Qué es un análisis FMEA (Análisis de Modos de Fallos y Efectos)?
La sigla FMEA significa Failure Mode and Effect Analysis o, en español, Análisis de Modos de Fallos y Efectos (AMFE). En este contexto, «fallo» significa pérdida de funcionalidad, mientras que «modo de fallo» designa la manera como se produce el fallo. Es una de las herramientas más comunes de análisis de la causa raíz.
Diferencias entre fallo y modo de fallo
Para entender bien la diferencia, veamos un ejemplo sencillo: si un terminal de pago deja de imprimir recibos (fallo identificado) puede ser porque el rollo de papel no está bien colocado (modo de fallo 1) o porque el compartimento no está bien cerrado (modo de fallo 2).
Partiendo de los modos de fallo, podemos llegar a la causa raíz. Sin embargo, el análisis FMEA no se limita a determinar el origen. Esta herramienta se divide en dos partes: primero, la identificación de los modos de fallo (y, por extensión, la posible causa raíz) y luego la evaluación del efecto de ese mismo fallo.
Para entender esta última parte, veamos un ejemplo un poco más complejo. Imagine que una máquina se estropea (fallo) porque el ventilador estaba funcionando con muchas vibraciones (modo de fallo). ¿Qué sucede si se produce este modo de fallo? El equipo se detiene momentáneamente (efecto del fallo), lo que causa pérdidas en la producción.
Diferentes modos de fallo pueden tener diferentes efectos, con consecuencias muy diferentes para el funcionamiento de la empresa. Es por eso que la FMEA a menudo trabaja en conjunto con el análisis de criticidad de activos. Cuando ambos análisis se realizan al mismo tiempo, el resultado se conoce como FMECA, que significa Failure Modes, Effects and Criticality Analysis (Análisis de Modos de Fallo, Efectos y Criticidad).
¿Cuáles son las principales aplicaciones del análisis FMEA?
Y ahora, un poco de historia. El análisis FMEA o AMFE fue desarrollado por el ejército norteamericano en los años 50. Poco después fue adoptado por la industria de la aviación y la NASA, incluyendo en las misiones Apolo, en el desarrollo de las dos sondas Viking y en las misiones interestelares Voyager. La industria del automóvil y la industria petrolera son otros sectores donde el FMEA es habitual.
El análisis FMEA puede ser funcional (centrado en la funcionalidad total del sistema), de procesos (centrado en el análisis de los procesos de producción y montaje) o realizado aún en la fase de diseño/proyecto (principalmente para la gestión de riesgos). Se recomienda hacer un nuevo análisis siempre que se lance un nuevo producto o haya cambios en el funcionamiento de la empresa -cambios en la producción, nuevos reglamentos, etc.- y cuando el feedback de tus clientes informe de un problema recurrente.
¿Cuáles son las ventajas y beneficios de un análisis FMEA?
El objetivo principal de un análisis FMEA es mejorar la calidad, fiabilidad y seguridad de los activos que estamos explorando. Sin embargo, hay una serie de beneficios derivados del proceso de hacer un FMEA en sí mismo:
- Desarrollar un método de trabajo que tenga probabilidades de ser exitoso, seguro y confiable.
- Evaluar los modos y mecanismos de fallo y su impacto, para clasificarlos según la gravedad y la probabilidad de que ocurran (especialmente si se hace un FMECA). Esta lista de prioridades aumenta la eficacia de tu plan de mantenimiento.
- Identificar los puntos de fallo y comprobar la integridad del sistema, cuya seguridad no debe estar comprometida, aunque para garantizarlo sea necesaria la introducción de nuevos modos y medidas de seguridad.
- Comprobar el efecto de los cambios y ajustes en los procedimientos adoptados y en el diseño del equipo (por ejemplo, comprobar si se reduce la probabilidad de fallo).
- Resolución de fallos más rápida, ya que se describen los modos de fallo y sus causas.
- Definir los criterios para las pruebas y comprobaciones que deben incluirse en el plan de mantenimiento preventivo basado en los modos de daño descritos.
¿Cuáles son las limitaciones del análisis FMEA?
Por otro lado, hay algunas debilidades en el análisis FMEA:
- No es adecuado para los sistemas en los que los fallos pueden producirse simultáneamente, ya que no muestra la causalidad o la correlación entre diversos fallos.
- Como veremos más adelante, los tres factores (grado de gravedad/índice de frecuencia/probabilidad de detección de fallos) tienen el mismo peso para el cálculo del riesgo y, desde esta perspectiva, se trata de un análisis muy simplista.
