¿Qué es el análisis de los 5 por qués?
El análisis de los 5 por qués (o los 5 ¿por qué?) es uno de los muchos métodos para encontrar la raíz de un daño. Consiste en un método interrogativo, en el que se pregunta por qué se produjo cada evento que precedió al daño hasta encontrar la causa raíz. Generalmente, se necesitan solo 5 preguntas para obtener la respuesta que buscas, de ahí el nombre «5 por qués».
La gran ventaja de este método es reconocer que hay una serie de eventos que preceden y causan el fallo. Casi siempre los daños se producen por un conjunto de causas y efectos, o un «efecto dominó», más que por un evento inmediatamente anterior. El análisis de los 5 por qués es un método simple y rápido para intentar determinar el verdadero origen del problema, que podemos utilizar en una gran variedad de contextos.
En mantenimiento, el objetivo de cualquier análisis de la causa raíz es corregir el error inicial, aplicar nuevas estrategias para evitar fallos similares y establecer procesos internos que reduzcan al mínimo la probabilidad de cometer un error en cualquier etapa del proceso.
¿Cómo surgió el método de los 5 por qués?
Cuando hablamos de los métodos para hacer el análisis de la causa raíz, siempre es interesante ver en qué contexto ha aparecido. La técnica de los 5 por qués fue desarrollada por Sakichi Toyoda, el fundador de Toyota. De acuerdo con los principios de Toyoda, la máquina «para cuando ocurre un problema». Preguntar «¿por qué?» 5 veces permitía descubrir el origen de ese problema – y la solución para evitarlo se hacía evidente. El concepto formó parte del sistema de producción de Toyota durante la expansión de la empresa, y hoy en día se sigue aplicando como parte de una metodología lean.
¿Cómo funciona el método de los 5 por qués?
Imagina que tienes fiebre. Tomas un antipirético para aliviar los síntomas, pero eso no es una cura. Para eso, tienes que preguntarte «¿por qué tengo fiebre?» ⇢ infección viral ⇢ «¿por qué tengo una infección?» ⇢ he contraído el virus Influenza A «¿por qué he contraído el virus?» ⇢ tuve contacto cercano con un paciente infectado. ¡Ni siquiera necesitamos 5 preguntas para obtener una respuesta!
De esto se deduce rápidamente que no sólo necesitas un antiviral, sino que la solución para evitar caer enfermo es mantener la distancia social. Por supuesto que este es un ejemplo simple – todos sabemos que nos enfermamos de gripe porque tuvimos contacto con alguien infectado – pero no habríamos llegado a estas respuestas si alguien no hubiera pasado por la “etapa de los por qués» antes que nosotros.
Ten en cuenta que no siempre podemos seguir un pensamiento lineal para encontrar la causa raíz. En algunos casos hay múltiples potenciales causas raíz, lo que nos obliga a explorar las diferentes respuestas a cada «por qué» y a encontrar todas las secuencias posibles. Por ejemplo:
El coche no arranca. ➝ ¿Por qué? ➝ No tiene batería. ➝ ¿Por qué se ha descargado la batería? ➝ Las luces estuvieron encendidas durante horas con el motor apagado. ➝ ¿Por qué estuvieron encendidas? ➝ No hubo ningún sonido de alarma ni ninguna luz de testigo en el salpicadero.
A partir de aquí, nuestro diagrama se divide:
➝ ¿Por qué no hubo alarma? ➝ El sensor falló. ➝ ¿Por qué? ➝ El sensor nunca fue reemplazado.
➝ ¿Por qué no se encendió ninguna luz en el salpicadero? ➝ Hubo un problema eléctrico. ➝ ¿Por qué? ➝ Los fusibles están dañados.
Cuando el análisis de los 5 por qués «se despliega» en muchas posibilidades, casi siempre es un síntoma de que hay fallos en los procesos de calidad y de detección de errores. Nunca olvides que estás analizando el proceso, no las personas, así que no aceptes el «error humano» como la causa raíz. Seguramente hay algún proceso de control de calidad, aunque sólo sea una checklist, que no se ha ejecutado.
