What does DFMEA stand for?
DFMEA stands for Design Failure Mode and Effects Analysis. This acronym encapsulates the process of thoroughly examining the potential failure modes of a product’s design and their effects. The primary goal of DFMEA is to anticipate issues, proactively address them, and ultimately enhance the product’s safety and quality.
DFMEA is a critical tool in the world of product development and safety, since this systematic approach allows organisations to identify and mitigate potential design-related risks before they lead to costly errors in production or, worse, pose threats to consumers.
By integrating DFMEA into the design process, organisations can save costs, reduce risks, and build a reputation for producing reliable and safe products.
Why is DFMEA important?
The importance of DFMEA cannot be overstated. In the competitive world of product development, getting a product to market quickly is essential. However, without the rigorous analysis provided by DFMEA, rushing a product through development can result in costly mistakes. Consider this: design-related issues are much more economical to rectify in the design phase than later in the production process or, even worse, after the product is in the hands of customers.
DFMEA is, therefore, most effective when integrated into the design process from the very beginning. By identifying and mitigating potential design flaws early, you can significantly reduce the chances of costly revisions and safety issues later on.
How does DFMEA work?
DFMEA is a systematic process involving several key steps. It starts with the identification of potential failure modes in the design. Then, the effects of these failure modes are assessed, and the severity of their impact is rated. Additionally, the likelihood of occurrence and the ability to detect the failure mode are evaluated. This data is then used to calculate a Risk Priority Number (RPN) for each failure mode. Actions are taken to address the high-risk items, and the process is iterative, ensuring continuous improvement throughout the design phase.
This is a true collaborative effort, as it involves individuals from various departments, including engineers, designers, and subject matter experts. Cross-functional teams play a crucial role in the success of DFMEA as they bring different perspectives and expertise to the table.
DFMEA Example
Let’s consider a real-world DFMEA example in the automotive industry. Imagine a car manufacturer is designing a new braking system. During the DFMEA process, the team identifies a potential failure mode: brake pad wear unevenly. They assess the effects, which could include reduced braking efficiency and increased stopping distances. The team rates the severity as high, the likelihood of occurrence as moderate, and the ability to detect the issue as low. This results in a high RPN, indicating a significant risk.
To address this, the team might decide to revise the design to ensure even pad wear and implement more rigorous testing procedures. By proactively addressing this design-related issue, the manufacturer avoids potential safety concerns and costly recalls.
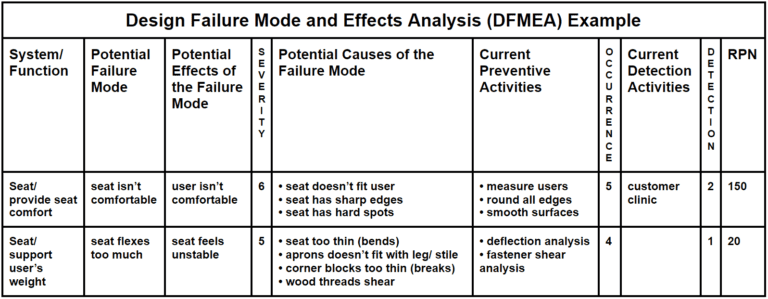
Difference between DFMEA and FMEA
DFMEA and FMEA are closely related but serve different purposes. While DFMEA focuses exclusively on design-related risks, FMEA (Failure Mode and Effects Analysis) encompasses a broader spectrum, including both design and process-related risks. Think of DFMEA as a subset of FMEA, with a more specific focus on design aspects.
Difference between DFMEA and PFMEA
Another distinction to be made is between DFMEA and PFMEA (Process Failure Mode and Effects Analysis). DFMEA, as previously mentioned, addresses design issues, whilst PFMEA deals with potential failures in the manufacturing or production processes. Both are critical for a comprehensive risk management strategy, but they apply to different stages of product development.
Benefits of DFMEA
Early Risk Identification
Since DFMEA is typically conducted during the early stages of product development, it allows teams to identify potential failure modes, their effects, and causes before they become more challenging and costly to address.
Enhanced Product Quality and Safety
By identifying and addressing potential failure modes and their root causes, DFMEA helps improve the overall quality and safety of the product. This leads to products that are more reliable and less likely to fail in real-world conditions, as well as compliant with safety standards and regulations.
Customer Satisfaction
Higher product quality resulting from DFMEA leads to increased customer satisfaction. Fewer defects and failures mean that customers can trust the product to perform as expected and with minimal issues.
