If the corporate world were an ocean, Facility Management (FM) would be an octopus: a skilful creature able to manage multiple limbs simultaneously. From equipment safety to the management of employees, the responsibilities of a facility manager can be quite a handful.
In the UK, the Health and Safety at Work Act 1974 is the legal document that establishes the duties and regulations employers must abide by to guarantee a safe work environment. The role of Facility Management is to maintain statutory compliance with that document.
The importance of statutory compliance
Statutory compliance vs regulatory compliance: what is the difference?
There are two main kinds of business compliance: statutory compliance and regulatory compliance. The difference between statutory and regulatory compliance lies in who passes the law.
Statutory laws are set out by the government, whereas regulatory compliance is overseen by other bodies. Statutory conditions are the basis of regulatory laws, and the latter can never overwrite the former.
What happens if you don’t comply with health and safety rules in the UK?
Non-compliance means you become liable to a series of risks that can compromise not only your business but the integrity of its core: your workers. Note that no harm needs to be done to commit a criminal offence. A single non-compliance – depending on the risk it poses – is enough to get verbal or written advice, a prohibition notice, or be prosecuted. If the HSE needs to interfere, you’ll need to pay a fee.
Now may be a good time to remind you health and safety fines are proportional to the size and turnover of the business. On average, health and safety fines in the UK are £150.000, and over £50 million fines are issued every year.
Facilities Management compliance checklist
In the UK, there are several statutory requirements. Here at Infraspeak, we certainly don’t want you to feel lost whilst navigating this sea of rules and regulations, so we comprised a checklist with the general Health and Safety legislations that apply to businesses in Great Britain.
Health and Safety at Work
- Employers need to carry out a risk assessment. If the company has five or more employees, it needs to record the significant findings of the assessment.
- After the risk assessment, employers must implement health and safety measures according to the findings. These measures should be planned and carried out by a facility manager or other competent people.
- Set up emergency procedures and train employees accordingly.
- If your company deals with hazardous materials, other regulations may apply.
📝 See here how to make a risk assessment at work according to the Health and Safety at Work Regulations from 1999. We’ve also covered how to carry out a risk assessment for maintenance and facility management employees.
Fire Regulations
- Fire Safety Order 2005
- The building must have fire risk assessments and evacuation plans. You need to carry out at least one annual drill and record the results. Every person in the building must be aware of all emergency procedures.
- Fire alarms: inspected every six months.
- Emergency lighting: daily examination (e.g. is it on?), monthly check (e.g. does it work during an outage?), and annual inspection (e.g. does it work uninterruptedly for three hours?).
- Fire extinguishers: monthly visual checks, and an annual inspection by a competent person (you must keep a permanent record of all maintenance).
Hazardous Substances Regulations
- Control of Substances Hazardous to Health (COSHH)
- Hazardous substances – such as chemicals, mixtures, dust, gases, fumes and biological agents – require assessments.
- The employer must provide safety data, control measures, and appropriate equipment and training for all employees exposed to those substances.
Work Equipment Regulations
- Provision and Use of Work Equipment Regulations 1998 (PUWER)
- The equipment has to be suitable for its intended use, maintained in a safe condition, inspected periodically, and used only by people who received appropriate training.
- PUWER concerns any equipment workers may use, for example, photocopiers, ladders, water boilers, etc… Keep in mind that each piece of equipment has different inspection periods.
Electricity Regulations
- Electricity at Work Regulations 1989
- Employers must consider the placement, construction, installation and appropriate use of electrical systems.
- When it comes to electrical instalments/fixed wire, the inspection periods are every five years for commercial use, every three years for industrial use, and once a year for emergency lighting and fire alarms.
Asbestos Regulations
- Control of Asbestos Regulations 2012
- It is mandatory to test for asbestos, check for its condition, implement a control strategy and keep an updated risk assessment.
- The UK outlawed the use of asbestos in 1999, so if your building dates before 2000, asbestos surveys are mandatory.
- If the removal is necessary, it must be performed by a professional.
Gas Regulations
- Gas Safety Installation and Use Regulations 1998 (GSIUR)
- The law states that you must repair and maintain gas pipework, flues, and appliances in a permanent safe condition.
- Each piece of equipment and duct shall undergo an annual safety check carried out by a licensed technician who can provide certification.
Water Regulations
- Legionella Risk Assessment (LRA) is mandatory for water systems and is valid for two years.
- You need to be especially cautious if the temperature of water systems is between 20ºC-45ºC, the water recirculates (ex.:showers), the system produces breathable droplets, and if the conditions are favourable for bacterial growth.
