Misinformation about asset maintenance can shorten equipment lifespan and cause unnecessary downtime. Yet, many facility managers still follow outdated beliefs that do more harm than good.
But what if some of the maintenance “rules” you’ve always followed were actually myths?
Is reactive maintenance always more expensive? Does preventive maintenance guarantee a breakdown-free future?
It’s time to separate fact from fiction! In this post, we’ll debunk 10 common asset maintenance myths — so you can make smarter, more cost-effective decisions for your facilities.
Myth 1: “If it is not broken, don’t fix it”
Many firms believe that maintenance is only essential when something stops functioning. 😏 The reason behind this mindset is simple: “Why spend money on servicing equipment that is working perfectly?” To them, it appears to be a needless cost that may be better spent elsewhere.
However, this mistake may lead to reactive maintenance. Plus, it is more expensive in the long run.
Waiting until equipment fails could result in significant disruptions or high replacement costs. Studies reveal that unplanned downtime costs UK businesses an estimated £180 billion per year (Source: The manufacturer)
What data say
Preventive maintenance allows you to spot problems early on and extends the life of your assets.
According to ISO 55000, proactive maintenance can extend asset life by up to 40%.
Myth 2: “New equipment doesn’t need maintenance”
It’s easy to say that newly purchased machinery don’t require maintenance for the first few years. After all, they are brand new, so why worry about servicing them?
But what if we told you that brand-new equipment also experiences stress and minor degradation when it starts operating?
Manufacturers know this, and that’s why they provide specific maintenance schedules. Failure to service those machines could result in increased energy consumption and unplanned failure.
What data say
Predictive maintenance decreases maintenance costs by 12%, improves equipment availability by 9%, and the lifespan of assets by 20% (Source: Infraspeak)
Myth 3: “The more maintenance staff you have, the less downtime you face”
Employing more maintenance staff may seem like the solution to keeping equipment in good shape. It seems logical—if you have more hands on deck, they can repair equipment on time, right?
But in reality, a bigger team doesn’t equal better results.
Imagine a construction site with many workers hanging around, unsure what to do next. Some repeat tasks, others wait idly, and may become confused. The same happens in asset maintenance — without a streamlined system, things could get chaotic. So, instead of increasing headcounts, staff should be equipped with computerised maintenance management systems (CMMS).
What data say
Remote diagnostics improved repair times across various industries. For example, advanced vehicle diagnostic systems have reduced troubleshooting time by 85%
📖 A must-read: 10 best CMMS software in 2025
Myth 4: “Preventive maintenance eliminates all equipment failures”
“If you follow a strict maintenance schedule, your equipment will NEVER spoil.” This is a costly misconception.
Some companies treat preventive maintenance (PM) as a guarantee. They think breakdowns are avoidable if they replace parts on time and stick to routine servicing.
But machines don’t work that way. Even with the best preventive maintenance plan, failures can still happen.
What data say
The UK’s Institute of Asset Management (IAM) reveals that integrating preventive and predictive maintenance can extend the lifespan of ageing assets by 16%.
🧰You should also check out the differences between preventive and predictive maintenance.
Myth 5: “All asset maintenance can be done in-house”
Waiting solely on an in-house team for maintenance is cost-effective, but it can backfire.
While internal technicians can conduct routine servicing, complex systems like HVAC units, electrical grids, and industrial machines need specialised expertise.
If you don’t outsource to certified professionals, errors, extended downtimes, and compliance issues could occur.
What data say
The ISO 45001 occupational health and safety standard stresses the need for qualified experts for high-risk maintenance.
📖Keep your maintenance team on track! Read How to set an HVAC maintenance plan🔧
Myth 6: “Condition monitoring is only for large companies”
There is a common belief that condition monitoring is a luxury only large corporations can afford.
Thus, many small and medium-sized enterprises (SMEs) say investing in vibration analysis and infrared thermography is expensive.
However, advancements in technology and automation make condition monitoring affordable for all businesses. These systems provide real-time data so you can detect early signs of equipment failure.