Regulatory Compliance
Meeting regulatory requirements is crucial in many industries. DFMEA helps in identifying potential issues that might lead to non-compliance, by addressing these issues early on.
Efficient Resource Allocation
DFMEA enables teams to prioritise their efforts based on the severity of potential failure modes. This ensures that resources are allocated to the most critical issues, rather than spreading resources too thin across all possible failure modes.
Improved Decision-Making
Design Failure Mode and Effects Analysis provides a structured process for evaluating the impact and likelihood of potential failure modes, making way for a data-driven approach that helps in making informed decisions about which issues to address and how to address them.
Continuous Improvement
This is an iterative process. As the design evolves and new information becomes available, the analysis can be updated and refined. The continuous improvement approach ensures that the design remains robust throughout development.
How to perform DFMEA in 10 steps
1. Define System Functions and Requirements
The initial step in the DFMEA process involves breaking down the product design into distinct systems and components, each serving a specific function. These can be organised using a design and function tree, since this visual representation clarifies the relationship between the overall design, individual systems, and their respective functions.
2. Identify System Failure Modes
Next, identify potential failure modes for each system. A failure mode represents a state in which a design doesn’t meet user needs or intended functions.
3. Assess Failure Effects and Assign Severity Ratings
For each failure mode, describe its potential effects and assign a severity rating. Failure effects are the direct consequences of a failure mode, bein severity ratings typically based on predefined criteria, with 1 indicating minimal customer impact and 10 signifying a significant impact on customer safety or regulatory compliance.
4. Determine Failure Causes
After assigning severity ratings to failure effects, investigate the root causes of each failure mode. In some cases, the cause may lie in component function failures; for example, in the manufacturing process of electronic components, such as a printed circuit board (PCB), insufficient solder paste deposition during the surface mount assembly process can lead to poor electrical connection and mechanical weakness.
5. Specify Prevention Controls and Assign Occurrence Ratings
Prevention controls are specific measures taken to prevent the existence of failure causes. Occurrence ratings should be assigned based on the likelihood that a failure cause will persist despite preventive measures, and typically range from 1 (very unlikely) to 10 (very likely), considering ongoing prevention controls.
6. Define Detection Controls and Assign Detection Ratings
Detection controls are procedures aimed at improving the capability to identify failure causes before finalising design drawings and specifications. Assign detection ratings from 1 (highly likely to detect) to 10 (likely to remain undetected even with controls in place).
7. Calculate the Risk Priority Number (RPN)
The Risk Priority Number (RPN) is a key tool in prioritising which design failure modes to address. RPN can be calculated by multiplying the severity, occurrence, and detection ratings. Establishing a pre-defined RPN threshold (e.g. 100 and above) can aid in decision-making regarding which failure modes warrant immediate action, helping teams focus on the most critical failure modes.
RPN = Severity x Occurrence x Detection
For example, if the severity score is 6, the occurrence score is 4, and detection is 4, then the RPN would be 96.
8. Develop High-Priority Recommendations
For failure modes exceeding the RPN threshold, create high-priority recommendations. These recommendations should include specific actions and target completion dates, with designated responsible individuals. Focus on reducing the severity of failure effects or introducing new preventive and detection measures to lower occurrence and detection scores.
9. Document All Actions Taken
Document all actions taken to address the identified failure modes, wicch should include actual completion dates, and update the DFMEA form accordingly, to ensure effective follow-through and progress monitoring.
10. Re-evaluate RPNs for Decision-Making
Finally, re-evaluate the RPNs of target failure modes after implementing actions to improve the design. If the team determines that these actions have effectively mitigated risks, the design can progress in the product development process.
👨💻You may also like: 10 best preventive maintenance software
Most common mistakes in Design Failure Mode and Effects Analysis
While DFMEA is a powerful tool for identifying and mitigating design-related risks, there are several mistakes that can hinder its effectiveness. Understanding these pitfalls is crucial for ensuring the success of your DFMEA process.
Not Involving Cross-Functional Teams
Failure to assemble a cross-functional team is a fundamental mistake. DFMEA requires input from experts in various fields, and without diverse perspectives, critical failure modes may be overlooked.
Incomplete Identification of Failure Modes
Failing to identify all potential failure modes is a significant issue, since incomplete failure mode identification can lead to critical design flaws going unnoticed.
Incorrect Severity Ratings and RPN Thresholds
Assigning incorrect severity ratings or having no pre-defined RPN thresholds can distort the prioritisation of failure modes. It’s vital to ensure that these accurately reflect the potential impact of a failure on customers and safety. Consistent and clear criteria are crucial.
