These are probably two of the words you hear the most in a day: work order. Maintenance revolves around work orders, and yet there’s still so much we can do to improve them. Throughout this post, we will explain what is a work request and a maintenance work order, what would be a perfect work order and how you can manage all of your work orders more efficiently.
Hopefully, if you’re a maintenance manager, all of this will help you improve your team’s workflow. Ready to dive into the brave new world of work orders and Intelligent Maintenance Management Platforms?
What is a maintenance work order?
Perhaps we could explain the work order process in a shorter article, but then you’d probably need to check a glossary or cross reference with other sources to understand the full picture. So we will take the time to explain each concept in detail, and we hope you can bear with us a little. Let us start at the very beginning: what is a maintenance work order, after all?
Except that’s not the very beginning. For the sake of this article, work orders will be our Universe. And so, we must address our Big Bang. Before there is anything else, there are work requests. These requests are submitted by your staff or by your clients (in the case of maintenance businesses), asking for a certain task to be performed. Once the requests are authorised and accepted by a maintenance manager/planner, the time counter begins – and the work order is born.
From that moment on, the workflow of your company should fall into place. A work order is first and foremost a communication tool, one that should include all the necessary information to perform a task. As we’ll see in a little bit, work orders determine who is authorised to perform it, the scope of the task, who is it assigned to and everything that will get your team from point A to point B. Again, like the Universe, work orders expand and gain a more complex structure.
What are the different types of work orders?
Now that we have clarified the difference between work requests and work orders, we need to understand the different types of work orders that exist. (Are these multiple Universes? Or has this metaphor fallen apart already? Stay tuned to find out).
These are the different types of work orders and what they consist of:
- inspection: these work orders focus on inspecting and reviewing your assets, usually as part of a preventive maintenance strategy or condition monitoring. You can schedule them automatically on your maintenance management platform (IMMP).
- preventive maintenance: maintenance work orders can be, for example, preventive cleaning, routine lubrication, air filter change, complying with manufacturer’s recommendations and so on, to prevent a machine from breaking or any error from occurring.
- emergency: some work orders are emergencies. These tasks must be performed in order to protect expensive company assets and control damages. They usually relate to reactive maintenance.
- electrical: work orders related to wiring, lighting or power supplies, for instance.
- safety: maintenance work orders to prevent health and safety risks, like disposing of hazardous waste or cleaning chemicals.
- special projects: these are one-off work orders, for example to replace assets, install new assets, upgrading and so on.
So… what makes a work order perfect?
If a work order is your Universe, you need to understand what chemical elements it is mostly made of. Detailed maintenance work orders need to contain a lot of information to organise, assign, perform and complete the task. In other words, you should think of the work order like a briefing you need to pass on to your team.
What is the work order process?
But writing a detailed maintenance work order isn’t enough to make it a perfect one – far from it. Work orders need to be managed properly throughout their whole cycle to avoid delays, lack of accountability, higher costs, increased downtime or a backlog of to-do lists. This is why we also need to pay close attention to the order process. This step determines how the elements in your Universe will interact with one another.
- Identification. First, someone identifies the issue and decides to report it.
- Someone creates the request. This turns into a work request which will appear on your maintenance management platform. You should evaluate its criticality, the existing plans for that asset, the age of the asset and the severity of the issue, as well as your resources, before turning it into a work order.
- Prioritise & schedule. After the request is accepted, the maintenance planner will prioritise the task and schedule it accordingly.
- Assigned & completed. The task will then be assigned to a specific technician or team, who will undertake it during the scheduled time.
- Closed & documented. After the maintenance task is performed, it should be marked as complete and documented, so that you can keep track of important data.
- Analysed and reworked. The insights are then analysed to find out what could be improved. The data may be useful in future similar work orders.
What information should a maintenance work order include?
To make a perfect work order, you should include at least the following information:
- Identify the asset and describe the issue. Identify the asset and its location clearly on the work order. Try to describe what happened or the malfunction reported. If the cause is not clear, your technicians should add it later to their report.
