The Facilities Management (FM) sector is undergoing a profound transformation. Increasing pressures to do ‘more with less’ — notably fewer personnel due to labour shortages — combined with increasingly stringent legislation — hello, decarbonisation targets! — and evolving client expectations, are forcing industry leaders to rethink strategies.
Traditionally characterised by reactive approaches and manual processes, FM now needs to leap towards more intelligent, flexible, and collaborative models. This guide provides a clear vision of the future of FM, identifies current sector challenges, and presents solutions for those who refuse to be left behind.
The FM Iceberg: beyond what’s visible
Traditionally, each open and completed work order involves different people, numerous (often lost!) exchanged messages, and various associated manual actions. For every defined maintenance plan, there are hours spent analysing scattered information, and managing each asset involves a series of slow steps and poorly informed decisions.
In other words, the visible work is just the tip of the ‘FM iceberg.’ Beneath the surface lies a vast layer of essential aspects — team performance, supplier management, compliance, SLA compliance, customer and user satisfaction, operational risk management, etc. — shrouded in a haze due to outdated procedures. When there is no complete visibility into what lies beneath the waterline, making strategic decisions, optimising resources, or predicting problems becomes impossible.
Bringing operational efficiency to the surface in FM
Just as ‘you can’t make omelets without eggs,’ achieving desired efficiency in FM is impossible without the right tools. In other words, there are no future-ready facilities management operations without intelligence. Even today, in many companies, FM decisions continue to be made based on intuition or outdated reports. Manual processes drain time and increase the risk of error, while the potential of data remains underutilised.
The good news is that the industry is changing. The adoption of tools with integrated intelligence is transforming reactive operations into proactive, sustainable, and scalable processes.
📄 You may also like: How Sotécnica reduced administrative work by 87%
It all starts with data
Structured, centralised, real-time data is the foundation of intelligence in facilities management. But data without action is just noise. Intelligence lies in what we do with that data — in the clarity it brings, the decisions it guides, the work it automates, and the time it saves.
The role of automation and AI
This is where technology comes in — through platforms that collect, centralise, and process operational data, it’s possible to turn them into concrete actions. This translates into:
- automation of repetitive tasks, saving time and reducing overload;
- more informed and secure decisions;
- better performance and state of assets, thanks to predictive insights;
- less time spent ‘putting out fires’ and more focus on what truly matters.
With connected systems, real-time data, automation, and artificial intelligence, FM teams are finally getting the tools they need to lead rather than just react, and:
- make the entire ‘FM iceberg’ visible;
- break down silos by giving everyone in the FM ecosystem access to the same data;
- create alignment through shared visibility;
- enable data-driven strategic decisions — not assumptions.
Intelligence isn’t just about technology — it’s about fostering collaboration, clarity, and strategic thinking.
Advantages of Intelligent FM
Reduced operational costs
With the right technology, it’s possible to reduce maintenance costs by up to 25%, according to a Sustainability magazine study on AI applications in FM.
Increased asset availability and operational efficiency
According to a 2024 Gartner report, 40% of FM team time was spent on administrative tasks, but with inherent automation in intelligent FM, this time can be redirected to critical decisions and strategic work.
Resource optimisation
By more efficiently scheduling maintenance tasks and allocating resources according to asset priority and criticality, intelligent facilities management allows for more effective use of labour, parts, and work time.
Improved strategic planning
By providing detailed data on asset performance and maintenance costs, intelligent FM facilitates long-term strategic planning and informed decision-making on asset and resource investments.
Continuous and predictive monitoring
Technological tools help anticipate failures, improve asset lifecycle management, and ensure compliance. The Sustainability study cited above also concluded that AI can achieve over 90% predictive accuracy in detecting equipment problems and estimating energy consumption.
Condition monitoring is an integral part of intelligent FM, allowing for real-time data collection, continuous monitoring of asset conditions, and detection of any signs of deterioration or potential failure. Data obtained through condition monitoring is stored in advanced analytics systems capable of identifying patterns, trends, and anomalies that can alert to future problems, thus allowing them to be avoided.