En los análisis más complejos, intenta organizar todas las respuestas en un diagrama Ishikawa (también conocido como diagrama de espina de pescado). La combinación de ambos métodos ayuda a visualizar mejor todas las hipótesis.
¿Cómo hacer un análisis de los 5 Por qués?
Explicamos ahora, paso a paso, la manera de hacer un análisis de los 5 por qués en el día a día:
1. Reúne un equipo
Como cualquier otra herramienta de análisis de la causa raíz, este método no debe ser realizado por una sola persona. Reúne a profesionales con un profundo conocimiento del activo, pero que estén dispuestos a mirar el problema desde otra perspectiva y explorar todas las respuestas.
2. Define el problema
Lo ideal sería que todo el equipo pudiera acompañar el problema que se está analizando. Todo el mundo tiene que estar de acuerdo con la descripción del problema. Por ejemplo, todo el mundo debería llegar a la conclusión de que la definición más apropiada del daño es «el coche no arranca» en lugar de «el encendido no arranca», ya que tendría diferentes implicaciones en los siguientes pasos.
3. Empieza a preguntarte «¿por qué?»
Ahora que están todos en sintonía, es hora de empezar a preguntarse ¿por qué? Las respuestas deben coincidir con los hechos, no con las suposiciones sobre lo que pasó. Es probable que no todos los miembros del equipo presenten las mismas respuestas, así que hay que debatir hasta llegar a un consenso.
4. Aprende a parar
No pares demasiado pronto – intenta llegar al menos a 5 preguntas – pero también debes aprender a parar. Cuando las respuestas no ayudan a comprender el daño, o cuando no se dan más sugerencias sobre posibles soluciones, es hora de parar. Si no puedes encontrar una respuesta, prueba con otro método de análisis de causa raíz, como el análisis de árbol de fallos, o FMEA.
5. Planea cambios en tu plan de mantenimiento
Después de completar el análisis, el grupo debería hacer sugerencias sobre lo que se puede hacer para evitar daños similares en el futuro. En esta etapa, puede ser útil examinar de nuevo todas las respuestas para aplicar los procesos de control en las diversas etapas del proceso.
¿Cuándo usar la técnica de los 5 por qués?
En mantenimiento, la técnica de los 5 por qués puede utilizarse en el contexto de un análisis de la causa raíz, para troubleshoot o para resolver un problema. Suele ser bastante eficaz y rápida en determinar la causa raíz en los daños de criticidad baja a moderada. Además, tiene una gran aplicabilidad como herramienta de mejora de la calidad dentro de una metodología lean.
A diferencia de otros análisis, la técnica de los 5 por qués no puede aplicarse en una etapa de concepción. Se limita a descubrir la causa de los problemas que ya han ocurrido y a analizar los fallos que son realmente relevantes. A ese respecto, no hay ninguna «pérdida de tiempo» y no se hacen preguntas hipotéticas.
¿Cuáles son las limitaciones del método de los 5 por qués?
La principal limitación del método de los 5 ¿por qués? es obvia: al seguir una lógica lineal, tiende a llegar a una sola causa raíz. Por esta razón, no es práctico cuando se acumulan varias «vías de investigación» o hay múltiples causas raíz. En esos casos, es preferible hacer un árbol de fallos, que demuestre bien la relación entre los diversos sistemas y fallos, un diagrama de Ishikawa junto con el análisis de los 5 por qués, o incluso un FMEA.