What data say
A 2013 study by Research Gate found that infrared thermography was highly effective in improving safety, reducing “dangerous points” – and potential failure causes – by 90%.
📝See also: What is condition-based maintenance?
Myth 7: “OEM parts are always the best option”
Although original equipment manufacturer (OEM) components are high-quality and guaranteed by the manufacturer, they are costly and have long wait times.
High-quality parts — sourced from reputable suppliers that meet ISO standards — can perform as OEM parts at a fraction of the cost. Some aftermarket parts offer enhanced durability or improved efficiency compared to OEM options.
What data say
As long as parts comply with ISO 9001 quality management standards, businesses can save money without sacrificing performance or safety.
Myth 8: “Maintenance data isn’t that important”
If you fail to track maintenance data, you are wrong! Without proper record-keeping, you’ll depend on guesswork to schedule maintenance tasks.
Effective maintenance strategies need this data for accurate decision-making.
Tracking machine performance, repair history, or failure rates helps you predict issues before they occur. Likewise, they help anticipate problems before they happen, optimise maintenance schedules, and reduce downtime.
What data say
A study by The British Institute of Facilities Management (BIFM) found that companies using data-driven maintenance achieve 20% lower operational costs.
Myth 9: “Maintenance software is too complicated”
Switching to computer-aided facilities management (CAFM) can be overwhelming.
Some facility managers dislike complex dashboards, interfaces, and hours of training to complete simple tasks. This fear often makes them stick with manul documentation, thinking it’s easier.
However, modern CAFM platforms like Infraspeak are user-friendly, cloud-based, and designed for easy implementation.
What data say
The UK government awarded £1.2 billion in facility management contracts (Q3 2023–Q2 2025), showing the demand for efficient maintenance solutions. Companies using modern CAFM software can stay ahead by streamlining operations. 🚀 (Source: Statista)
👉 Read the article: CAFM vs CMMS – differences and similarities👈
Myth 10: “Maintenance doesn’t affect energy consumption”
Do you think ignoring maintenance causes equipment to go faulty only? Not at all. It silently inflates your utility bills.
Dirty filters, misaligned machinery, and poorly lubricated components make machines work harder than usual. In the end, they’ll consume more power and increase energy bills.
In short, neglecting maintenance isn’t just bad for your equipment — it’s terrible for your finances, too.
What data say
According to the Carbon Trust UK, proper maintenance can improve energy efficiency by up to 20%, reducing carbon emissions and operational costs.
🔰Learn how to reduce your company’s energy expenses
🔹 Real-World Impact: Work. Life’s Energy-Saving Strategy
Work.Life manages 16 coworking spaces and used to track maintenance manually. However, they needed a more innovative way to monitor energy usage to meet B Corp’s sustainability goals. With Infraspeak, they now monitor energy in real-time across all locations. Likewise, they ensure 100% renewable energy compliance.
Explore Work. Life’s maintenance transformation in this case study.
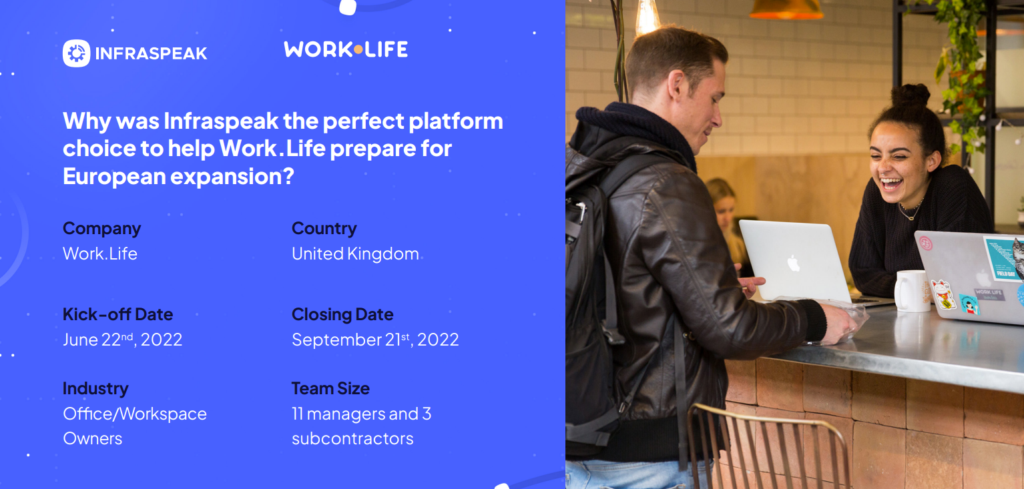
Rethink maintenance — take action today!