- Es un proceso lento que involucra a muchos profesionales, ya que depende directamente de la experiencia de su equipo para enumerar los diversos modos de fallo.
- Necesita una actualización constante, ya que el conocimiento sobre el equipo aumenta con la experiencia y el uso; se pueden descubrir modos de fallo inesperados que no se tuvieron en cuenta en el análisis inicial.
- Si no se detecta un posible modo de fallo, se subestimará el índice de riesgo de un equipo en particular. Por otro lado, si es demasiado detallado puede dispersar su atención de problemas críticos y desperdiciar recursos.
¿Cómo hacer un análisis FMEA?
La mayor dificultad para hacer un análisis FMEA es la necesidad de ser exhaustivo en cuanto a los modos de fallo, sus causas y su impacto. Lo más común es organizar toda la información en una tabla, en la que recomendamos incluir 7 columnas, una para cada paso.
1. Definir los modos de fallo
El primer paso en un análisis FMEA es definir los modos de fallo para cada componente partiendo de experiencias anteriores con activos similares.
Los análisis de FMEA y FMECA se utilizan comúnmente en industrias peligrosas donde la seguridad es una prioridad. Sin embargo, para el propósito de este artículo, usaremos como ejemplo un plato mal preparado en un restaurante. El ejemplo es de un modo de fallo muy común: encontrar un pelo en el plato. Nuestro crítico Michelin interno distingue también otros tres posibles modos de fallo: encontrar un insecto en el plato, la falta de sal y la intoxicación por salmonela.
Obviamente, un experto en restaurantes conocería muchos más. Este es el gran riesgo del análisis FMEA: no considerar todos los posibles modos de fallo y, como consecuencia, subestimar el riesgo asociado al activo.
2. Describir el efecto del fallo
El segundo paso del análisis FMEA es describir claramente el efecto del fallo en el sistema, ya que este es el factor que determina su gravedad. Intente ser lo más específico posible al describir el efecto del fallo para calcular su impacto en el paso 3.
¿Cuál es el efecto de nuestro modo de fallo? Inmediatamente, devolver el plato. A la larga, no volver nunca más.
3. Impacto ou grado de gravedad del fallo
El grado de gravedad varía de 1 a 10, dependiendo del impacto del fallo:
1 | riesgo nulo: los fallos son casi imperceptibles |
2-3 | riesgo bajo: los fallos son perceptibles pero tienen pocas consecuencias |
4- 6 | riesgo moderado: las consecuencias de los fallos son evidentes (incluso para los clientes) y afectan al rendimiento del activo |
7- 8 | riesgo alto: el funcionamiento del activo está totalmente comprometido, lo que causa una interrupción en el orden del día |
9-10 | riesgo muy alto/crítico: el activo está totalmente comprometido y hay altos riesgos de seguridad |
No sabemos qué opinas, pero para nosotros el activo «plato con un pelo» está totalmente comprometido, con altos riesgos de seguridad e higiene. Lo clasificamos con un 9 (reservamos el 10 para la salmonela).
4. La posible causa del fallo
El mismo modo de fallo puede tener varias causas. Por ejemplo, un ascensor que se detiene entre plantas puede tener un error de configuración o un problema de error eléctrico. Si se enumeran todas las causas potenciales, es más fácil probarlas y corregirlas cuando se produce el modo de fallo.
En nuestro ejemplo, la causa raíz es obvia: los empleados de la cocina no llevan gorro. Si hubiéramos encontrado un insecto en la ensalada, ahí sí, tendríamos varias líneas de investigación: comida mal almacenada, fallo en el lavado, infestaciones, etc.
5. Ocurrencia/ Frecuencia de los fallos
La columna de frecuencia debe dar una indicación de la probabilidad de que ocurra el fallo, de nuevo basada en el historial del activo y equipos similares. Normalmente, el Índice de Frecuencia consiste en una clasificación de 1 a 10, donde 1 representa «nada probable» y 10 «muy probable» o «inevitable».
Basándonos en nuestra experiencia personal, calculamos la frecuencia de nuestro modo de fallo en 2.
6. Cómo detectar el fallo
En esta columna debe proponer medidas sobre cómo detectar el fallo. También debe calcular el Índice de Detección de Fallos –la probabilidad de encontrar el error durante el mantenimiento- donde 1 representa «muy probable» y 10 es «nada probable».
