The maintenance industry is rapidly evolving worldwide and the United Kingdom is no exception — maintenance service provider teams have to constantly adapt to new trends and technologies to meet increasingly high expectations with less time and resources available. But what are the main operational challenges and priorities for maintenance teams in the UK?
Infraspeak spoke to 50 British maintenance managers to understand what their main challenges are at the moment and what reasons they believe are behind them, as well as their priorities for the upcoming years.
Paper… still?
Even though the UK is ahead of their continental European counterparts in terms of digitalisation — paper dependency is still one of the main issues reported by Spanish and Portuguese maintenance managers —, some managers in the UK still consider paper to be an issue, though the problem is not so much the wastage, but the excessive bureaucracy.
Multiple respondents say that spending less time doing paperwork is one of their main priorities (one respondent estimating that they spent more than half a day on paperwork per week!), especially for creating/managing work orders and building reports.
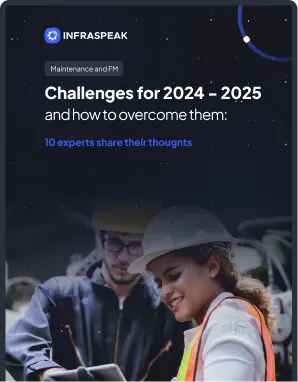
Data Analysis and Report Building
In fact, building reports is where most maintenance teams seem to fall short. Customers are increasingly demanding in regards to the data they want to be given, but gathering and working all that data can be tricky for those without an adequate maintenance management software (CMMS), with the two main reasons behind those struggles being (1) the lack of data centralisation and (2) relying on technicians to work on the data and do the paperwork.
Regarding centralisation, some managers find themselves having trouble collating and analysing all the data that they receive from multiple sources, as a consequence of having contractors who use different software with no integrations, while some others have built (or are currently working on building) their own databases to gather data. As for the latter reason, multiple respondents acknowledge that getting good enough data is a constant challenge, either because the people in charge of providing and/or managing data aren’t those with the right set of skills (electricians, mechanical engineers, etc.), or because contractors tend to sacrifice paperwork and data analysis for the need to work fast and efficiently.
For larger facility management companies, there’s even more to it: since these companies tend to be fragmented into various services lines that are each individually run like smaller businesses, the data is not centralised and it’s harder to combine and analyse with a wider scope. Besides, the employees whose job it is to input the data usually don’t know what’s valuable and what isn’t, so they end up putting in everything, making the data less reliable.
The importance of operational control
After data treatment and reports building, control over the team and operations was the most commonly reported challenge by the respondents. In fact, many consider this to be the most vital thing to improve business profitability, since it means that technicians work in the most efficient and reliable way possible. Some managers expressed concerns that without a proper tracking system, contractors skip jobs and do not actually fulfill their obligations. Management systems with technology such as NFC can help mitigate these concerns by allowing managers to keep track of what equipment or location tags are actually scanned. But lacking a CMMS or using an inappropriate system for their operations are still very present issues among the respondents.
Current technology use
When asked about their use of dedicated technology, the majority of managers report already using a CMMS. However, the outlook is still far from ideal — close to 23% don’t use maintenance management software yet, relying on tablets with spreadsheets, or (yes, you guessed it!) paper. Among those using a CMMS, some report inadequacy of their current solution. For instance, one respondent felt their current software was targeted at gas engineers and had to tweak it to fit their operation the best they could.
Those who are currently in the process of adopting a CMMS emphasize the importance of being able to integrate it with other software and the need for flexibility and margin for customisation when it comes to building reports in order to meet different customers’ needs or demands.
In a nutshell…
While relatively advanced in terms of digitalisation, the maintenance and facilities management industry in the UK still has a lot of paperwork and bureaucracy to get over. Many teams still spend excessive time managing work orders and especially building reports, mostly due to a lack of the right technology, having data that’s too disperse, or not getting good feedback from technicians. Many believe controlling technicians is one of the biggest challenges to improving business profitability and acknowledge the need for an adequate tracking system for managers to stay on top of their teams’ actions. Finally, while most respondents use a CMMS, some report they’re not completely satisfied with their software in terms of fit or flexibility.
–-
Find out how Infraspeak can help maintenance managers solve most of these problems and achieve their goals with its total flexibility, comprehensiveness and the use of NFC technology.