Now that we’ve debunked these 10 asset management myths, it’s time to take action.
Stop letting outdated beliefs hold your operations back. Infraspeak makes maintenance smarter, simpler, and more efficient.
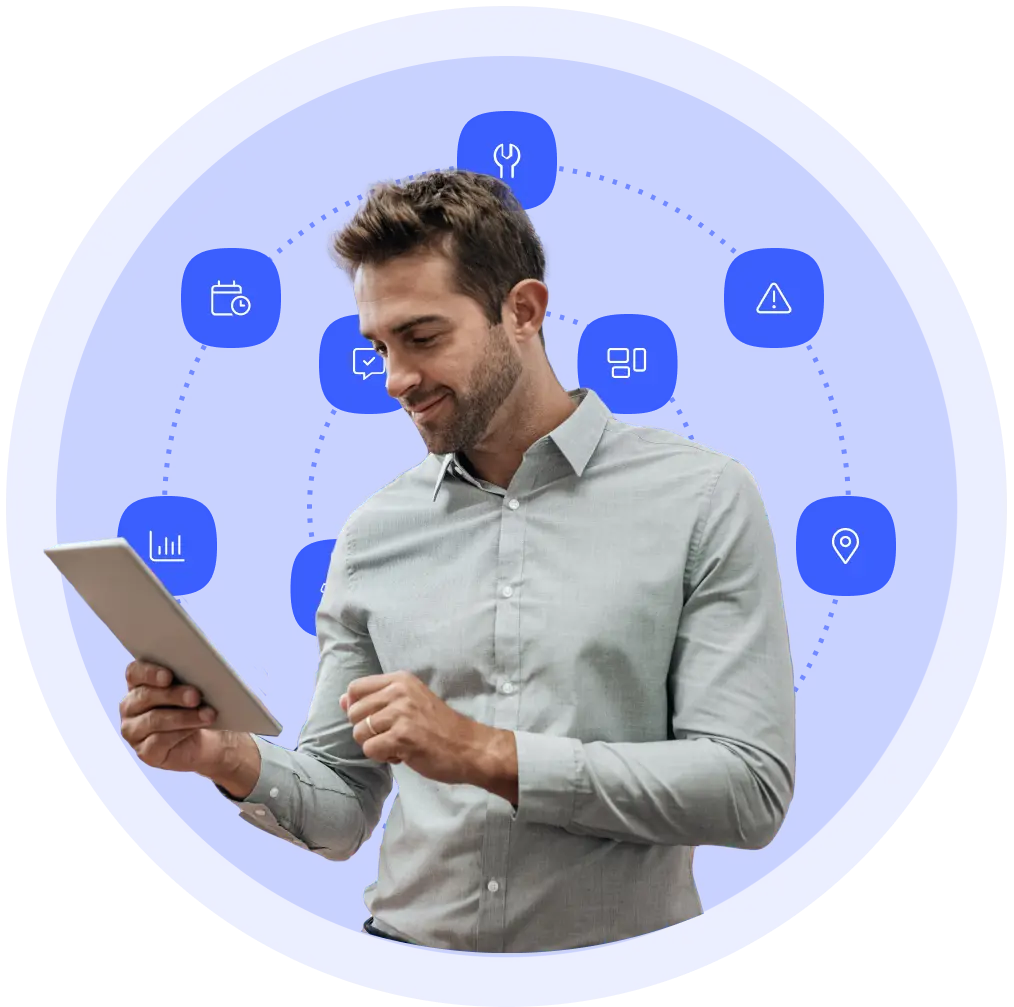