Additive Manufacturing is one of the technologies linked to Industry 4.0. Together with big data analytics, the Internet of Things (IoT), cyber-physical systems, simulations, augmented reality (AR) and virtual reality (VR). But what is additive manufacturing, and how does it work? What improvements can it bring for maintenance and facility managers? And what are the differences between 3D printing techniques?
What is additive manufacturing?
Additive manufacturing is also known as 3D Printing. How does it work? A printing machine reads a computer file layer by layer and prints each layer. In the end, all the layers build a 3D object.
In the beginning, 3D printing was mostly used to create prototypes. Now, it’s changing manufacturing and maintenance. In particular, for maintenance and facilities, it can improve inventory and stock management. It can also extend the useful life of older assets, as we’ll see.
Additive Manufacturing: real life examples
Companies like Siemens and General Electrical have been using additive manufacturing for a few years now (Siemens opened a 3D printing facility in Sweden in 2016 already). They can repair burner tips 60% faster than they used to, and cut repair times for turbines by 90%.
Deutsche Bahn (German Railways) also uses 3D printing for at least 100 parts that are hard to procure and render trains unavailable, which can send the company back thousands of euros every day. Now, parts weighing 13kg can be printed in 7 hours, decreasing downtime and financial losses. These companies are leveraging modern technology and integrating other PLM tools such as Windchill with their enterprise systems in a bid to establish, fine-tune, and optimize additive manufacturing capabilities. They can also expand access to their product data, making sure that the printed 3D models match their expectations.
For most companies, however, additive manufacturing in maintenance is still something of the future. Imagine never waiting for parts to arrive, and printing them at your own facility, at your own pace. This is especially important for customised parts, which have the longest waiting times.
Let’s take a look at the advantages and disadvantages of additive manufacturing.
Advantages of Additive Manufacturing
- Faster repairs, which leads to a smaller MTTR, greater availability, and a better OEE. With the quick turnaround, production and maintenance cycles become shorter.
- It reduces inventory costs, as you don’t have to keep parts in storage “just in case” – you can make them “just in time”. Besides, printing precise entire components also cuts assembly costs.
- You can print anything, even if it’s for old equipment and spare parts are no longer in production. We will no longer replace entire assets simply because the original parts have been discontinued. This extends the lifespan of equipment and its return on investment.
- Parts can be reverse-engineered and redesigned to be compatible with older equipment, but with a few tweaks to make them more efficient. Since ageing equipment is one of the biggest challenges European managers face, this has the potential to be a game-changer.
- Companies with printing equipment on-site become less dependent on their suppliers and can customise parts and products easily. Additive manufacturing provides unlimited design freedom.
📝 Read also: The role of Predictive Maintenance in enhancing manufacturing plant safety
Disadvantages of Additive Manufacturing
Sounds too good to be true? Well, printing machines are not instant pudding. They may take their time to print whatever you need. But that’s still likely to be faster than transportation, not to mention more sustainable. Besides, you need to have prototypes ready to go – a digital stockroom of sorts.
- Additive manufacturing is cost-effective once it’s implemented, but it’s expensive in the beginning. Machines can cost €0.6 up to €1.5 million. Raw materials, like metal powder, are expensive as well.
- Therefore, additive manufacturing will not be a cost-sensible option for smaller components until this technology becomes less expensive.
- Machines need to become more productive in order to be faster and accommodate different types of parts.
- Since it’s still (relatively) new, there are no industry quality standards yet. You’ll need to discuss every detail with your supplier.
A way around initial investment: outsourcing 3D printing Having a machine ready to print in your own facilities seems ideal. However, if you cannot afford machinery, you might outsource 3D printing. Start with a 3D scanner to create CAD files of important parts, and get a third party to print them. Although this won’t eliminate lead times, it will still allow you to print customised or discontinued parts. |
3D Printing Techniques
If you’re imagining a gigantic printer, there’s a little more to it. Despite being relatively new, there are already several 3D Printing techniques. These are the most common 3d printing techniques in maintenance:
- Selective laser melting (SLM) and Direct metal laser melting (DMLM). A layer of metal is laid onto a plate in the printer. The printer will read a CAD file, and a high-powered laser melts the powder. The component is then built layer by layer. It has a high degree of accuracy, which makes it appropriate for precise work and saves time on application.
- Laser metal deposition (LMD). Like SLM and DMLM, LMD uses metal powder to print. The difference is that the powder, instead of being laid on a plate, is injected directly into the beam of the laser. As a result, it’s able to print parts much faster, although with less precision. Technicians will need to adjust parts on their own, which will delay application.
- Electron beam melting (EBM). Instead of a laser, EBM uses an electron beam. It’s similar to SLM in efficacy, but EBM can only be used with a limited number of metals.
We can’t wait until prescriptive maintenance diagnoses a failure and automatically orders the system to print a part in 3D. But, in the meantime, we’re focused on building an Intelligent Maintenance Management Platform that automates your work as much as possible. Schedule a meeting to see how Infraspeak can help you.
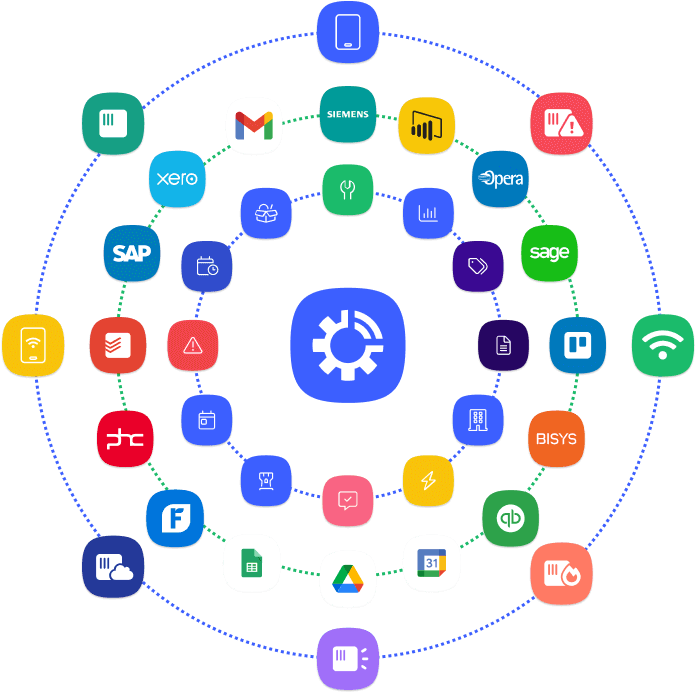