Neglecting Occurrence Ratings
Occurrence ratings determine the likelihood of a failure mode occurring, and neglecting these ratings or assigning them inaccurately can lead to inadequate risk assessment.
Overlooking Detection Controls
Failing to consider and implement appropriate detection controls can result in the continuation of failure causes. These controls are essential for preventing design issues from progressing to the production phase.
Ignoring the Iterative Nature
DFMEA is an iterative, living process, and failing to revisit and update it as the design evolves is a common mistake esigns — designs change, and new risks may naturally emerge.
Lack of Clear Action Plans
Identifying high-priority failure modes without clear action plans is counterproductive, since failing to specify who is responsible for what, and by when, can lead to inaction.
Not Documenting Actions Taken or Monitoring
Documentation is vital for ensuring that corrective actions are completed. On the other hand, neglecting to monitor and review DFMEA throughout the product development cycle means that emerging risks may go unnoticed.
Poor Training
Last but not the leasr, inadequate training of team members in the DFMEA process can lead to errors and misunderstandings. Investing in proper training ensures that the team understands the process and the importance of each step.
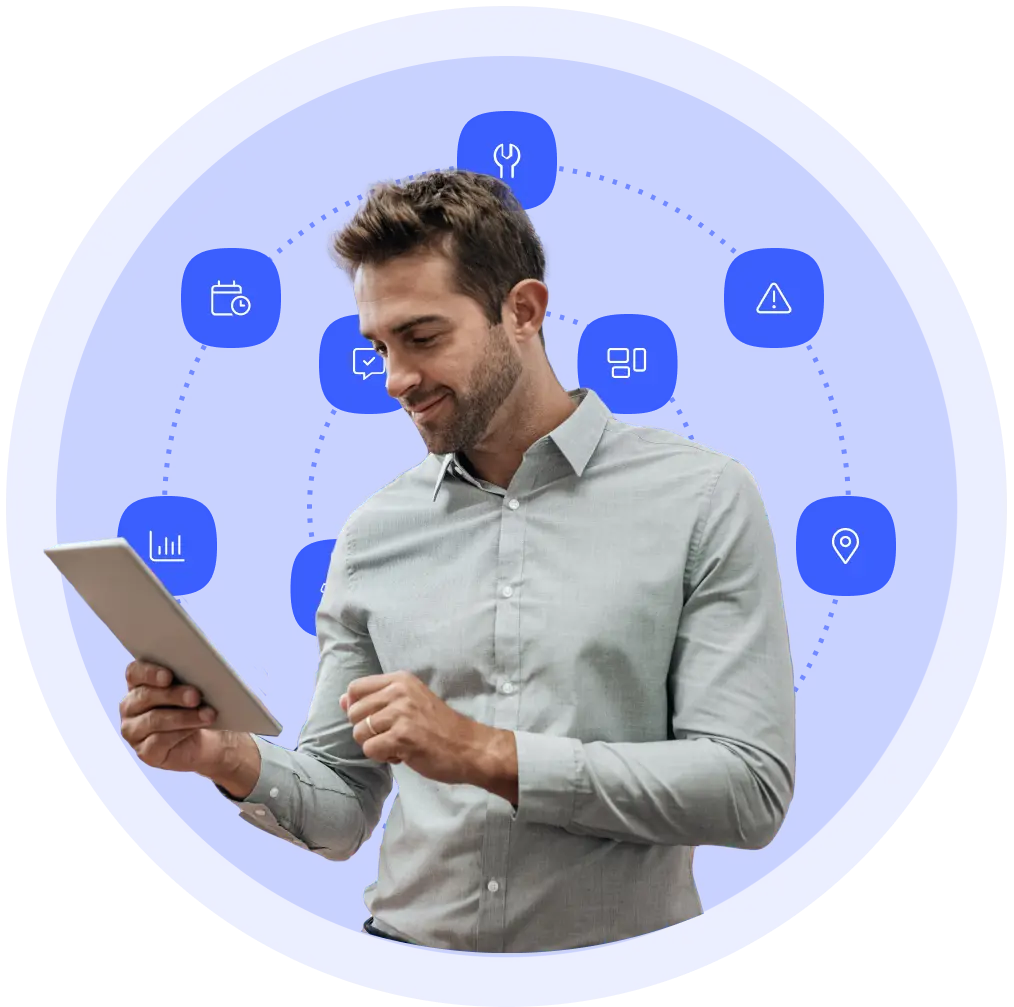