- Assignee. Obviously, the task will need to be assigned to a specific technician or team.
- Priority. Don’t leave your team in the dark. It’s important that technicians know what they’re in for and what the most urgent work orders are.
- Parts and tools required. A detailed work order should include which parts and tools are required to perform the task. If you are using an Intelligent Maintenance Management Platform, this will also help in tracking down the costs and managing inventory automatically.
- Health and safety notes. If there are any risks associated with the task, technicians should be warned. Attach any documents regarding safety measures to the work order before your team sets out to do the job.
- Expected completion date and expected hours of work. The final report should include when the order was requested, when it was performed, the expected completion date and the actual completion date. This will help managers with scheduling and lets them determine how long the equipment was down, the mean time to repair, etc.
- Other notes and documents. If there is any other relevant data or if your technicians want to add information later on for future reference (completion notes).
Free Work Order Template in Excel
Easily create complete and customised work orders for preventive or reactive maintenance interventions with this easy-to-use Excel template. Share the file with all your potential requesters to streamline the communication between them and your maintenance team.
With this template, you can access:
- All your assets and team members.
- Optional dropdown menus for faster filling of the work order.
- Adaptable fields for reactive or preventive maintenance.
→ Download your Work Order template here
How can you manage maintenance work orders more efficiently?
Now that your knowledge of your Universe is broader – you know how it began, how hydrogen and helium work together and you’ve carefully observed it – you might be wondering what’s the best, most efficient way to organise all this information.
You’ll want to recall what we said at the beginning of this article: work orders are first and foremost a communication tool. Making a perfect work order is all about passing on the right information through all the stages of the process.
How can you organise maintenance work orders?
For as long as preventive maintenance has existed, pen and paper have been faithful friends. They are easy to use and cheap — no instructions needed whatsoever. But every rose has its thorn. Papers tend to get lost or misfiled, take up lots of space, and they aren’t exactly an environment-friendly option. That’s how some people arrived at whiteboards, although they are not a viable answer in terms of space either.
More recently, Excel sheets became every maintenance planner’s best friend. They are relatively simple, harder to lose and easy to archive.
However, this is not exactly cutting-edge technology, so it may not be your best bet, especially if you have a relatively large team (more than 3 or 4 technicians) and want to stay ahead of the competition.
💡Enter the Intelligent Maintenance Management Platform. Now, you can store every work order in the cloud, which makes it available to all of your team at all times. A simple phone is enough to keep them up to date with notifications and requests. It’s easier for your clients to make a work request, you reach out to your team, and everything runs smoothly.
How does an IMMP work in managing work orders?
First, it’s easier to write detailed work orders with an IMMP – don’t forget it will store all the info regarding each asset, stock, and part. Technicians will find every document they need in the blink of an eye, which saves the team even more time. They’ll get instant notifications to put everything in motion immediately, which is vital in urgent work orders. It’s also possible to schedule inspections or preventive work orders automatically with a certain frequency. If you’re still doing this manually, it will be a time-saver too.
Finally, monitor your preventive and reactive maintenance work orders with the collected data. The software can calculate key performance indicators such as compliance with preventive maintenance plans, the mean time between failures (MTBF) or mean time to repair (MTTR). Sure, it might seem like a lot of data, but the secret to managing your work orders more efficiently is in the details. Remember: losing just 15 minutes a day will rob you of 1 hour of work every 4 days!
This is how it all should work, at least in theory. Ultimately, regardless of your preferred method for organising and managing work orders, everything comes down to the people using it. A maintenance management platform relies on the data you give it. If you and your team make good use of your platform, inserting all the necessary data to perform tasks and collect reliable data, it will work smoothly. If not, it can be just as unreliable as any other method. To avoid this, we strongly suggest that you request help to train your employees during the onboarding phase.
Managing work orders with Infraspeak Network™
Muddy communication continued to be a major obstacle for Client and Supplier even after the contract was signed. What happens when they walk through the door? How do you reach them?