En este caso, la forma de detectar el fallo es hacer una inspección visual del plato antes de llevarlo a la mesa. Pero la inspección visual puede ser bastante -por lo que a menudo no nos damos cuenta del fallo hasta demasiado tarde. Así que, sin querer sumergirnos más en las malas experiencias, calculamos la probabilidad de detectar el fallo en 4, «probable».
7. Índice de Riesgo
El índice de riesgo es el producto del índice de gravedad (calculado en el paso 3), el índice de frecuencia (calculado en el paso 5) y el índice de detección (calculado en el paso 6). Cuanto más alto sea el índice de riesgo, mayor será la necesidad de tomar medidas de mejora.
El índice de riesgo de nuestro plato, por lo tanto, sería 9* 2*4=72. Si le hubiéramos dado ese 10 a la salmonela, con la misma frecuencia y la misma probabilidad de detectar el fallo, el índice de riesgo sería 80 -es decir, un fallo con mayor prioridad en el plan de mantenimiento. Ahora, es hora de que el análisis FMEA pase de la hoja de Excel al mundo real.
📝 ¿Quieres saber más sobre evaluación de riesgo? Lee nuestro artículo sobre cuáles son las diferencias entre un árbol de fallos y un AMFE.
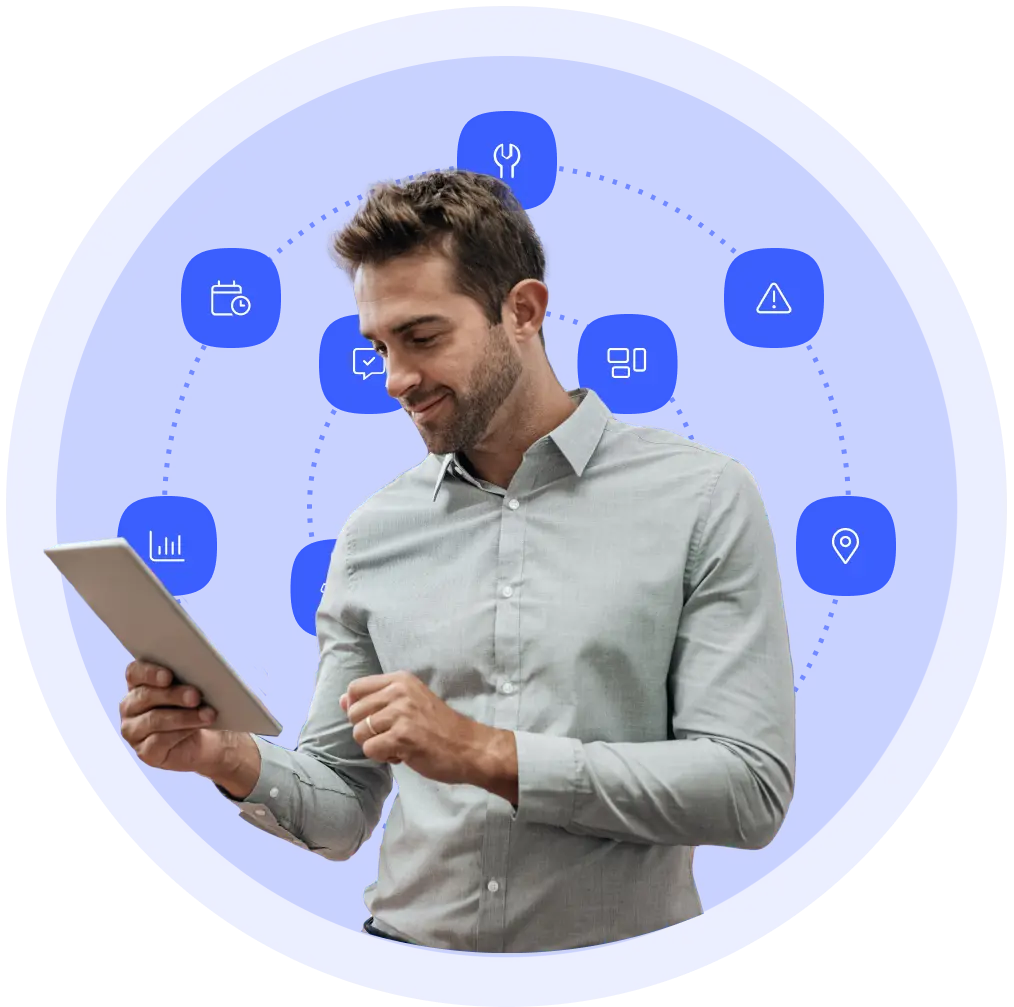