Además de la tendencia a llegar a una sola causa, hay otras desventajas en el método de los 5 por qués, tales como:
1. Dado que sólo evalúa los eventos que ya han ocurrido y es meramente cualitativo, no es apropiado para hacer una evaluación de riesgo;
2. Al igual que la FMEA, depende totalmente del conocimiento de tu equipo para determinar la causa rápidamente. Si se ha producido un modo de fallo inesperado, puede que nunca lleguéis a una conclusión;
3. Tu equipo tiene una visión sesgada, así que pueden crear preguntas y respuestas sesgadas que confirmen sus sospechas o teorías. La falta de exención puede comprometer los resultados del análisis;
4. No siempre es fácil distinguir los «síntomas» de las «causas» y decidir cuándo parar. De vez en cuando, puedes terminar el análisis antes de realizar un análisis completo y minucioso;
5. Por estas razones, diferentes equipos pueden llegar a diferentes resultados partiendo de un mismo daño o pregunta.
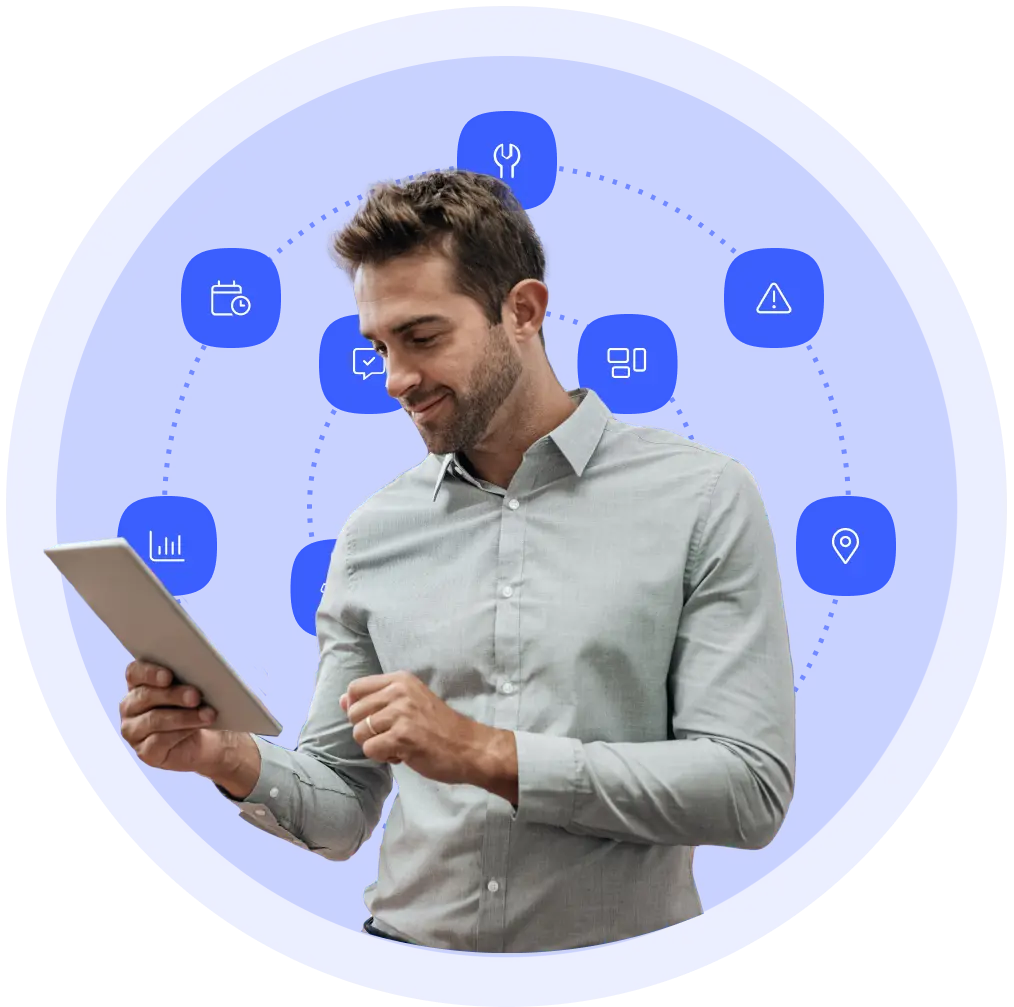