The Internet of Things (IoT) has changed the way we interact with the world. However, the world of Industry 4.0 has already taken a step forward and brought us the IIoT. Around here, we can barely contain the enthusiasm with the implications it will have on the industrial maintenance and predictive maintenance universe.
What is IIoT?
The Internet of Things (IoT) is no longer a dream, but a reality. Nowadays, (almost) everything is connected to the internet – from the city traffic lights to our bank account. Without taking it too far, think about your phone. How much data does a simple cell phone gather about you? How does GPS know where the traffic is most intense? This is the network we call the Internet of Things. However, nothing about this is new.
But… what if this Internet of Things could be used in our favor to produce something greater and better? To gather information that was previously unreachable? These were exactly the questions the creators of Industry 4.0 asked.
The answer, as you may have guessed, boils down to four letters: IIoT (Industrial Internet of Things). If all machines are connected to the network, they can transmit information to teams and, within the near future, analyse data and make decisions on their own. Surreal? Buckle up, because we are just starting.
How does IIoT work?
The beauty of the Internet of Things lies in its simplicity. After all, it all comes down to one word: connectivity.
Today there are already some factories where almost everything is automated – all that remains is to develop artificial intelligence so that failures are automatically corrected. While it might not be in the nearest future, industrial robots are being improved, machines are connected to sensors, NFC tags and the gathering of big data allows for some analysis to be done automatically.
Note that the Internet of Things or IIoT is not limited to the industrial setting. We can also use these technologies in agriculture, for example, with sensors and data-gathering tools that allow us to adjust drip irrigation systems or know which minerals are depleting in the soil. Financial services can be even safer, with no room for human error, with technologies like Blockchain. Even medical assistance can be improved, as there are already sensors that warn caregivers when a patient needs help. The possibilities are endless.
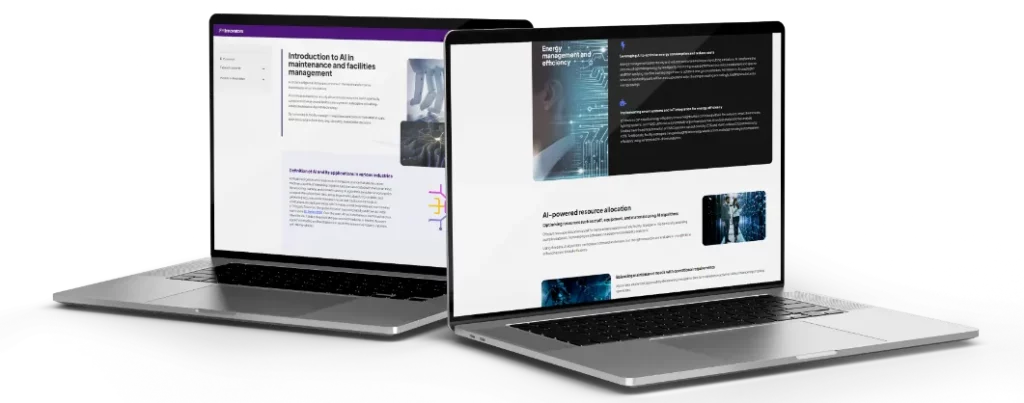
How can we apply IIoT and the Internet of Things to industrial maintenance?
The keywords here are data gathering. Since the moment that machines have sensors and collect data that we previously didn’t have access to, it becomes easier to predict when a failure will happen. Finally, industrial maintenance strategies based on predictive maintenance are within our reach – and it is the possibility to make this transition that makes IIoT as exciting for maintenance technology as it possibly could.
What is predictive maintenance?
Despite not being a new concept, maintenance is still divided into two main types: preventive maintenance and corrective maintenance. Preventive maintenance does not prevent all failures. We can also never be sure that we are not wasting resources (equipment, time, and human resources) carelessly. On the other hand, waiting for a failure to happen, and adopting a reactive approach leads us to constant corrective maintenance, which is usually urgent and more expensive.
Predictive maintenance unites the best of both worlds. First of all, it removes the uncertainty that is associated with preventive maintenance: “am I focusing on the right assets?”, “Is this the best working agenda?” and so on. Then, it prevents failure from actually happening. So, compared to a reactive approach, it significantly reduces downtime, increases asset availability, and reduces costs.
To add to those benefits it’s also worth mentioning the machines’ ability to manage maintenance requests on their own, or the software’s ability to demand maintenance based on the information gathered from the sensors. Then the same mechanisms will be connected to the IMMP, which will notify the staff accordingly. And we can follow this whole process from our cell phone. So, all in all, forget about manual data entry or gathering.
For the time being, there is a clear disadvantage: the cost associated with the installation of sensors and the necessary data collection tools. Certainly, these technologies are not within the reach of all companies. As the Industrial Internet of Things becomes a reality, however, we are sure that we are entering a new era in the world of maintenance and Industry 4.0.
Here at Infraspeak, we have already booked a front-row seat.