When it comes to safety, you can never be too careful. Maintenance workers are exposed to several hazards, and accidents during repairs are not uncommon. LOTO (“lockout-tagout”) procedures are one of the most cited ways to tackle these issues, and that’s exactly why we’re talking about them today.
- Out of 111 workplace fatalities in 2019/20 in the UK, 29 were due to falls from heights, 20 were due to a moving vehicle, 18 were struck by a moving object, and 11 were caused by moving machinery.
- Maintenance workers are exposed to physical hazards, such as dangerous amounts of noise, excessive vibration, radiation, chemical and biological hazards, and demanding physical work.
- In the UK, maintenance-related accidents account for 25-30% of all manufacturing industry fatalities. Manufacturing and construction are obvious high-risk activities, but they are not the only ones.
- Maintenance accidents often occur in sectors that aren’t perceived as risky, such as hospitality and real estate. In a 2006 study, 29% of Austria’s maintenance accidents happened in hotels and restaurants.
The numbers don’t lie, and neither does your work experience. But how can maintenance managers make their workplaces safer?
Implementing safety features isn’t enough, since they are relatively easy to bypass. To prevent this, American OSHA standards recommend LOTO procedures. LOTO means “Lockout – Tagout” and, simply put, it ensures machines are properly shut off during maintenance activities or shift changes.
LOTO programmes have several benefits:
- setting procedures to shut down equipment;
- promoting safer starting up procedures;
- preventing energy from being released;
- avoiding fines for non-compliance and lawsuits;
- providing increased safety and productivity overall, preventing injuries such as amputation, electrocution, or being struck by moving parts.
LOTO procedures in 6 steps
Prepare for the shutdown
When maintenance requires machines to be shut down, it should be noted on the work order. The responsible team member must review the hazards and LOTO procedures beforehand. Keep in mind that procedures should be tailored to each machine.
Note: It’s generally recommended to make a list of authorised employees and train them extensively in LOTO procedures. The rest of the staff should be informed but does not need such extensive training. However, when it comes to maintenance teams, this happens at your discretion. According to the perceived risks, you may even train everyone.
Shutdown
The responsible technician should shut down the machine according to the manufacturer’s requirements or company guidelines. Instructions should be as specific and thorough as possible, mentioning every potential energy source. Never take any prior knowledge for granted, and explain every step as if the operator hadn’t done it before. Emergency shutdowns are often guided by SOPs.
Isolate the equipment
It’s not a shutdown if all energy sources are not sealed or closed off. First, disconnect all the primary energy sources, such as electricity, water, gas, steam or compressed air. Then, prevent secondary energy – trapped heat, fumes, spills, and kinetic energy (in moving parts) – from being released. Equipment should be completely isolated and motionless.
Place locks and tags
Locks and tags should be placed on valves, breakers, electrical switches, and potential sources of leakage. Locks should be coded and tagout devices must be securely fastened and visible. Some companies adopt visual systems on their tags, with different danger warnings, “do not operate” orders, and even colour coding. Nobody should try to operate the machine until the tagout is removed.
💡 Pro tip: make a checklist of all the plugs and switches that need to be locked out. This will make it easier to order locks and choose suitable devices for electrical and mechanical parts. Lockout stations are a good option to organise them and save time during maintenance or repairs.
Block stored energy
Sometimes, equipment retains stored energy that can be difficult to identify and contain. LOTO procedures should draw attention to these potential problems, including moving parts, springs under tension, pressured steams or water, vents, and so on. You might need to open relief valves, bleed hydraulic parts, install brakes, and take other preventive measures.
Verify equipment isolation
More than lockout-tagout, we should reinforce “lockout, tagout, and try out.” After you have cleared the area, locked and isolated the equipment, try to start it up. It should not be possible to start up the equipment. This ensures unaware employees cannot start the equipment by accident and get injured. Only trained staff should remove the locks and start it up again.
Life after LOTO
After you have implemented your LOTO procedures, what’s next? We recommend periodic energy control inspections to ensure your guidelines are up to date, especially if machines are modified. You can also provide periodic refresher training to your staff. It can be included, for example, in safety and hazard identification retraining.
You can (and should) integrate LOTO software with your maintenance platform. Talk to one of our specialists to find out how an intelligent maintenance management platform can increase efficiency and safety.
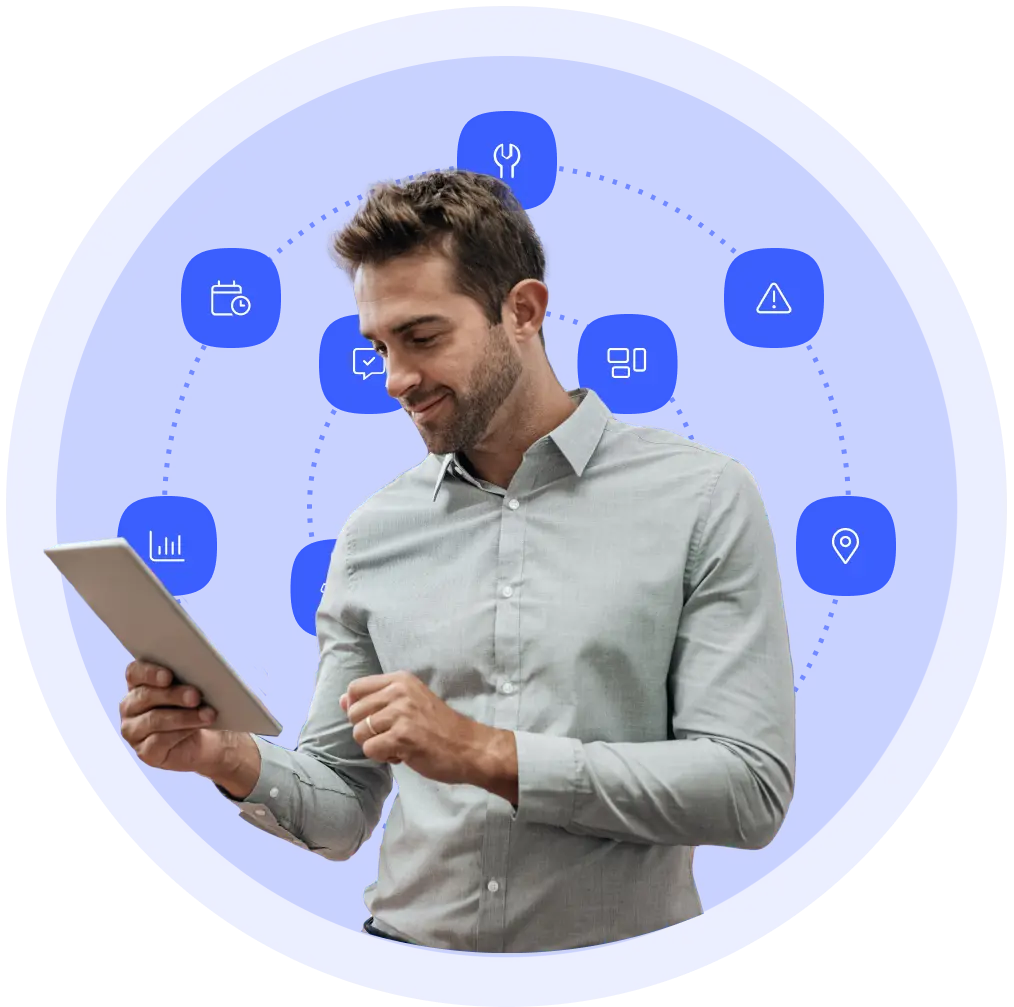