O que significa DFMEA?
DFMEA é uma sigla inglesa que remete para Design Failure Mode and Effects Analysis — análise de modos e efeitos de falha do projeto, em português. Trata-se do processo de examinar minuciosamente os potenciais modos de falha na conceção de um produto e os seus efeitos ou consequências. O principal objetivo da DFMEA é antecipar problemas, resolvê-los de forma proativa e, em última análise, melhorar a qualidade e a segurança do produto final.
A DFMEA é uma ferramenta essencial na fase de conceção dos produtos, uma vez que esta abordagem sistemática permite às organizações identificar e mitigar potenciais riscos, antes que estes conduzam a erros dispendiosos na produção ou, pior ainda, representem uma ameaça para os consumidores.
Ao integrar a DFMEA no processo de conceção do produto, as organizações podem poupar custos, reduzir riscos e construir uma reputação de fabrico de produtos fiáveis e seguros.
Porque é que a DFMEA é importante?
A importância da DFMEA não deve ser subestimada. No competitivo cenário atual, é indispensável colocar produtos no mercado rapidamente, no entanto, sem a análise rigorosa fornecida pela DFMEA, apressar o desenvolvimento de um produto pode resultar em erros dispendiosos. Considere o seguinte: é muito mais barato retificar problemas na fase de projeto, do que mais tarde no processo de produção ou, pior ainda, depois do produto estar nas mãos dos clientes.
A DFMEA é, portanto, mais eficaz quando integrada no processo de conceção, desde o início. Ao identificar e atenuar as potenciais falhas de conceção numa fase inicial, é mais fácil reduzir significativamente a probabilidade de haver correções dispendiosas, atrasos e problemas de segurança mais à frente.
Como funciona a DFMEA?
A DFMEA é um processo sistemático que envolve várias etapas fundamentais. Começa com a identificação dos potenciais modos de falha no projeto. De seguida, os efeitos desses modos de falha são avaliados e a gravidade do seu impacto é classificada. Para além disso, são avaliadas e classificadas a probabilidade de ocorrência e a capacidade de se detetar o modo de falha. Estes dados são utilizados para calcular o Índice de Risco — ou RPN, de Risk Priority Number, para cada modo de falha. São então tomadas medidas para resolver os aspetos de alto risco e o processo é iterativo, assegurando uma melhoria contínua ao longo da fase de conceção.
Trata-se de um verdadeiro esforço de colaboração, uma vez que envolve elementos de vários departamentos, incluindo engenheiros, projetistas e especialistas da área em causa. As equipas multidisciplinares desempenham um papel crucial no sucesso da DFMEA, uma vez que trazem diferentes perspetivas e conhecimentos para cima da mesa.
Exemplo prático de DFMEA
Consideremos um caso real de DFMEA na indústria automóvel. Imagine que um fabricante de automóveis está a conceber um novo sistema de travagem. Durante o processo de DFMEA, a equipa identifica um potencial modo de falha: o desgaste irregular das pastilhas de travão. Avaliam os efeitos, que podem incluir a redução da eficiência da travagem e o aumento das distâncias de paragem. A equipa classifica a gravidade como alta, a probabilidade de ocorrência como moderada e a capacidade de detetar o problema como baixa. Isto resulta num RPN elevado, indicando um risco significativo.
Para resolver este problema, a equipa pode, por exemplo, decidir rever o design para garantir um desgaste uniforme das pastilhas e implementar procedimentos de teste mais rigorosos. Ao abordar proativamente esta questão relacionada com o projeto, o fabricante evita que, no futuro, tenham lugar potenciais problemas de segurança e eventuais recolhas dispendiosas de viaturas.
