Technology is hailed as the ultimate time-saver, but we all know that’s not always the case. Digital tools like CMMS, for example, often fail to deliver on that promise. Their complexity makes them cumbersome for those in the field, and over time they become abandoned cornfields with very little valuable data.
Current CMMSs are not the answer
According to McKinsey, technicians continue to spend less than half of their time doing practical work, dropping below 30% in some cases. During the remainder of the time, they’re looking for the right materials and tools, along with protective equipment, reading relevant information, entering information, checking permits and so on.
Granted, technicians will never have their hands on tools 100% of the time. Even with the most cutting-edge technology, they will always spend time getting whatever they need for the repair. But they can get themselves organised much faster with intuitive software that compiles all the relevant information.
Centralised information and integrated operations
For service providers, whose core service is maintenance itself, integrated operations aren’t just “something nice to have”. Everything must be connected to the core to maximise resources, be agile, and become more competitive. Even less obvious integrations, like accounting tools, can streamline business with clients.
Integrating your maintenance software with your client’s building management systems – like Siemens BMS, BISYS or Projedomus – is pivotal to collect data in real time, receive notifications, and make data-based decisions regarding maintenance intervals, energy consumption, asset lifecycle management, and much more.
Service providers can also improve their own planning, be it through integrations with their ERPs, route optimisation software, or communication tools. Overall, it’s safe to say integrated operations offer a better user experience to your team as well.
📝 You may also like: What is integrated facilities management and how it works
Benefits of integrated maintenance operations
Improve end-user experience
Integrated maintenance can help you deliver a better service. However, we’ve also seen that the user experience doesn’t improve just from the client’s point of view. For managers and technicians alike, it’s much easier to manage their daily routines.
Troubleshoot more efficiently
Failures happen – that’s a fact of life. What sets you apart is how quickly you can solve them. When your technicians can easily access the equipment’s logs and technical docs, they’ll reach a diagnosis faster and see how the problem was previously fixed.
Enable condition monitoring and predictive maintenance
According to McKinsey, condition monitoring and advanced troubleshooting, which are ‘simpler’ than predictive maintenance, can yield impressive results. But you’ll need a data-focused mindset and reliable data, which is easier to come by with integrated ops.
Reduce emissions and energy consumption
Non-residential buildings use, on average, 40% more energy than residential buildings. Making sure equipment is well-maintained, as well as integrating your maintenance platform with building management systems, can have a real impact on reducing most businesses’ carbon emissions.
Promote remote work and become more resilient
If you associate “integrated operations” with “remote work”, you aren’t entirely wrong. While it’s not all there is to it, integrated operations certainly enable several teams to work together remotely, which makes you more agile, resilient and Industry 5.0-ready.
Ensure compliance and never miss an SLA
Centralising information and integrating your platform with your client’s software helps you comply with regulations, laws or even ISO quality standards. Besides, you can collect data that proves compliance with the SLAs you agreed to.
More data supports better decisions
Ultimately, integrated operations allow you to collect more data, which supports better decisions. You can figure out ways to avoid waste and maximise resources, improve maintenance planning, and deliver a top notch performance every step of the way.
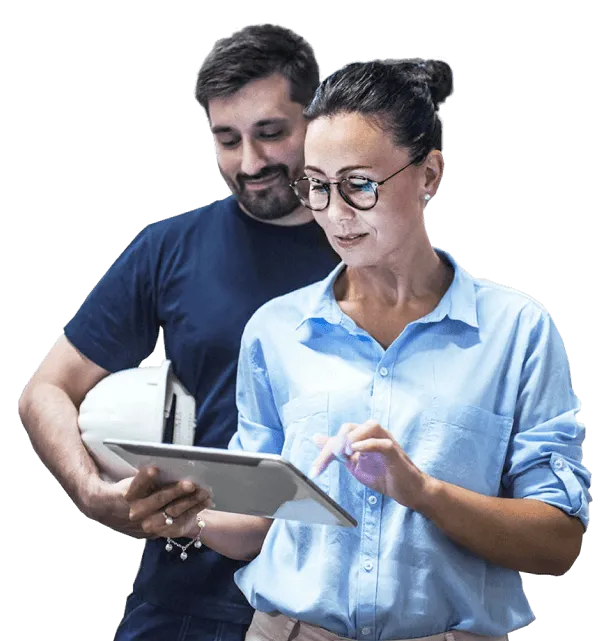