Interconnected systems and real-time data
Integration between software allows for a global and instantaneous view of operations.
Challenges of Intelligent Facilities Management
- System integration: Implementing technologies like IoT and AI may require integrating complex systems, which can be a challenge for some organisations.
- Human resource training: Practicing intelligent FM often requires company employees to become familiar with new technologies and processes, which may require significant investment in training.
- Data security: With the collection and analysis of large volumes of data, concerns about the security and privacy of information arise, requiring additional data protection measures.
“We must not forget that the need to establish a more human-centred way of doing facilities management is a challenge in itself. We need to start thinking of collaboration as a means to work smarter and more resiliently, building stronger relationships that lead to lasting results. And this requires the use of intelligent technology.” – Luis Martins, Founder and CTO at Infraspeak
Collaboration: the key to unleashing FM’s potential
Collaboration in FM goes beyond internal teams. Everyone is called upon to occupy their place in a common workspace: managers, technicians, suppliers, subcontractors, building users, and even regulatory entities. However, much of the sector’s companies still operate in fragmented environments, with scattered data and ineffective communication.
This lack of alignment among all involved has consequences:
- delays in interventions;
- risk of non-compliance;
- high costs in supplier management;
- compromised employee motivation;
- low customer satisfaction;
The solution lies in implementing collaborative platforms, like Infraspeak, with shared workflows, real-time accessible data, and the possibility of integration with systems like BMS and ERP.
Still have doubts about the potential of collaborative and intelligent software? Check out these average numbers achieved by companies that chose Infraspeak:
- 83% decrease in average repair time
- 66% reduction in unexpected expenses
- 91% improvement in compliance levels
- 60% of administrative work automated
All thanks to the advanced capabilities of the software, which offers a shared workspace and simple, agile communication channels, centralising information and keeping everyone informed of the situation at all times.
Flexibility — because in FM, change is constant
In the unpredictable world we live in, rigid models no longer suffice. Flexibility in FM is a competitive advantage and increasingly a prerequisite for responding to new demands, regulations, or changes in the workplace — consider, for example, the challenges posed by the COVID-19 pandemic, with remote and hybrid work suddenly leaving facilities empty.
The 3 pillars of a flexible operation
- Customisable and scalable systems: Based on a modular platform that adapts to each team’s reality and allows for integrations with IoT, BMS, ERP, and other tools.
- Transparency and collaboration: Allowing for the sharing of information with all stakeholders, from suppliers to facility users.
- Proactive compliance: Continuously and automatically monitoring assets, ensuring legal compliance, enabling real-time audits, and data-driven risk management and predictions.
Infraspeak Gear™: Intelligence that works
Challenges, changes, demands — this is the daily life of a facilities manager. To navigate such turbulent waters, these professionals need to rely on the right technology. It’s time to introduce you to Infraspeak Gear™.
The result of 5 years of continuous development, Infraspeak Gear™ is the intelligent engine of the Infraspeak platform, designed to make FM more efficient, strategic, and flexible.
Benefits of Infraspeak Gear™
- Reduces administrative burden: Fewer repetitive tasks, more time for what matters — with Infraspeak, you can save up to 8 hours per week per user.
- Provides total collaboration: Everyone involved has access to information, and communication is agile.
- Facilitates asset monitoring: Allows for continuous tracking of assets based on history and automatic measurements.
- Enables better decision-making: With data analysis and real-time reports and suggestions, decisions are faster and fact-based, avoiding errors and failures.
- Offers scalability: Its modular design and powerful integration capability with other systems allow it to adapt to your specific needs and the growth of your operation.
Such benefits mean that, in practice, Infraspeak Gear™ has the ability to:
- Automate according to ‘if-this-then-that’ logic.
- Analyse data, create reports, and suggest actionable insights — 75% of Infraspeak users claim to apply these suggestions!
- Create and send automatic alerts — notifying, for example, when an asset does not have an assigned PPM.
