What is inventory management?
Inventory management is the systematic approach to sourcing, storing, and selling inventory — both raw materials and finished goods. It involves the tracking of inventory from manufacturers to warehouses and from these facilities to a point of sale. The goal is to have the right products in the right place at the right time, ensuring that a business can meet demand without overstocking, which ties up capital and increases storage costs, or understocking, which can lead to lost sales and customer dissatisfaction.
Key components of inventory management
- Ordering: The process of purchasing the right quantity of stock to meet demand. This includes determining optimal order quantities and timing.
- Storing: Safely and efficiently storing inventory in warehouses or storage facilities, ensuring easy access and proper conditions to maintain product quality.
- Tracking: Monitoring inventory levels, movements, and locations. This includes using tools like barcodes, RFID tags, and inventory management software.
- Controlling: Managing inventory to prevent overstocking or stockouts. This involves setting reorder points and maintaining accurate inventory records.
- Forecasting: Predicting future inventory needs based on historical data, market trends, and demand analysis.
Advantages of inventory management
Optimised stock levels
By maintaining optimal stock levels, companies can ensure they have enough inventory to meet customer demand without holding excess stock that consumes warehouse space and resources. On the other hand, proper inventory management reduces the costs associated with storage, spoilage, and obsolescence.
Improved cash flow
Efficient inventory management helps businesses maintain a healthy cash flow. Capital isn’t unnecessarily tied up in excess inventory, which allows businesses to invest in other areas of growth.
Better insights and forecasting
Accurate inventory records and data analytics provide valuable insights for demand forecasting and business planning. Businesses can anticipate market trends and adjust their inventory strategies accordingly.
Streamlined operations
Efficient inventory management integrates seamlessly with other business processes, facilitating smoother operations and reducing the complexity of managing large inventories.
📝 You may also like: 10 best inventory management software
Why should you use an inventory management solution?
Implementing an inventory management solution can revolutionise how a business handles its inventory.
First and foremosty, automated inventory solutions significantly reduce human error. Barcoding, RFID tagging, and automated data capture ensure that inventory records are precise. Using an inventory management software automates many repetitive tasks, such as order processing and stock level monitoring, freeing up time for employees to focus on more strategic activities.
These solutions provide real-time visibility into inventory levels and locations. Businesses can monitor stock movements and status updates instantly, making inventory management more dynamic and responsive. On the other hand, whether a company has one warehouse or multiple locations globally, the software can adapt to increasing volumes and complexity.
An advanced inventory management system, like Infraspeak, offers powerful data analytics tools. These help businesses analyse trends, forecast demand, and make informed decisions about inventory procurement and distribution. By optimising your inventory control, an inventory management solution can reduce operational costs, excess inventory, and prevent stockouts, all of which contribute to lower overall expenses.
5 ways to improve inventory management
1. Conduct regular audits and cycle counts
Regular inventory audits and cycle counts help ensure the accuracy of inventory records. Unlike annual physical counts, cycle counting involves counting a subset of inventory on a regular basis. This practice can uncover discrepancies between recorded and actual inventory levels, allowing businesses to address issues promptly. Consistent auditing helps maintain reliable stock data, which is essential for effective inventory management.
2. Optimise order quantities
Using techniques like Economic Order Quantity (EOQ) can help determine the most cost-effective order size. EOQ balances ordering costs with holding costs to minimise total inventory costs. By optimising order quantities, businesses can reduce storage costs, avoid overstocking, and ensure they have enough inventory to meet demand without frequent reordering.
3. Step up your supplier management game
Building strong relationships with suppliers is key to ensuring reliable and timely deliveries. Effective supplier management involves negotiating better terms, such as discounts and flexible payment conditions, and ensuring clear communication regarding lead times and order quantities. Good supplier relationships can also help businesses respond more effectively to changes in demand or supply chain disruptions.
4. Utilise demand forecasting
Accurate demand forecasting involves using historical sales data, market analysis, and predictive analytics to anticipate future inventory needs. By understanding trends and seasonal fluctuations, inventory levels can be aligned proactively.
5. Implement an inventory management software
Using dedicated inventory management software, such as Infraspeak, can streamline and automate various inventory-related tasks. This software provides real-time tracking of inventory levels, automates reordering processes, and generates insightful reports. Features like barcode scanning, RFID tagging, and mobile accessibility ensure accuracy and efficiency; also, software integration with other business systems like ERP and CRM enhances overall operational coherence.
Why is an IMMP ideal for inventory management?
While regular inventory management software focuses primarily on tracking and managing inventory levels, an Intelligent Maintenance Management Platform (IMMP) like Infraspeak offers a more comprehensive approach by integrating maintenance management with inventory control.
Holistic approach and seamless coordination
An IMMP integrates inventory management with maintenance operations, providing a holistic view of both. This ensures that inventory is not only tracked but also aligned with maintenance schedules and requirements. By linking inventory with maintenance tasks, businesses can ensure that the necessary parts and materials are always available for repairs and maintenance activities, reducing downtime and improving operational efficiency.