First Aid Regulations
- Health and Safety (First Aid) Regulations 1981
- If a worker falls ill or gets injured at work, the employer must provide equipment, facilities and personnel to ensure immediate first aid.
👨💻 Suggested readings: A guide to the BACS decree for tertiary buildings and Health and Safety file: a comprehensive guide
Beware these are only some of the laws that fall under the spectrum of operations in FM. Some regulations are tied to the type of business one’s talking about; if you work at a creative agency, it is unlikely you have to worry about complying with the Working at Height Regulations 2005. If you need help, check the HSE guide for your industry.
How to improve Facilities Management compliance
Maintaining statutory compliance often relies on preventive maintenance and scheduled tasks. In fact, the great explorer Erasmus may have accidentally etched the motto for the job in 1500 by stating: “Prevention is better than cure”.
However, planning for emergencies, assessing risks, keeping maintenance on schedule, and saving and maintaining correct records is hardly something you can organise on Excel sheet tabs.
Given the number of things you need to monitor, it’s easier if you do it with the right software. Using just one platform to plan scheduled tasks, assign tasks automatically and receive deadline notifications will increase compliance and avoid hefty non-compliance penalties.
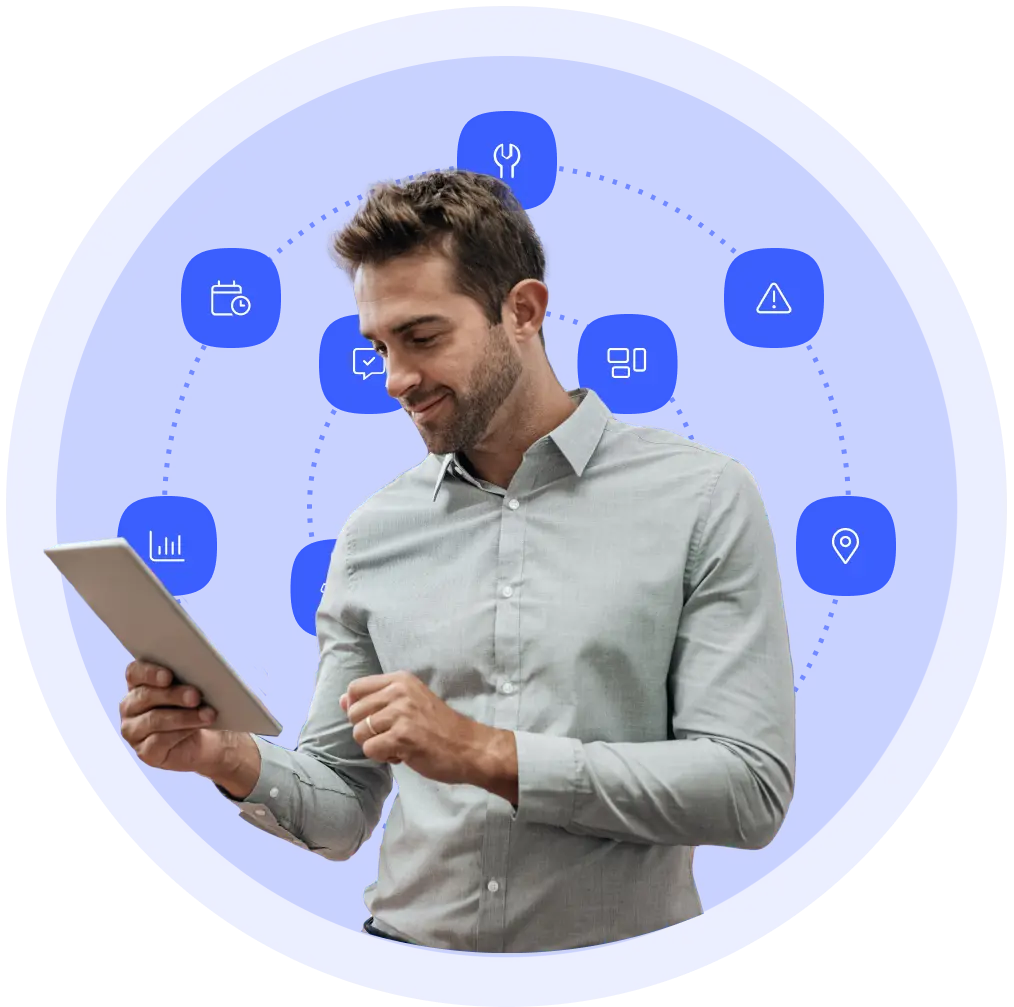