What is a maintenance log?
A maintenance log is a document that shows all the maintenance work that has been performed on a given asset. The information on these documents varies according to the equipment and your maintenance management software.
However, maintenance logs usually include (1) general information, like the name of the asset, serial number, location, date of purchase and date of first use, and (2) a list of actions and who performed them, perhaps with a brief description.
The 3 types of maintenance logs
Although all maintenance logs register maintenance actions, we can set three types of maintenance logs apart:
- Maintenance schedule logs. These are timetables for ongoing projects within the operation, including the estimated time to complete each order. This gives managers a great overview of everything that is happening.
- Machinery maintenance logs. These logs plan maintenance activities for each machine or asset, and their respective deadlines to keep them running.
- Project logs. They overlap with maintenance schedule logs to a point, but these logs also include complete projects (and not just ongoing ones) and projects from other departments.
What are the benefits of maintenance logs?
Registering information about every work order isn’t necessarily appealing, so here are 6 gentle reminders of why you should keep maintenance logs:
✓ Easier time scheduling maintenance. Accurate maintenance logs let you know how often you’re performing a certain task, and how long it takes on average. You can optimise your preventive maintenance schedule based on this information and design machine-specific plans for critical assets.
✓ Faster diagnosis and repairs. Learn from the mistakes of the past! Maintenance logs let your technicians know how failures were diagnosed and repaired in the past. They can check when the failure last happened, which parts were replaced, and read remarks from repair personnel.
✓ Better informed decisions about whether to repair or replace. Deciding whether to replace or repair an asset is a question maintenance managers have to face time and time again. Having up-to-date maintenance logs helps them assess if there are safety hazards, increasing breakdowns, and weigh the “health” of an asset.
✓ Improve safety at work. Because managers are constantly aware of the current condition of each asset, safety hazards can be dealt with promptly. Besides, tracking the maintenance schedule’s compliance makes it less likely to miss health codes and other guidelines.
✓ Validate warranty claims. Maintenance has a bad reputation as a “necessary evil”. But, for maintenance managers, insurance claims when a machine breaks down are often the necessary evil. Maintenance logs attest you performed appropriate maintenance according to the manufacturer’s guidelines.
✓ Increase resale value. Proof that you have a well-maintained machine, with very few breakdowns and original equipment manufacturer parts, can increase resale value. Remember that resale value counts as salvage value if you’re calculating straight-line depreciation.
How to create a maintenance log
Define your objectives
Before you start, determine the purpose and objectives of your maintenance log. Are you creating it for a single piece of equipment, a group of similar equipment, or for various types of equipment? Understanding your goals will help you design the log effectively.
Gather necessary information
Collect all the essential information you need to track maintenance, including equipment specifications, identification numbers, manuals, and any historical maintenance or repair records. You should set up categories and columns to capture relevant information, for instance:
- Date of Maintenance
- Description of Work
- Maintenance Type (e.g., routine, preventive, reactive)
- Technician/Engineer Name
- Parts/Components Used
- Hours Spent
- Next Scheduled Maintenance Date
- Notes or Comments
Record the maintenance data
As maintenance or repair activities are performed, record the details in the log. Make sure to be accurate and thorough, including the date, what was done, who performed the work, any parts replaced, and the time spent on the task. If there are specific guidelines or checklists in the equipment manual, you can use those as references.
Regularly update the log
Consistently update the maintenance log whenever maintenance or repairs occur. This will help you keep an up-to-date record of the equipment’s maintenance history.
Review and analyse data
Periodically review the log to identify trends, such as recurring issues or maintenance needs. This information can help you make informed decisions about equipment replacement, upgrades, or changes in your maintenance schedule.
How to optimise maintenance logs with intelligence
No matter what you do, resist the temptation of making lengthy maintenance logs. Although maintenance logs have several advantages, they should not take technicians’ time away from maintenance work.
Before you ask your staff to track something, think twice: will this data be useful to make decisions in the future? Will it allow me to organise data sets and optimise maintenance plans? Do I need to provide this data to clients?
Of course, you can (and should) ditch old paper maintenance log sheets to save time. For example, with an Intelligent Maintenance Management Platform (IMMP), technicians can swipe an NFC tag to start and close an order, and generate time logs automatically.
Advantages of using an IMMP to register maintenance logs
- Paper can easily be misplaced or lost, which does not happen with digital maintenance logs. Also, you can find them any time without getting into dusty archives.