Data-driven insights
Infraspeak uses advanced data analytics and IoT (Internet of Things) sensors to monitor equipment health. A proactive approach is adopted, which helps in planning inventory needs in advance, ensuring that parts are available before they are required. Goodbye, delays, hello, productivity!
Enhanced reporting and analytics
IMMPs provide detailed analytics not only on inventory levels but also on equipment performance, maintenance schedules, and operational efficiency, allowing you to make informed decisions regarding both inventory and maintenance processes. You can generate fully customisable reports that offer intelligent insights into inventory usage, maintenance costs, and equipment lifecycle management, facilitating strategic planning and continuous improvement.
Improved resource allocation
By integrating inventory management with maintenance, you can be sure that resources are used efficiently. For example, parts can be allocated to critical maintenance tasks, preventing overstocking of less critical items and understocking of essential ones. Infraspeak also helps in managing labour resources by scheduling maintenance tasks effectively, ensuring that technicians have the necessary parts and tools to complete their work without delays.
Real-time monitoring and alerts
Real-time updates on inventory levels, equipment status, and maintenance activities — an IMMP provides you all this and more, so any issues are promptly addressed, thus preventing disruptions in operations. Get automated alerts and notifications for low stock levels, maintenance due dates, and equipment anomalies.
Scalability and flexibility
Last but definitely not the least, IMMPs are highly scalable and can adapt to the growing needs of every business. Whether managing a single facility or multiple locations, Infraspeak can handle increased complexity and volume without compromising efficiency. Customisable workflows and features can be tailored to specific industry needs, so that the solution fits the unique requirements of your operation.
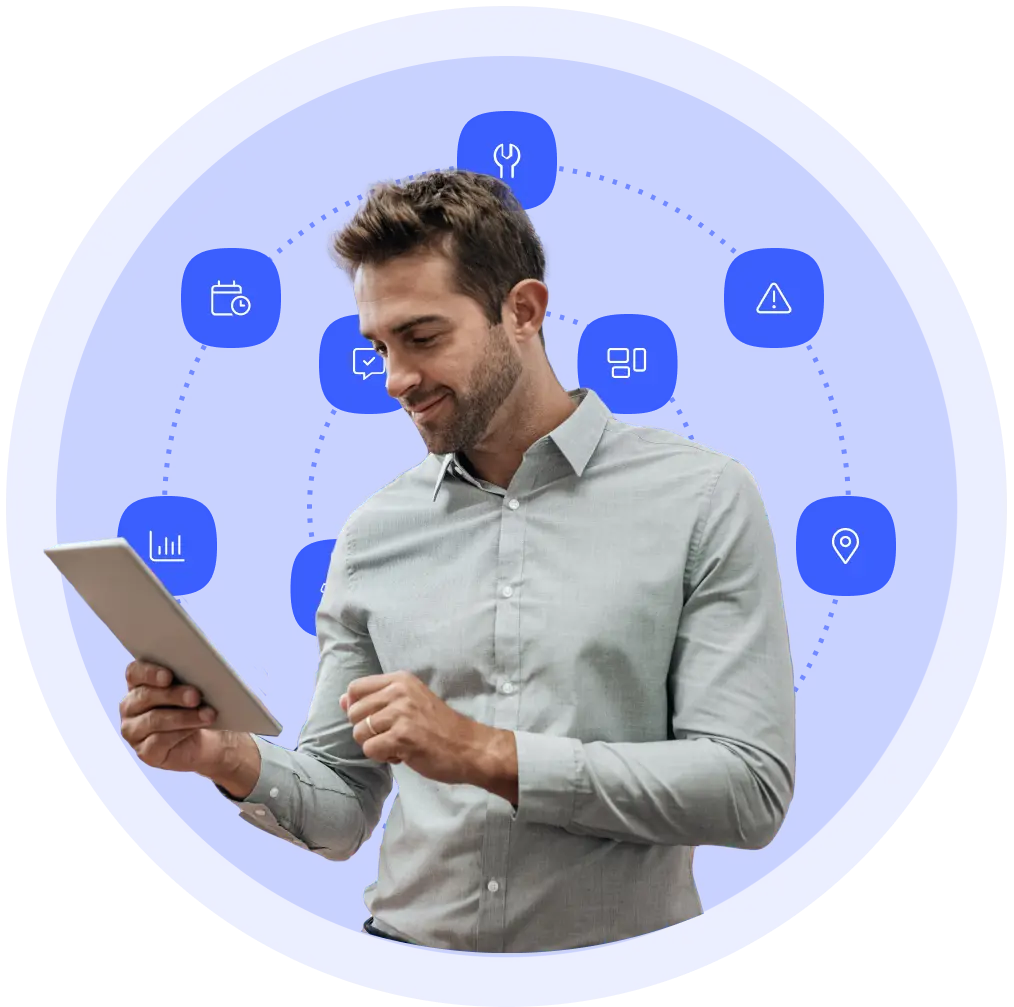