Maintenance departments are vital across various industries, including manufacturing, healthcare, and energy. They ensure that equipment operates efficiently, which is essential for employee safety and the firm’s overall productivity.
For instance, in manufacturing, regular maintenance prevents machinery breakdowns, reducing downtime and production delays. Similarly, in healthcare, well-maintained equipment is crucial for patient care, while in the energy sector, maintenance ensures uninterrupted power supply.
However, these departments have faced persistent staffing challenges over the last couple of years. Pertinent surveys reveal that over 30% of maintenance and facilities managers struggle to find skilled technicians and mechanics, leading to manpower shortages. Looking ahead, projections indicate a global shortfall of up to 2 million skilled maintenance workers by 2025, underscoring the urgency of addressing this issue.
While such predictions are based on industry-wide movements, that’s not to say that there aren’t ways to circumvent such trends. To understand the optimal path for your organisation, let’s first discuss what might be the cause of your firm’s maintenance segment’s prevalent staffing issues.
Why do maintenance departments face staffing issues?
Staffing issues in maintenance departments stem from a combination of global challenges that disrupt workforce stability and growth — meaning, it might not be all your company’s leadership’s fault. Currently, the five biggest obstacles include:
- an ageing workforce,
- the shortage of skilled technicians,
- the rapid adoption of complex technologies,
- the difficulty of attracting younger talent, and
- limited training opportunities.
These challenges are interconnected, creating a cycle that impacts productivity and operational efficiency. Making matters worse, they can appear in unison to hinder a company’s workflow resulting in missed deadlines. Hence, understanding the underlying causes of each issue is crucial to addressing them effectively and securing the future of maintenance departments worldwide.
Global effects of an ageing workforce
As experienced technicians retire, there’s a shortage of qualified individuals to take their place. In the United States, around 7% of the labour force is age 65 or over, more than double the rate from two decades ago and substantially higher than at any point in U.S. history going back to the 1850 Census. As these experienced employees retire, they take with them valuable skills and institutional knowledge, creating gaps that are difficult to fill.
Similar challenges are evident amid Europe’s aging workforce, compounded by demographic shifts and complex sociopolitical factors. The working-age population in many European countries is shrinking due to low fertility rates and increasing life expectancy. For instance, Germany would need to attract up to 400,000 migrants annually to maintain its workforce, a task complicated by global competition for skilled workers.
These challenges highlight the difficulty in balancing workforce sustainability with public sentiment, leaving Europe’s maintenance departments struggling to retain experienced talent and find suitable replacements.
Prevalent shortage of skilled technicians
According to a 2024 survey, 53% of skilled U.S. tradespeople identified a lack of qualified candidates as their top challenge, highlighting the ongoing difficulty in filling these essential roles. 39% of the respondents highlighted the lack of knowledge sharing and collaboration on the job site (down from 42% just one year prior), while 30% noted an influx in coworkers retiring (up from 28% in 2023).
This deficit is not limited to one region: countries like Australia are also grappling with significant shortages. The nation needs an additional 32,000 electricians by 2030 to meet its infrastructure demands, reflecting a broader global trend.
The implications of this shortage are far-reaching, affecting productivity and operational efficiency. As experienced technicians retire, the gap left behind becomes increasingly challenging to fill, increasing the need for effective solutions to attract and train new talent in the maintenance sector.
Evolving complexity of modern machinery
While modern machinery has indeed become increasingly sophisticated, integrating advanced technologies that enhance performance tends to also complicate how maintenance tasks are performed. Technicians now need expertise in automation, robotics, and computer systems to effectively service equipment — all areas that weren’t necessarily synonyms with maintenance half a decade prior. This shift demands continuous learning and adaptation, even via bespoke maintenance software.
The rapid pace of technological advancement often outstrips the training programs designed to prepare technicians. Many educational institutions struggle to update their curricula to keep pace with industry needs, resulting in a skills gap among graduates. Consequently, maintenance departments find it difficult to recruit personnel proficient in the latest technologies.
This skills gap leads to increased reliance on external specialists or vendors for maintenance tasks, which can be costly and may introduce delays. Additionally, the pressure on existing staff to upskill can lead to burnout and job dissatisfaction.
Issues with attracting younger maintenance professionals
Nowadays, misconceptions about the financial prospects in maintenance careers further deter young talent. A significant number of young people underestimate the earning potential in skilled trades, with only 42% expecting skilled trade workers to earn at least $50,000 annually. In reality, many skilled trade workers with less than ten years of experience earn at least $50,000.
The demand for flexible working arrangements is another factor impacting the appeal of maintenance careers to younger professionals. Many workers, especially from younger generations, prioritize work-life balance and seek roles that accommodate their lifestyle needs. Unfortunately, the maintenance sector often operates on rigid schedules, with 24/7 availability required in some cases, making it less attractive compared to industries offering remote or flexible work options.
