Workwear compliance refers to adhering to laws, regulations, and industry standards that dictate the type, quality, and use of clothing worn by employees in specific work environments. These rules exist to protect workers from hazards like chemical exposure, extreme temperatures, or physical injuries while ensuring operational consistency.
Compliance with workwear regulations is important for the following reasons:
- Prevents workplace injuries: Properly designed and maintained workwear reduces the risk of accidents, aligning with the goals of regulatory bodies like the Occupational Safety and Health Administration (OSHA).
- Avoids legal penalties: Adhering to standards helps sidestep fines, lawsuits, or shutdowns arising from non-compliance, protecting the organisation financially and legally.
- Protects reputation: Consistent compliance demonstrates a commitment to safety, enhancing trust with employees, clients, and regulators while avoiding the reputational damage tied to violations.
- Boosts worker confidence: When employees know their workwear meets high standards, they can focus on tasks without worrying about personal risk, improving morale and productivity.
Emerging trends in workwear for compliance and worker safety
The landscape of workwear is changing, driven by technological advancements, sustainability concerns, and shifting workforce needs. It’s about much more than picking a pair of comfortable work pants. Facilities managers should stay informed about these trends to anticipate compliance updates and enhance worker safety.
Smart workwear
Wearable technology is making its way into uniforms. Sensors embedded in clothing can monitor vital signs, detect hazardous gases, or track fatigue levels. Smart personal protective equipment (PPEs) also collect valuable data that facility managers can analyse to identify trends and optimise safety protocols. These innovations improve safety and may soon become part of compliance mandates as regulators recognise their value.
Sustainable materials
Environmental pressures are pushing industries toward eco-friendly fabrics, like recycled polyester or biodegradable textiles. While sustainability isn’t yet a universal compliance requirement, it’s gaining traction in regions with strict environmental regulations, influencing procurement decisions.
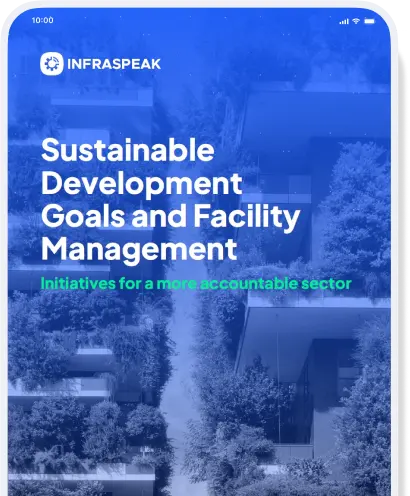
Ergonomic design
Modern workwear prioritises comfort and mobility without sacrificing protection. Lightweight, breathable fabrics and adjustable fits reduce strain during long shifts, addressing safety and worker well-being — a growing focus in compliance frameworks.
Antimicrobial and easy-clean fabrics
Post-pandemic, hygiene has taken center stage. Workwear with antimicrobial coatings or materials designed for frequent washing without degrading is increasingly common, especially in healthcare and food processing, where cleanliness ties directly to compliance.
These trends reflect a broader shift — workwear is no longer just protective gear but a dynamic tool for safety, efficiency, and adaptability. Facilities managers who track these developments can better prepare for what’s ahead.
How facilities managers can ensure workwear compliance
Stay updated on regulations
Laws and industry standards evolve. Regularly review guidelines from relevant authorities — such as OSHA, International Organisation for Standardisation (ISO), or local agencies—to ensure workwear aligns with the latest requirements.
Conduct risk assessments
Identify workplace hazards specific to your facility, like machinery risks or chemical exposure. Match workwear specifications (e.g., cut-resistant gloves and flame-retardant jackets) to these risks, ensuring they meet or exceed compliance thresholds.
Train employees
Compliance isn’t just about providing the right gear; it’s about proper use. Train workers on how to wear, maintain, and inspect their workwear. For example, a hard hat with a cracked shell fails compliance, but untrained staff might not notice.
Partner with reliable suppliers
Source workwear from vendors who provide certified, standards-compliant products. Request documentation — like certificates of conformity — to verify quality and avoid counterfeit or subpar items.
Maintain and replace gear
Workwear degrades over time. Set schedules for inspecting and replacing items like worn-out boots or faded high-visibility vests to maintain compliance and workplace safety.
Document everything
Keep records of purchases, training sessions, and compliance checks. This proves adherence during audits and helps identify patterns that could signal deeper issues.
Preparing for the future of workwear compliance
Looking ahead, facility managers must anticipate how workwear compliance will evolve and position their facilities to adapt. The future will likely bring stricter standards, new technologies, and greater accountability. Here’s how to prepare:
Embrace technology
Invest in or pilot smart workwear solutions. As these become mainstream, early adopters will have an edge in meeting future mandates. Start small, perhaps with sensor-equipped vests in high-risk areas, and scale up as benefits emerge.
Build flexibility into budgets
Emerging trends like high-tech or sustainable workwear may carry higher upfront costs. Plan for gradual upgrades by allocating funds annually and balancing immediate needs with long-term investments.
Engage with Industry networks
Join professional associations or forums where compliance updates and best practices are shared. Peer insights can reveal what’s coming, whether it’s a new PPE standard or a shift in enforcement priorities.
Monitor global trends
Workwear compliance isn’t static or uniform. A regulation introduced in the European Union, like stricter chemical resistance rules, could eventually influence standards elsewhere. Keep an eye on international developments to stay proactive.
Involve workers in planning
Employees who wear the gear daily can offer practical feedback. Their input — on comfort or durability —can guide decisions that align with compliance and usability, fostering buy-in for new initiatives.
Prepare for audits
Future compliance may involve more frequent or detailed inspections, especially as data-driven oversight grows. Establish robust tracking systems now, such as digital logs of workwear issuance, to streamline audits later.