Total Productive Maintenance, or TPM, is a lean maintenance strategy that aims for zero breakdowns, zero defects and zero work accidents. We’ve already introduced TPM, what it is, who is responsible for it, its numerous advantages, and how it fits into Industry 4.0.
However, to succeed at such an ambitious plan, we need solid pillars. That brings us to the 8 pillars of TPM, or the 8 basic principles of TPM. Implementing them is not only key to enable TPM but also to ensure it will last.
What are the 8 Pillars of Total Productive Maintenance?
1. Focused Improvement
Focused improvement is the first pillar of TPM. The priorities are clear: improve, improve, and improve continuously. To avoid the loss of equipment, talent, raw materials, and energy, the whole team must share this vision. The team must be proactive, willing to try new methods, and eager to sit around the table to work out problems.
📝 Read more about using Kaizen for continuous improvement in TPM and lean manufacturing.
2. Autonomy
Autonomy is the second pillar of TPM, in the sense that every team is an autonomous “maintenance agent”. Everyone has the autonomy to clean, inspect, and contribute to the upkeep of the assets they work with. This ensures every piece of equipment is cared for, improves early fault detection, and frees maintenance technicians for heavier tasks. Learn more about autonomous maintenance and how to implement it.
3. Quality Maintenance
One of TPM’s biggest goals is manufacturing zero defective products, which, undoubtedly, also plays into customer satisfaction. Hence, quality management and implementing internal processes linked to quality control are another pillar. We recommend several root cause analysis tools to root out problems.
4. Planned Maintenance
Planned maintenance – whether it is planned reactive maintenance or preventive maintenance – is the best way to avoid downtime and breakdowns. Keep every asset up and running to ensure quality and avoid customer complaints (for B2C), and improved compliance (for B2B service providers). Programmed maintenance that requires machines to shut down should be done after regular work hours.
Learn more on how to avoid downtime and reactive maintenance.
Download our free whitepaper to learn about:
- The most common causes for reactive maintenance (with data from multiple studies);
- How to reduce your downtime, 8 different ways.
- 5 tips to reduce your MTTR when breakdowns do happen.
5. Early Equipment Maintenance
Early equipment maintenance is one of the 8 pillars of a well-succeeded TPM strategy. When it’s time to choose new equipment or develop new products, consider previous experiences to make maintenance easier. This can be as simple as choosing a washable paint for the walls (which makes cleaning easier), or as complex as picking a robot which can self-diagnose malfunctions (which improves production).
6. Training and Education
TPM requires investing in training and education. Otherwise, it’s impossible to trust each worker with routine maintenance or prevention. For TPM to work, basic maintenance knowledge about assets used daily is non-negotiable. Besides, when you think about how fast technology evolves, continuous training is the only way to make sure your technicians are familiar with new equipment and the state-of-the-art of the industry.
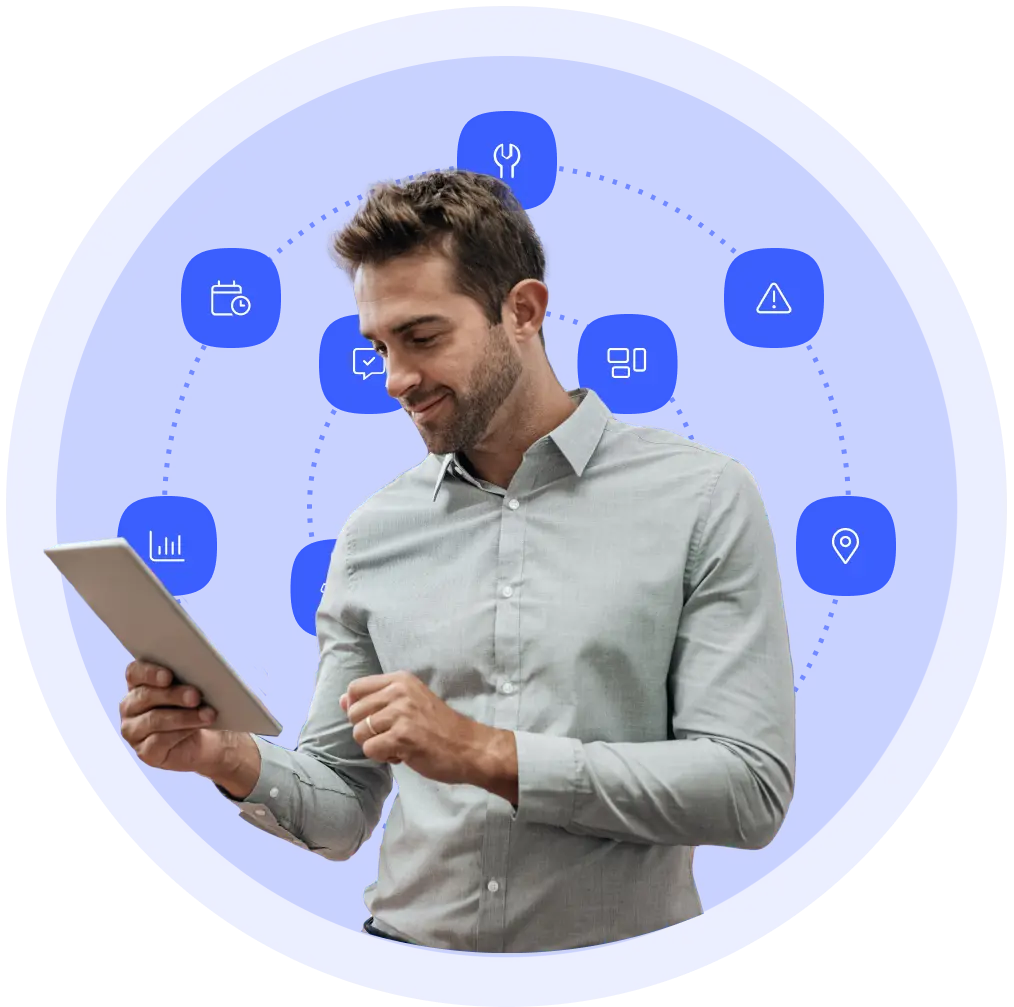
7. Safety, Health and Environment
TPM also aims at zero work accidents, zero pollution, and zero burnout. Good maintenance management not only avoids accidents during maintenance activities but also contributes to every worker’s well-being and safety.
Estimates suggest about 53% of all cancers in Europe are related to professional activities, usually due to exposure to asbestos, benzene (used in rubbers, lubricants, dyes, detergents, and pesticides, for example), chromium, nickel, silica powder (common in mining activities, quarries, glue and paint factories), radiation and fumes. Proper maintenance of equipment and buildings can help to reduce these statistics.
8. Office TPM
The last of the 8 pillars is office TPM. This means administrative workers and managers should also chip in, instead of leaving it to the “worker bees”. Everyone, without exception, must be proactive and focused on improvements, from logistics to scheduling.
Find out more about Total Productive Maintenance (TPM) here.