📩 Access our FM & Maintenance Compensation and Salary Report
Lack of effective training opportunities
Studies indicate that 74% of employees feel they aren’t reaching their full potential due to a lack of development opportunities. In time, this seemingly superficial issue can evolve into a festering problem leading to decreased productivity and increased turnover rates.
Companies that invest in pertinent training programs do see substantial benefits, however. Organisations with strong training initiatives report a 24% higher profit margin compared to those without.
Additionally, employees who receive proper training are 15% more likely to be promoted, highlighting the importance of continuous development.
Despite these advantages, many maintenance departments still lack structured training programs. This deficiency can result in increased downtime, higher maintenance costs, and a greater risk of equipment failure.
What can maintenance department heads do?
The great variety evident among the above issues points to several methodologies that you can apply within your firm’s management department to alleviate staffing issues before they take hold. For instance:
Strategies to attract younger workers into the maintenance field
Consider taking advantage of the popularity of today’s digital channels. Social media recruitment, for instance, has proven to be a powerful tool, with nearly 75% of employees aged 18–34 finding their most recent job via these platforms. By leveraging platforms like LinkedIn, Instagram, and TikTok, you can not only reach a broader audience but also present a more dynamic, forward-thinking brand that appeals to younger generations.
Another key strategy is emphasising continuous learning and skill development opportunities, particularly through eLearning. Younger generations, especially Millennials and Gen Z, seek roles where they can grow both personally and professionally. For example, you can incorporate video content into your recruitment and training strategies, enhancing engagement and appeal to younger workers. Platforms like Veed, a great CapCut alternative, offer AI text-to-video features that enable the creation of professional, engaging videos without requiring advanced editing skills.
Next, make the most of online courses. They help employees gain new technical skills, especially with the growing reliance on advanced technologies in maintenance, while also enhancing team collaboration by standardising technical language across all levels of the workforce. Thus, you can build a more skilled, adaptable, and cohesive team, all while fostering a work environment that values continuous improvement and employee satisfaction.
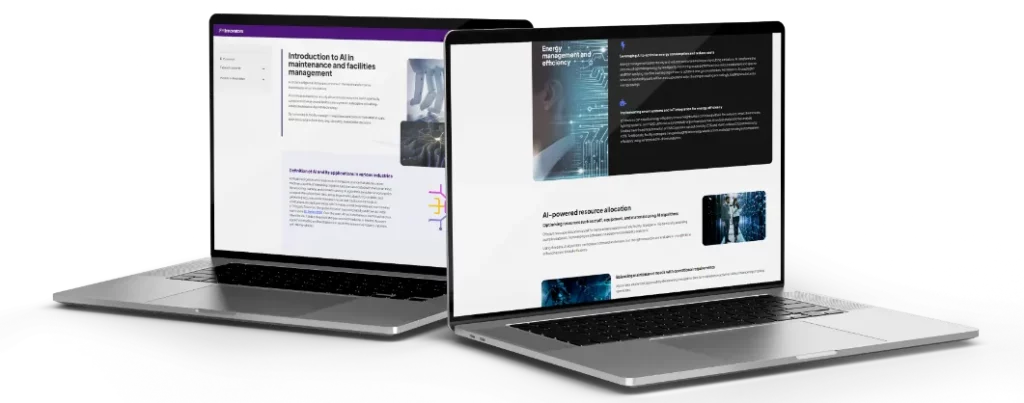
Overcoming skilled labour shortages
By consolidating resources, maintenance teams can benefit from shared expertise and streamlined processes, leading to improved efficiency and productivity. Facilities operations specialists highlight how centralised maintenance helps create a more unified training and development strategy across teams, allowing employees to receive consistent and effective training regardless of their location.
This approach not only fills gaps in technical expertise but also fosters a more adaptable workforce, enabling teams to meet increasing demands despite staffing shortages. Tying to the previous points, by focusing on fostering a positive work environment you can attract and retain talent, particularly in maintenance where skilled workers are in high demand.
So, strive to create a culture that prioritises employee satisfaction and well-being. That way, your department’s employees will feel motivated to grow within the company, rather than seeking opportunities elsewhere.
Offer learning opportunities and competent employee benefits
Research indicates that 70% of knowledge workers believe that increased workplace learning would boost their productivity and engagement, with two-thirds more likely to stay with a company that invests in their growth. Such an implementation could be the key to improved maintenance performance, as well as raising that segment’s body count.
Implementing structured training programmes equips employees with the skills necessary to perform their duties efficiently and safely. A study by the Center for American Progress found that turnover can cost organisations anywhere from 16% to 213% of an employee’s annual salary, highlighting the financial impact of inadequate training and high turnover.
Offering competitive benefits, such as health insurance, retirement plans, and professional development opportunities, demonstrates a commitment to employee well-being. That said, employer-of-record providers make managing employee benefits hassle-free by streamlining the entire process, saving you valuable time.
The solutions are available. It’s about committing to them and promoting empathy alongside excellence as a core company value.