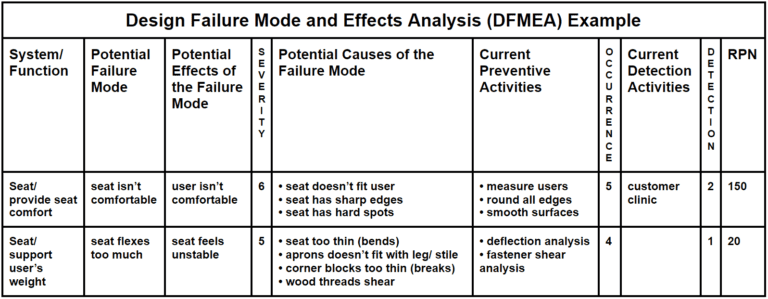
Diferença entre DFMEA e FMEA
A DFMEA e a FMEA são conceitos estreitamente relacionados, mas apresentando objetivos diferentes. Enquanto a DFMEA se concentra exclusivamente nos riscos relacionados com o projeto ou design do produto, a FMEA, de Failure Mode and Effects Analysis, abrange um espectro mais amplo, incluindo riscos relacionados não só com o projeto como também com o processo. Pense na DFMEA como uma componente da FMEA, com um foco mais específico nos aspetos do projeto.
Diferença entre DFMEA e PFMEA
Outra distinção que deve ser feita é entre DFMEA e PFMEA, de Process Failure Mode and Effects Analysis. A DFMEA, como já foi referido, aborda questões de conceção, enquanto a PFMEA lida com as potenciais falhas nos processos de fabrico ou produção. Ambas são fundamentais numa estratégia abrangente de gestão de riscos, mas aplicam-se a diferentes fases do desenvolvimento do produto.
Vantagens da DFMEA
Identificação precoce de riscos
Uma vez que a DFMEA é normalmente realizada durante as fases iniciais de desenho do produto, permite às equipas identificar potenciais modos de falha, os seus efeitos e causas, antes de se tornarem problemas dispendiosos e difíceis e de resolver.
Melhoria da qualidade e segurança do produto
Ao identificar e abordar os potenciais modos de falha e as suas causas principais, a DFMEA ajuda a melhorar a qualidade e a segurança do produto. Isto leva a que os artigos sejam mais fiáveis e menos suscetíveis de falhar em condições reais, bem como garante que estejam em conformidade com as normas e os regulamentos de segurança.
Satisfação do cliente
Uma maior qualidade do produto, resultante de uma DFMEA bem executada, leva a uma maior satisfação do cliente. Menos defeitos e menos falhas significam que os clientes podem confiar que o produto funcionará como esperado e com o mínimo de problemas.
Conformidade regulamentar
O cumprimento da legislação e dos requisitos regulamentares é crucial em quase todas as indústrias. A DFMEA ajuda a identificar potenciais problemas que podem levar à não conformidade, abordando-os e retificando-os numa fase inicial.
Alocação eficiente de recursos
A DFMEA permite que as equipas priorizem os seus esforços com base na gravidade dos potenciais modos de falha. Isto garante que os recursos são afetados às questões mais críticas, em vez de os distribuir de forma indiferenciada por todos os modos de falha possíveis.
Melhoria da tomada de decisões
A análise de modos e efeitos de falha do projeto fornece um processo estruturado para avaliar o impacto e a probabilidade de potenciais modos de falha, abrindo caminho para uma abordagem baseada em dados, o que ajuda a tomar decisões informadas sobre os problemas.
Melhoria contínua
A DFGMA é um processo iterativo, ou seja, recorrente. À medida que o desenvolvimento do produto avança e novas informações ficam disponíveis, a análise pode ser atualizada e aperfeiçoada. Esta abordagem de melhoria contínua garante que o design se mantém robusto durante todo o desenvolvimento.
Como realizar uma DFMEA em 10 passos
1. Defina as funções e os requisitos do sistema
O passo inicial do processo DFMEA envolve a decomposição do projeto do produto em sistemas e componentes distintos, cada um com uma função específica. Estes podem ser organizados através de uma árvore de design e função, uma vez que esta representação visual clarifica a relação entre o projeto global, os sistemas individuais e as suas respetivas funções.
