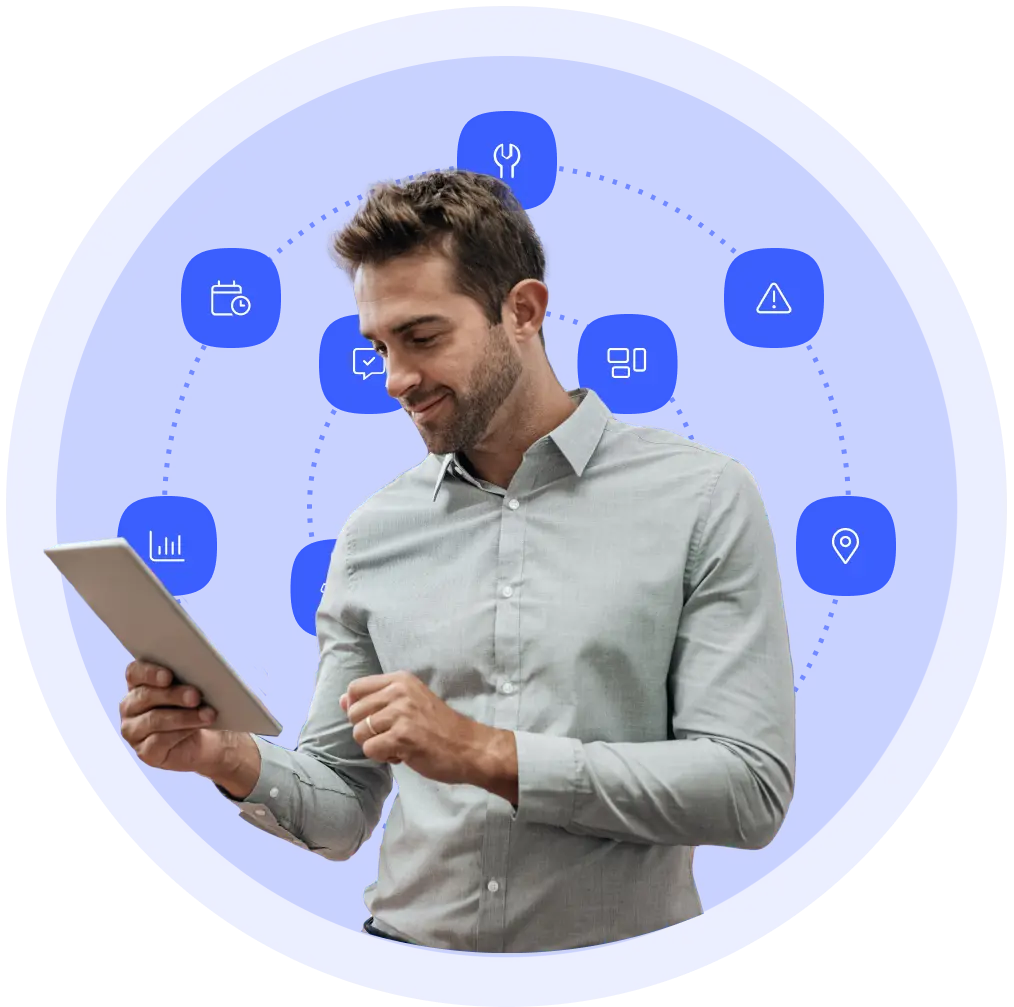