“Infraspeak Gear™ is not a trendy technological product — it is the operational heart of our platform, tested in the field to solve real problems.”
The time for intelligent FM is now
The era where ‘putting out fires’ was the main function of facility managers and their teams due to workload overload, lack of comprehensive operational insight, and lack of clear and effective communication, is over. The age of intelligent facilities management has arrived — a new paradigm in maintenance management, consisting of:
- Total visibility and control
- Cross-functional collaboration
- Actionable data
- Operational flexibility
Teams that embrace this change will not only increase efficiency but will also ensure the sustainability and competitiveness of their organisations. And the best part? It starts with a simple step: accessing intelligence that works.
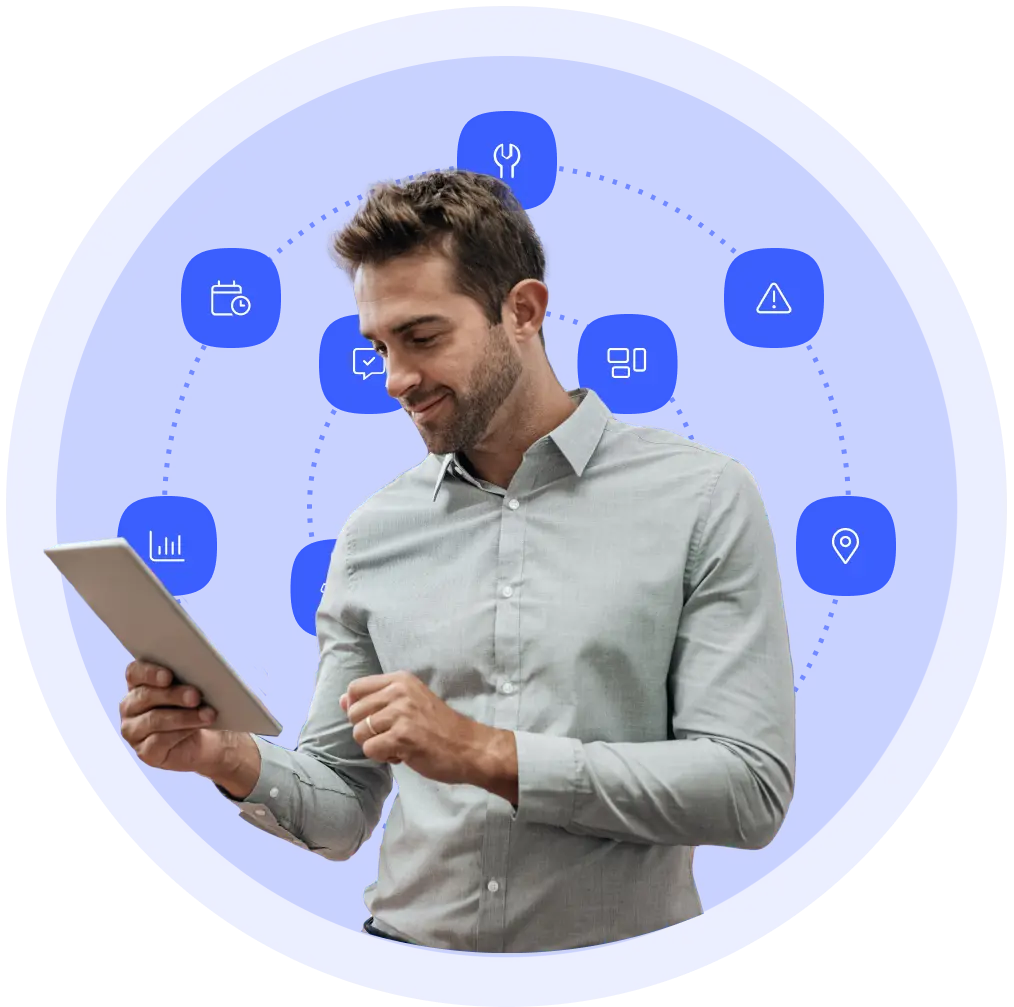