What is a Standard Operating Procedure?
SOP means Standard Operating Procedure. An SOP document provides instructions on how to perform routine tasks to improve efficiency and compliance with quality standards, as well as standardising processes.
SOPs are used in almost all industries, including retail (e.g., chain stores), services, and, of course, maintenance management.
Why implement an SOP?
You should consider implementing SOPs if:
- you manage too many clients;
- you have a large number of employees;
- the performance of the company is not consistent;
- you’ve struggled to implement agile processes;
- your operations include several repetitive tasks.
What are the advantages of an SOP document?
✔️ Increase compliance
The use of SOPs allows the implementation of best practices in each sector and stimulates compliance with international guidelines such as ISO standards. Thus, you can save resources, minimise problems, and increase efficiency.
✔️ Standardise processes
One of the main advantages of creating an SOP is increasing the consistency of the service you provide to your customers. Operations become a well-oiled machine, agile and faster, with specific procedures to make decisions and react to each obstacle.
✔️ Facilitate the onboarding
Another advantage of SOPs is making the employee’s training and onboarding easier. Even if there is someone new on the team, all they need to do is follow the SOPs to perform the work order successfully.
✔️ Preserve knowledge
Let’s imagine that you don’t have problems with compliance, that your processes are all streamlined and that you don’t have any challenges to train new technicians. In that case, is there any advantage to SOPs? Yes, because they’ll preserve the (excellent) know-how that you acquired for the future.
Remember to centralise information. SOPs should be accessible to all team members. Otherwise, people will go back to their old ways. Use a maintenance management platform to centralise all information and automatise processes.
How to prepare an SOP document
1. Choose the procedures that need an SOP
First, make a list of the tasks and processes that are part of your usual operations. Then, choose which ones best qualify for an SOP, taking into account your objectives and the advantages we mentioned earlier.
2. Define the document structure
An SOP doesn’t have to be too formal. It can follow a simple structure — e.g., a summary, task description and associated documents. However, you can also choose the structure proposed by the ISO 9000 standard, which is a bit more detailed:
- name of the procedure;
- purpose;
- reference documents;
- acronyms/glossary;
- responsibilities;
- scope and application;
- health and safety measures;
- list of revisions and amendments.
3. Prepare and write the SOP
When you’re preparing the document, keep the end-user in mind. That being:
- focus on the job and responsibilities of the user;
- choose an adequate writing style and vocabulary, avoiding overly technical terms with which staff are unfamiliar;
- explain everything that is required at each step, but don’t overexplain. There are no advantages in worrying the user with technical specifications that don’t affect their work.
Besides that, you should be careful with how you organise the information itself. SOPs must be scannable and easy to browse, and key information cannot be “hidden” in long paragraphs. These are the three most common formats in maintenance SOPs:
Checklists
Checklists are one of the most common formats used by maintenance teams to standardise processes. They are an excellent option for work orders with short instructions.
Checklists are widely used in preventive maintenance, either in “free” format (in which the order of the tasks is not relevant, as long as all the items are performed) or in a “step-by-step” format, with an established order. If you want to give detailed instructions for each step (e.g., “replace filter”, followed by an explanation on how to do it), consider preparing a hierarchical SOP instead.
Hierarchical lists
When there are too many instructions for each step, it is preferable to organise the information in sections and subsections. Hierarchical SOPs divide the text into several points (1., 1.a, 1.b) and are suitable for complex processes or processes with safety hazards, such as installations and set-ups.
Hierarchical procedures are also useful to train and guide new staff members, especially in industries with high turnover. Furthermore, it is possible to incorporate some decisions “what if/when“, as long as the solutions are limited. For processes with several variables, a diagrammatic scheme is more suitable.
Flow chart
When the sequence varies according to the results of each step, flow charts are the best method to explain all the variables. This type of chart is appropriate for troubleshooting and reactive maintenance, for example.
Depending on the failure, the chart can either instruct the operator to solve the problem by themselves or report the fault to technical assistance. The charts are also used by maintenance teams to assess priority, plan the repair, decide if it is going to be performed on-site or at the workshop, and consistently offer the same level of service.
4. Review the final document
After you’ve finished, walk through the process. Is there anything missing? If you had never done a similar job before, could you complete it? Do the instructions cover all the possibilities? If you are pleased, you can implement these documents in your internal processes.
5. Optimise an SOP
Nothing remains the same forever. You will need to update your SOPs as maintenance practices evolve. You can also make updates as challenges and doubts arise over time. We recommend reviewing your SOPs every six months to make a risk assessment and verify which tasks can be automated.
⚙️ Why not use an intelligent maintenance management platform to centralise all information and automatise processes? Ask for a quick demo with our team!
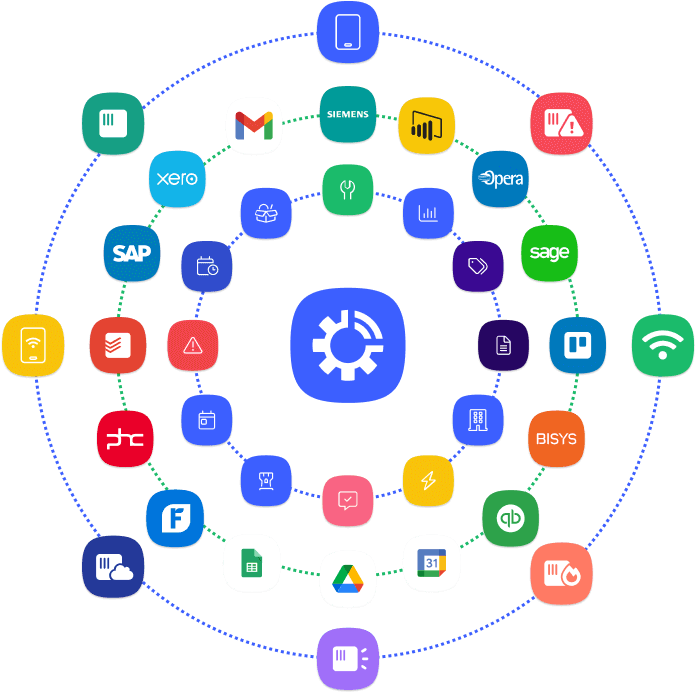