The Infraspeak Network™ allows the Client to share and collaborate on work orders with the Supplier, including a list of tasks that need to be executed. For example, if there’s a problem with an HVAC asset, the tasks might include:
- Remove Filter
- Clean Filter
- Replace Filter
The Infraspeak Network™ simplifies everyday processes like quote requests and proposals, sharing work orders and monitoring maintenance carried out by suppliers. These newly enabled workflows allow you to do the following from the comfort of your Infraspeak platform:
✔️ Expand your Client/Supplier base and book of contacts
✔️ Manage quote requests and agree on proposals for work orders and purchase of stock.
✔️ Execute contracted maintenance work more efficiently.
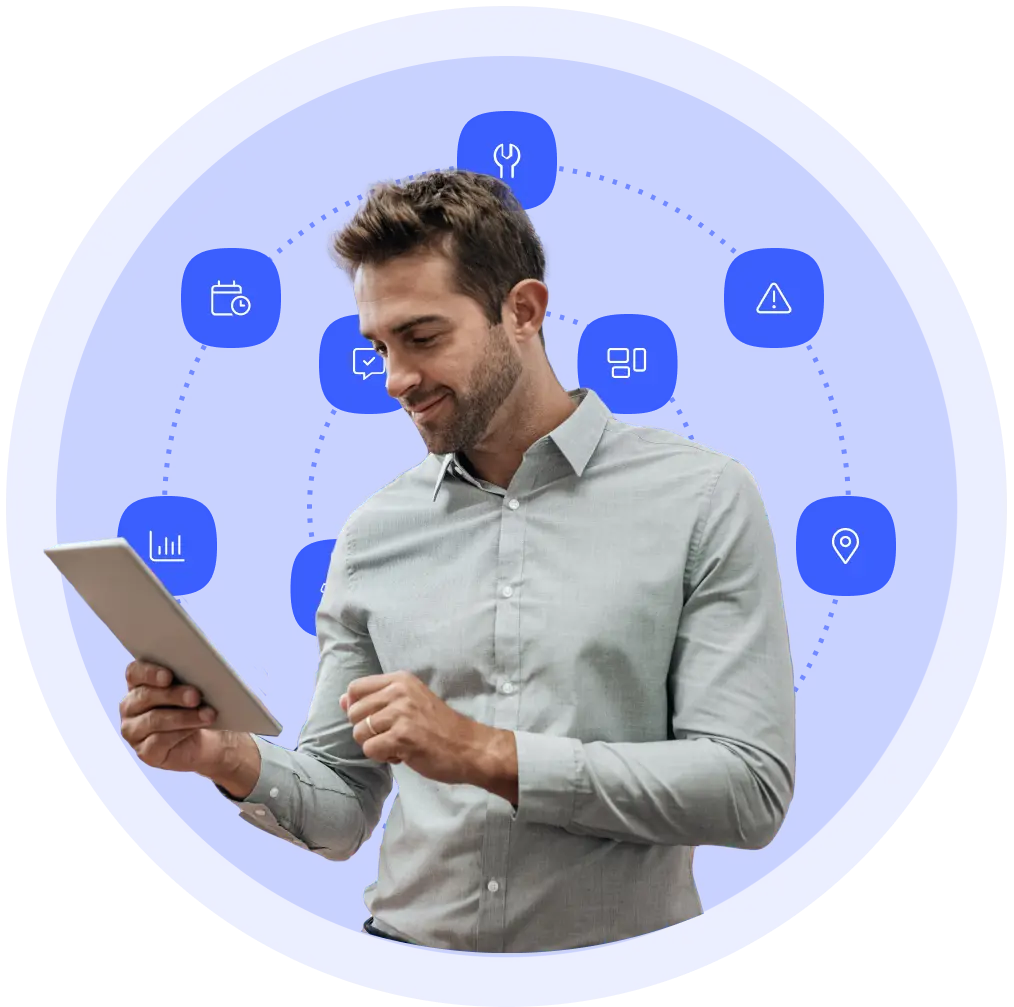