2. Identifique os modos de falha do sistema
De seguida, identifique os potenciais modos de falha para cada sistema. Um modo de falha representa um estado em que a conceção não satisfaz as necessidades do utilizador ou as funções pretendidas.
3. Avalie os efeitos da falha e atribuir classificações de gravidade
Para cada modo de falha, descreva os seus potenciais efeitos e atribua uma classificação de gravidade. Os efeitos da falha são as suas consequências diretas. Por norma, as classificações de gravidade são baseadas em critérios predefinidos, com 1 a indicar um impacto mínimo no cliente e 10 a significar um impacto significativo na segurança do cliente ou na conformidade regulamentar.
4. Determine as causas da falha
Depois de atribuir classificações de gravidade aos efeitos da falha, investigue as causas principais de cada modo de falha. No processo de fabrico de componentes eletrónicos, como uma placa de circuitos impressos (PCB), por exemplo, a deposição insuficiente de pasta de solda durante o processo de montagem em superfície pode levar a uma má ligação elétrica e a uma fragilidade mecânica.
5. Especifique controlos de prevenção e atribua classificações de ocorrência
Os controlos de prevenção são medidas específicas, implementadas para prevenir a existência de causas de falhas. As classificações de ocorrência devem ser atribuídas com base na probabilidade de uma causa de falha persistir apesar das medidas preventivas e normalmente variam entre 1 (muito improvável) e 10 (muito provável), considerando os controlos de prevenção contínuos.
6. Defina controlos de deteção e atribua classificações de deteção
Os controles de deteção são procedimentos que visam melhorar a capacidade de identificar as causas das falhas antes de finalizar o design e as especificações do projeto. Atribua classificações de deteção de 1 (alta probabilidade de detecção) a 10 (provável que permaneça sem deteção mesmo com controlos implementados).
7. Calcule o Índice de Risco (RPN)
O RPN é uma ferramenta fundamental para priorizar quais os modos de falha de projeto que devem ser alvo de maior atenção. O RPN pode ser calculado multiplicando as classificações de gravidade, ocorrência e deteção. Estabelecer previamente um limite de RPN (por exemplo, igual ou maior que 100) pode ajudar na tomada de decisões sobre quais os modos de falha que justificam ação imediata, ajudando as equipas a concentrarem-se nos modos de falha mais críticos.
RPN = Gravidade x Ocorrência x Deteção
Por exemplo, se a pontuação de Gravidade for 6, a pontuação de Ocorrência for 4 e a Deteção for 4, então o RPN seria 96.
8. Estabeleça recomendações de alta prioridade
Para modos de falha que excedam o limite de RPN, crie recomendações de alta prioridade. Estas recomendações devem incluir ações específicas e datas previstas de conclusão, com a designação de pessoas responsáveis. Concentre-se na redução da gravidade dos efeitos das falhas ou na introdução de novas medidas preventivas e de deteção para reduzir as classificações de ocorrência e deteção.
9. Documente todas as ações realizadas
Documente todas as ações tomadas para resolver os modos de falha identificados, o que deve incluir as datas reais de conclusão, e atualize o formulário DFMEA adequadamente, para garantir o acompanhamento eficaz e a monitorização do progresso.
10. Reavalie o RPN para tomada de decisões
Finalmente, após a implementação de ações para melhorar o design, devem ser reavaliados os RPN dos modos de falha identificados. Se a equipa determinar que essas ações mitigaram efetivamente os riscos, pode seguir-se com esse design no processo de desenvolvimento do produto.
👨💻 Também lhe pode interessar: Software de manutenção preventiva: tudo o que precisa de saber
Erros mais comuns na Análise de Modos e Efeitos de Falha do Projeto
Embora a DFMEA seja uma ferramenta poderosa para identificar e mitigar riscos relacionados com a conceção e o design de produtos, existem vários fatores que podem prejudicar a eficácia desta análise. Compreender essas armadilhas é crucial para garantir o sucesso do seu processo DFMEA.