- With a mobile platform, maintenance logs are available anytime, anywhere.
- Promotes better accountability, since it’s possible to know who did what and when. Once you open the work order, you can see when it was created, who approved it, and opening/closing times.
- Less room for human error, since technicians don’t need to write logs manually and/or from memory after they’ve completed the work.
- Technicians can also write messages and attach files, such as photos, which might be helpful for future interventions by less wary or less experienced staff.
- Automated data recording. Apart from tracking the time it takes to perform each work order, the app will cross-reference data in different apps and deduct stock from your inventory, estimate costs, suggest suppliers and generate automatic reports to update clients.
- Overall, it’s easier to have an overview of an asset’s history, even going back years. You can filter by failure type, technician, and priority.
Maintenance logs are not a sexy part of the job, but they are a necessary one. Without logs, managers cannot check if work orders are completed in time or track operations.
💡Intelligent maintenance management platforms make it less time-consuming, ensure logs are more accurate, and easier to browse. Finally, cross-referencing data promotes maximum transparency, accountability, and efficiency.
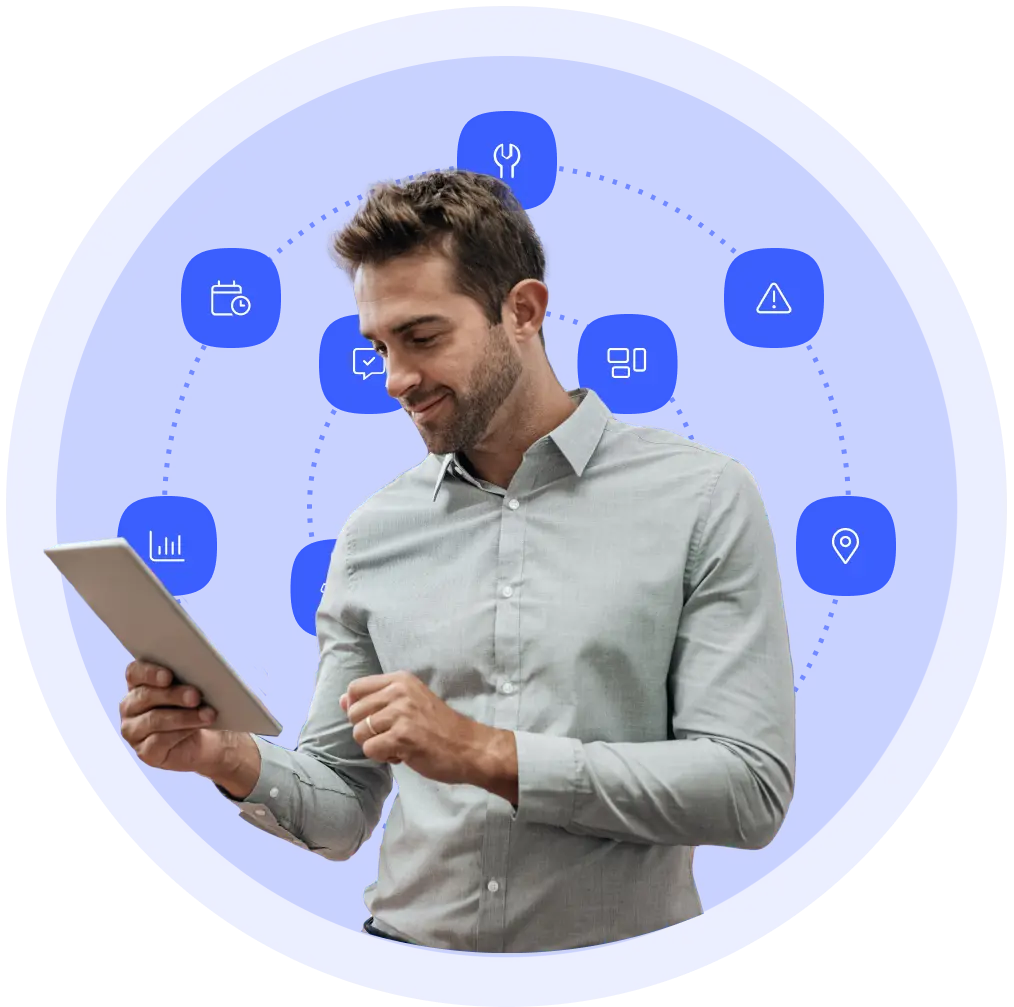