Não envolver equipas multifuncionais
Não reunir uma equipa multidisciplinar é um erro fundamental. A DFMEA requer a contribuição de especialistas em diversas áreas — sem perspetivas diversas, modos de falha críticos podem não ser descobertos.
Identificação incompleta de modos de falha
A falha na identificação de todos os potenciais modos de falha é um problema significativo, uma vez que a identificação incompleta também pode fazer com que falhas de projeto relevantes passem despercebidas.
Classificações de gravidade e limites de RPN incorretos
Atribuir classificações de gravidade incorretas ou não dispor de limites de RPN predefinidos pode distorcer a priorização dos modos de falha. É vital garantir que estes refletem com precisão o impacto potencial de uma falha nos utilizadores, nomeadamente ao nível da segurança. Critérios consistentes e claros são cruciais.
Negligenciar as classificações de ocorrência
As classificações de ocorrência determinam a probabilidade de um modo de falha acontecer e negligenciar essa pontuação ou atribuí-la de forma imprecisa pode levar a uma avaliação de risco inadequada.
Ignorar os controlos de deteção
Desvalorizar e não implementar controlos de deteção apropriados pode resultar na continuação das causas de falha. Estes controlos são essenciais para evitar que problemas de projeto passem para a fase de produção.
Ignorar a natureza iterativa da DFMEA
A DFMEA é um processo vivo e iterativo. Deixar de revisitá-lo e atualizá-lo à medida que a conceção evolui é um erro comum nos projetos – o design muda e novos riscos podem surgir naturalmente.
Falta de planos de ação claros
Identificar modos de falha de alta prioridade sem planos de ação claros é contraproducente, uma vez que não especificar quem é responsável pelo quê, e até quando, pode levar à inação.
Não documentar ações implementadas ou não monitorizar
A documentação é vital para garantir que as ações corretivas foram concluídas. Por outro lado, negligenciar a monitorização e a revisão da DFMEA ao longo do ciclo de desenvolvimento do produto significa que eventuais riscos podem não estar a ser identificados.
Falta de formação
Por último, mas não menos importante, a formação insuficiente ou desadequada dos membros da equipa responsável pelo processo DFMEA pode levar a erros e mal-entendidos. Investir em formação adequada garante que a equipa entende o processo e a importância de cada etapa.
e manutenção
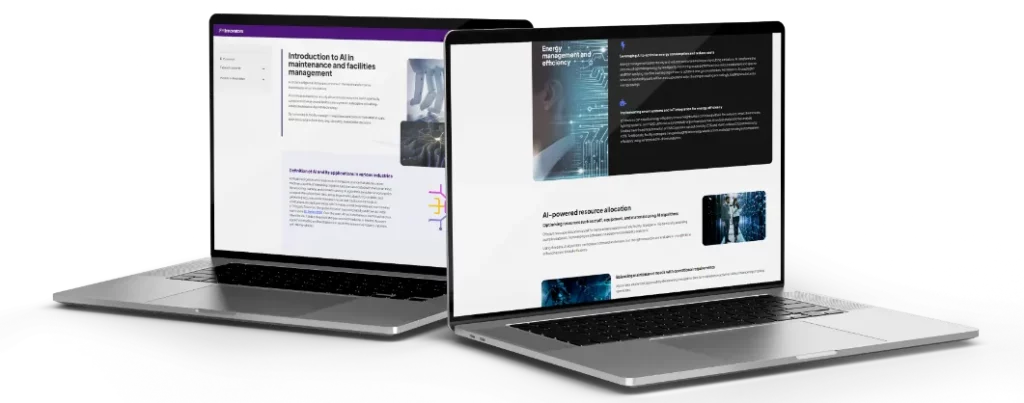